【壓縮機網】氯氣壓縮機中間冷卻器泄漏的原因有很多,涉及設備材質選擇、設備加工、設備安裝、工藝指標控制,特別是氯氣含水量的控制及酸霧的控制、氯氣中間冷卻器的冷卻介質即循環水的制備工藝等。本文將從氯氣壓縮機氯氣處理開始介紹,在整個氯氣處理直至氯氣壓縮后輸送過程中,各個過程安裝及控制對氯氣中冷器壽命可能造成影響的因素。氯氣的洗滌、冷卻、干燥、除霧、壓縮過程統稱為氯氣處理,也會對氯氣中冷器壽命造成影響。
1、氯氣處理工藝流程簡介
由離子膜電解槽出來的溫度約為85-90℃的高溫氯氣,在電解工序通過鈦列管式換熱器與二次鹽水工序的精制鹽水進行換熱,冷凝下來的氯水流至離子膜電解氯水罐,用氯水泵打入脫氯淡鹽水塔進行真空脫氯。冷卻后的氯氣溫度降溫至50-55℃后匯總并入氯氣主管線與氯酸鹽分解,和淡鹽水脫氯過來的氯氣一起被送至氯氣處理工序。
總體而言,在氯氣處理工序氯氣冷卻采用一級洗滌加二級鈦冷間接冷卻相結合[1],硫酸干燥采用四塔串聯干燥工藝,水霧和酸霧除霧器濾芯采用美國布林克除霧器濾芯,氯氣壓縮機采用西門子KKK公司生產的透平離心式氯氣壓縮機。該套氯氣處理裝置無論在電解初開車還是調峰生產變動負荷情況下,總體運行正常平穩,干燥氯氣含水質量分數一直穩定在1*10-5以內,硫酸單耗穩定在12-14kg/t。
詳細的處理過程為來自電解的氯氣通過玻璃鋼管道輸送至氯氣處理一級洗滌塔,塔內氯水由氯水泵加壓經氯水冷卻器冷卻后,從洗滌塔塔頂噴淋頭噴淋而下,與從下至上的高溫氯氣進行逆流接觸,氯氣降溫至30℃進入鈦列管式換熱器,被7-9℃冷凍水間接冷卻至12-16℃。在此過程中的所有氯水通過管道回流至氯氣洗滌塔,通過洗滌塔泵出口的液位調節閥與洗滌塔液位自控聯鎖將氯水打至電解淡鹽水脫氯工序回收利用。
從鈦冷卻器出來的氯氣進入水霧捕集器除去水霧后,電解槽出來的氯氣剩余含水量約降低為原來的1.6%[2],除霧后的氯氣進入一級填料塔填料底部,填料塔循環硫酸通過硫酸磁力泵從塔底輸送至硫酸板式換熱器,通過7~9℃的冷凍水與硫酸換熱后從塔頂硫酸分布器噴淋而下,在填料干燥塔中與氯氣逆流接觸,除去氯氣中的水分。一級干燥塔至四級干燥塔的硫酸濃度依次約為75~78%、85~90%、93~95%、98%,硫酸控制的溫度為14-15℃,氯氣溫度控制在14-15℃。其中在一級干燥塔的硫酸循環泵出口,設置一硫酸取樣口、現場密度計及廢酸控制調節閥,用于控制出酸。選擇上述各塔出酸濃度有一定的原因,一般情況下,濃硫酸溫度不應低于10℃,以防結晶,參見表1硫酸溶液的結晶溫度表。
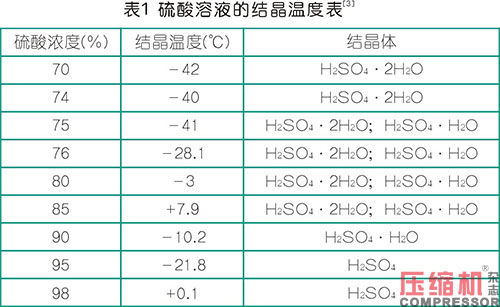
干燥后的氯氣經過酸霧除霧器,除去硫酸霧和其它雜質后,進入氯氣壓縮機壓縮,經過四級壓縮及四級氯氣冷卻器冷卻,最終氯氣被壓縮至0.6-0.7MPaG,溫度約為30-35℃,送至液化工序的原氯分配臺。下圖1為安邦公司氯氣處理工序流程方框簡圖:
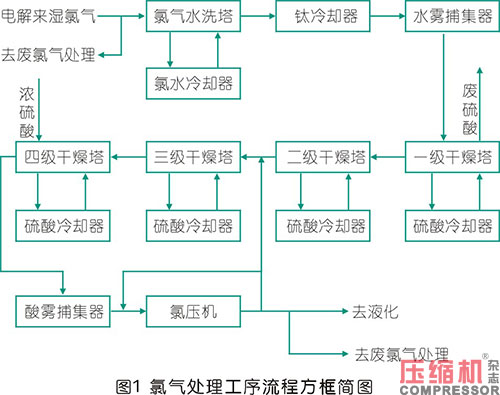
2、氯氣處理裝置運行情況
安邦公司氯氣處理裝置運行13年來,總體運行平穩,干燥氯氣中含水完全達到了設計要求。在線水分分析儀顯示一般保持在1*10-5以下,冬季水分可保持在0.5*10-5以下。由于電解調峰生產,調節較為頻繁,2010年開機以來,硫酸消耗基本維持在12-14kg/t左右水平,近5年來年平均硫酸單耗在12.7、13.6、12.9、13.2、13.2kg/t。
氯氣處理裝置運行中各項工藝指標保持穩定,2022年5月16日各項工藝指標執行情況如下:
氯氣洗滌塔氯氣進口溫度55.2℃
氯氣洗滌塔氯氣進口壓力-0.45KPa
氯氣洗滌塔氯氣出口溫度30.1℃
鈦冷卻器氯氣出口溫度13.45℃
一級干燥塔氯氣出口溫度14.2℃
一級干燥塔稀硫酸質量分數77.5%
二級干燥塔氯氣出氣溫度14.3℃
二級干燥塔稀硫酸質量分數92%
三級干燥塔氯氣出氣溫度14.1℃
三級干燥塔稀硫酸質量分數96%
四級干燥塔氯氣出氣溫度14.2℃
四級干燥塔稀硫酸質量分數98%
氯氣壓縮機進口氯氣壓力-12.8KPa
氯氣壓縮機出口氯氣溫度32℃
氯氣壓縮機出口氯氣壓力0.602MPa
氯氣在線水分分析儀(I、IV級)0.56*10-5、0.62*10-5
3、氯氣處理裝置可能產生的問題及技術改進
3.1干燥塔填料故障,出塔水分增加,影響氯氣中冷器壽命,可能造成腐蝕泄漏
氯氣填料干燥塔內填料是有壽命的,正常情況下經過近4年的運行,原PVC填料逐步老化,會發生脆化變形現象。導致比表面積嚴重降低,氯氣含水逐步上升,從原來穩定的5ppm左右,在約1個月時間內就可能上升至60ppm,且仍有繼續上升趨勢;干燥塔塔阻升高約2KPa,開始影響到氯壓機的安全穩定運行。
氯氣填料干燥塔水分開始逐步升高時,安邦公司在排除水分檢測儀誤差及故障、水霧捕集器故障原因后,初步懷疑PVC填料出現問題。
安邦公司氯氣處理1級到4級干燥塔用的是PVC花環,73*27.5型,填料堆積密度是硫酸密度的4.3%,填料質量相對于硫酸質量可不計。
從當時硫酸用量、硫酸控制溫度、氯氣水份來判斷,若水分檢測儀結果為真,則出現該情況的原因最大的可能性為塔內填料發生軟化降低,而且高度降低較多。硫酸用量增加及降低溫度已起不到決定性作用。在氯氣產量增加的情況下,氯氣流速流量增加,硫酸用量雖然增加,但是接觸面積不夠導致水分無法及時吸附。
經過論證,安邦公司決定徹底更換四臺塔內的PVC花環填料。對PVC花環和CPVC花環進行了溫度耐受實驗,PVC花環填料的耐受溫度在65℃,60℃時強度開始降低;而CPVC耐受溫度在85℃,80℃時強度未見明顯降低,且據資料顯示CPVC對腐蝕性介質比如氯氣和濃硫酸的耐受性上有較為明顯的優勢,PVC花環在長期使用過程中會發生癱軟脆化甚至發生斷裂,而CPVC花環填料相對PVC花環而言,CPVC盡管同樣會發生強度的降低但不易發生變脆垮塌的風險。因此在確認CPVC花環填料的運行穩定性后,決定對每只塔更換填料體積為31.8396m3,比表面積127m2/m3,接觸面積為4044m2。
安邦公司電解工序采用峰谷電調峰生產的方式,在電解A-D槽電流5kA,E-J槽電流6kA時,為低負荷;電解A-D槽電流11kA,E-J槽電流12.5kA時,為高負荷。PT0509為一級水洗塔前壓力,PT0550為四級干燥塔出口壓力,PT2450為酸霧捕集器出口壓力,PT2451為氯壓機進口壓力,氯氣處理阻力指水洗塔至酸霧捕集器出口之間的阻力,總阻力指水洗塔至氯壓機進口包含氯壓機進口過濾器的阻力。
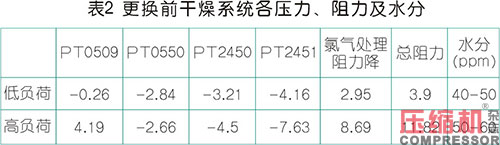
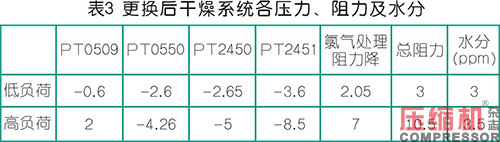
更換填料后,在同樣高負荷情況下,電解氯氣輸送壓力PT218壓力從7.5kPa降至3.9kPa,降低3.6kPa;氯氣處理總阻力降低1.3kPa,電解至氯壓機進口管道總阻力降低4.9kPa。水分從60~90ppm降低至13ppm并仍然有下降趨勢。
更換填料后電解系統至氯壓機進口間的阻力降低效果明顯,降低的4.9kPa壓力可以提升電解槽A-D的電流約4kA,每小時多產3.3噸折百堿,每年多產2.67萬噸折百堿。同時干燥系統的水分降低明顯,保證了氯氣壓縮機的安全穩定運行,同時有效防止了氯氣中間冷卻器因為水分含量高導致的腐蝕穿孔泄漏。
3.2氯氣處理工藝指標控制值偏差導致水分升高,影響設備壽命
3.2.1.氯氣處理的目的
從電解槽陽極析出的聯產氯氣溫度很高,通常稱之為“高溫濕氯氣”。濕氯氣的化學性質要比干燥氯氣更為強烈,幾乎對鋼鐵以及絕大多數的金屬有較強的腐蝕作用。只有少量的貴、稀金屬或非金屬材料在一定條件下,才能抵御此類氯氣的腐蝕作用。因此給氯氣的輸送、使用、貯存等都帶來了極大的麻煩和困難。而干燥后的氯氣對鋼鐵等常用的金屬材料的腐蝕作用在通常的條件之下是比較小的。詳見氯中不同含水對鋼鐵的年腐蝕速率,見表4。
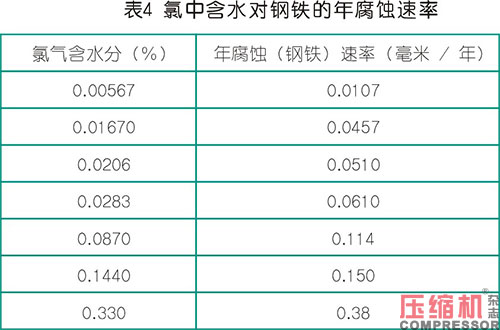
由上述腐蝕速率表可知,隨著氯氣中含水分的增加,每年的腐蝕速率也在增加。因此濕氯氣的脫水和干燥是生產和使用氯氣過程的需要。可見氯氣處理的目的就是要除去濕氯氣中的水分,使之成為含水分量甚微的干燥氯氣以適應、滿足氯氣輸送、生產、使用的需要。
3.2.2.氯氣處理氯中含水與氯氣溫度控制的關系
從氯氣處理的過程中,我們知道完整的氯氣處理工藝應包括:“冷卻除沫、干燥脫水、除霧凈化、壓縮輸送和事故氯氣處理”這五個部分。用通俗的話來講就是:“先冷卻、后干燥”工藝過程。
我們知道氣體的“含濕量”與溫度有著密切的關系。在不同的壓力和溫度下,氣體中的“含濕量”(又稱為“水蒸汽分壓”)是不同的。飽和濕氯氣中“含濕量”同樣與溫度有著密切的關系。一般來說,在壓力相同的情況下,溫度較高的氣體中含水量要大于溫度較低的氣體。詳見“氯氣中含濕量與溫度關系表5”:
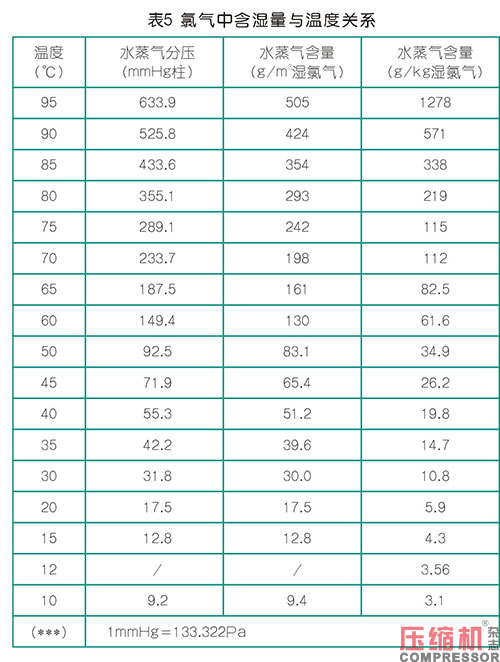
由表5可知,在相同的壓力情況下,氣體溫度每下降10℃,濕氯氣中的“含濕量”幾乎降低近一半。若以電解槽陽極出口氯氣溫度為80℃的話,每千克濕氯氣中所含的水分為219克。如果使用溫度為30℃的工業上水將其冷卻,使其溫度降低至40℃;此時每千克濕氯氣含水分為19.8克,可以通過冷卻去除掉水分近200克,幾乎去除掉91.3%的含水分。如果再用5~10℃的冷凍氯化鈣鹽水進一步冷卻,讓其溫度降至12℃;則每千克濕氯氣可去除水分16.24克。由此可見,濕氯氣溫度從80℃下降至12℃,每千克濕氯氣可以去除掉水分215.44克,占98.4%。余下的1.6%水分進行干燥脫水,這樣做是比較合理的。
按照降低氣相的溫度能夠減少“含濕量”的觀點,即氣相的溫度越低,氣體中水蒸氣分壓也越低,所含水分也就越少。那么繼續降低氣相的溫度,以求得較低的氣體“含濕量”,這樣的做法卻是不可行、不可取的。原因是當氯氣的溫度降低到9.6℃時,將會形成Cl2·8H2O的結晶體,使冷凝下來的氯水結冰,將冷卻器及其管道堵塞,使氣體無法通過。因此濕氯氣的溫度不可無限制降低,應有適度,最佳的進干燥塔溫度是12~16℃。
以上是通過冷卻手段,使氯氣中的含水分量減少了98.4%,這也就是實施“先冷卻、后干燥”理論的效果。如果不采取冷卻而直接用硫酸進行脫水干燥會是什么樣子呢?我們用濃度為98%的硫酸干燥稀釋至75%硫酸計的話,進行干燥脫水過程中,1噸硫酸吸收濕氯氣中所含水分0.306噸。這樣每干燥1噸濕氯氣所消耗的98%硫酸為0.7噸。以年產20萬噸100%燒堿生產能力計的話,每天處理600噸濕氯氣需要消耗硫酸420噸。這樣的消耗實在驚人。更令人吃驚的是:這些硫酸吸收了氯氣中的水分所釋放出來的稀釋熱量簡直無法估量。以每千克濃硫酸吸收水分放出的溶解熱為3557.675千焦(850千卡)計算,每天釋放出的熱量為1.49×109千焦。這些熱量可將4462.5噸20℃水上升至100℃,這明顯是不合理的。
3.2.3.氯氣處理硫酸濃度控制對氯中含水的影響
在氯氣洗滌降溫除霧后,氯中含水的進一步降低需要通過濃硫酸干燥及除霧的方式進行脫除。
氯氣在硫酸中的溶解度很小,可以說幾乎不溶解于硫酸;而水分卻能夠以任意比例溶解于硫酸之中,從而組成不同濃度比例的硫酸溶液。因此在氯氣處理工藝過程中“干燥脫水”這一步驟就借助于硫酸作溶劑;但是濃硫酸與濕氯氣中的水分進行吸收傳質的所謂“干燥脫水”,并不是在任何條件下都能實現的;而是需要一定的吸收傳質條件,比如:溫度、溶劑濃度等等。
要使吸收傳質操作得以進行,需要解決三個問題:
a.選擇合適的溶劑,要使其有選擇性的溶解氣相混合物中被分離的組分。在氯氣處理工藝過程中,選擇硫酸作為溶劑,它能夠溶解氯氣中被分離的組分水分,而對氯氣卻幾乎不能溶解。
b.選擇合適的吸收傳質設備,以實現氣液二相(溶質與溶劑)之間的接觸,使被分離的組分能夠從氣相中轉移到硫酸溶液中去。在氯氣處理工藝過程中,選擇了填料塔(泡沫塔、泡罩塔)等設備等,使氣相中的溶質(水分)與液相的硫酸充分接觸,使氯氣中的水分能夠轉移到硫酸中去。
c.選擇的溶劑能夠循環使用。在氯氣處理工藝過程中,溶劑硫酸能夠在一定的濃度范圍之內循環使用(98%~75%),并不斷補充新溶劑,以確保溶劑有足夠的循環量,使濃度不斷地更新。
濕氯氣中的所含水分處理量決定于硫酸液面上方的水蒸汽分壓。而不同的濃度和溫度的硫酸溶液的液面上方的水蒸汽分壓力是不同的。把硫酸液面上的水蒸氣分壓力降低,就能提高硫酸吸收氣相中所含水分進行傳質的速率,也就能將“氣相”濕氯氣中所含水分量降到最低點。
那么,要降低硫酸液面上的水蒸氣分壓有兩種途徑:
a).在溫度一定的狀況下,溶劑硫酸的濃度越高,其液面上的水蒸氣分壓就越低(這是從參數濃度方面來考慮)。
b).在濃度一定的狀況下,溶劑硫酸的溫度降低,那么它的液面上水蒸汽分壓隨之下降,從而加大了傳質吸收的過程的推動力。理解溫度對硫酸吸水的影響請看示意圖2。
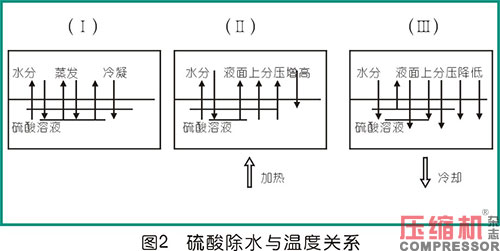
如圖所示(Ⅰ)表示:硫酸溶液在一個封閉的容器中,溶液中的水分不斷地從溶液中蒸發出來進入硫酸液面;幾乎同時又有液面上的冷凝水蒸汽不斷地進入硫酸溶液;因而,硫酸溶液的液面上水蒸氣分壓幾乎不變,達到平衡狀態。
如圖所示(Ⅱ)表示:硫酸溶液在一個封閉的容器中,并且處于溫度上升的加熱狀態,硫酸溶液中的水分大量的被蒸發出來進入硫酸溶液的液面;而液面上冷凝水蒸汽進入硫酸溶液幾乎很少;因而造成硫酸液面上的水蒸汽分壓增高,液面上的水蒸汽是很難進入硫酸溶液的。
如圖所示(Ⅲ)表示:硫酸溶液在一個封閉的容器之中,并且處于溫度下降的冷卻狀態,硫酸溶液中的水分由于溫度降低而蒸發至液面上的很少,相反液面上的水蒸汽由于溫度降低而大量的冷凝下來,進入溶液;因而造成硫酸液面上的水蒸氣分壓力降低,液面上的水蒸氣是很容易進入硫酸溶液的。
當然,對于氣相中含有雙組分(氯氣與水蒸汽)的混合物來說,其氣相擴散組分(水蒸汽)擴散進入硫酸的過程,“費克定律”(Fickler principle)同樣是適用的。即在單位時間之內,氣相氯氣中的擴散組分(水蒸汽)擴散通過單位面積的物質量是與擴散組分在擴散方向Z向上的濃度梯度成正比,因此降低硫酸濃度,可以降低硫酸表面水蒸氣分壓,更加有利于硫酸降低表面水蒸氣分壓從而在噴淋過程中增加傳質推動力,促進氯氣中的水分向冷硫酸中轉移,達到脫除氯中含水的目的,保證氯氣中間冷卻器的安全,防止其產生泄漏。
在此說明一點,氯中含水水分一般控制在50ppm以內,控制的越低對設備而言越好。氯氣壓縮機在運行時,會設置水分高報及停車指標,德國KKK壓縮機高報為240ppm,停車指標為480ppm。過高的水分不但對氯氣中間冷卻器造成腐蝕泄漏,同時也對氯氣壓縮機的轉子及管腔產生腐蝕。由于轉子轉速達到10000轉/min,水分的失控危害極其嚴重,可在短期內造成轉子的報廢,導致轉子壓縮能力急劇下降,甚至造成轉子不平衡導致導致事故的發生。曾有某廠家因氯中含水不達標導致氯氣壓縮機一周內轉子報廢的事故發生。
3.3氯氣壓縮機中間冷卻器列管結垢造成堵塞導致局部產生腐蝕穿孔
原廠家提供的氯氣中間冷卻器圖紙,采用八管程列管換熱器,管道為Φ19*2碳鋼管道。經過一年多的使用,發現該換熱器存在冷卻水折流管線過長,阻力大,導致水流速過緩,管道內部易杜塞、換熱效果差,出口氯氣溫度逐步由原來的30℃升高至51℃。
針對原氯氣中間冷卻器,冷卻水折流管線過長,阻力大,導致水流速過緩,管道內部易杜塞、換熱效果差的問題,安邦公司進行了專門的分析和研究,制定了改進方案。
將氯氣冷卻器重新設計,將原八管程改為六管程,內部列管改為Φ25*3管道,排列方式為正三角排列,換熱器循環水進出口管道由原來DN125改為DN150,因高位槽位置未變,進水壓力保持不變,出口依然保持無壓回水方式。
管道內水流方式為喘流,根據壓差阻力與管徑的關系,壓差阻力反比于管徑之比的5次方。改造后氯氣中間冷卻器的管程阻力降為改造前阻力的0.3倍,管內水流速增加,總傳熱系數大大增加。氯氣溫度由原來換熱后51℃降低至25-30℃。改造后換熱效果非常明顯。
3.4氯氣中間冷卻器水側暴露導致的電化腐蝕穿孔
氯氣冷卻器作為備件保存時應注意充氮氣保存,將所有氣相管口盲死確保密封,氣相口用盲板盲死,在盲板上安裝閥門及氮氣進口。有必要時加裝壓力表,觀察氯氣冷卻器氣相壓力泄漏情況。如果充入氮氣后氣相壓力隨著時間發生持續降低,應進行氣密性試驗。
氯氣冷卻器投入使用后,應注意氣相壓力高于冷卻水壓力,以防氯氣冷卻器水管泄漏時水進入氣相,導致氯氣壓縮機腐蝕造成更大事故。
氯氣壓縮機崗位巡檢人員在巡檢時,每班次需打開水側封頭排氣口將水中夾帶的空氣排盡,在每次開車加水時需打開排盡氯氣冷卻器內水中夾帶的空氣,而排水時同樣需要打開排氣口,以能夠迅速從排污口排去氯氣冷卻器內水,防止氯氣冷卻器內水因排水導致空腔形成負壓被吸住無法排盡。
在停車大修時,需要對氯氣冷卻器重點保護,除了氯氣壓縮機需要通入高氮進行充氣置換保護外,氯氣冷卻器水相也是重中之重。因水走的是管程,從氯氣冷卻器封頭的底部進入,從上部無壓溢出,碳鋼設備充水容易在空氣與水的接觸面上發生銹蝕,要防止這個問題,有兩種方法可以考慮。第一種是氯氣冷卻器管程保持充水滿液狀態后關閉進水閥門,為了保證氣相壓力大于水壓力,需要調整氯氣壓縮機進口的氮氣閥門,保證氯氣冷卻器內氣相壓力超過水壓力5kPa以上,以防止氯氣冷卻器泄漏水進入殼程。第二種方法是將氯氣冷卻器管程內水徹底排盡,排盡后從氯氣冷卻器E口充入氮氣,從F口將水吹出,直至排水口無水噴出為止。
在做開車準備時,氯氣冷卻器充水前必須保證氣相壓力在15kPa以上,以時刻保證氣相壓力大于水壓力。氯氣冷卻器充滿水后,提高氯氣壓縮機內氮氣壓力在25-40kPa之間,各項準備工作完畢后,開始啟動氯氣壓縮機。啟動后,迅速調節進入氯氣壓縮機的氮氣閥門,保證氮氣供應,防止氯氣壓縮機啟動后導致一級氯氣壓縮機內氣相壓力為負值。氯氣冷卻器曾發生過兩次因列管缺陷發生的泄漏,其中一次在氯氣壓縮機啟動后壓力逐步上升的過程中,發生列管突然破裂,DCS氯氣壓縮機冷卻水PH值發生迅速下降,現場氯氣報警儀出現氯氣報警,迅速被發現后,系統停車處理,檢測出具體的泄漏氯氣冷卻器,打開所有封頭用水管對所有列管進行水置換,直至水清澈無異味,同理對封頭及焊接面也必須徹底沖洗干凈,防止氯水腐蝕。在整個過程中氯氣壓縮機內始終充入大約200kPa的壓力,用肥皂水進行試驗,檢查泄漏的列管,如果列管泄漏,干燥的氮氣會將列管吹干,而不漏的列管保持潮濕狀態,此時用肥皂水試驗能夠較快地發現泄漏的列管。整個過程如果處理迅速,可及時防止氯氣冷卻器的腐蝕,否則極易導致氯氣冷卻器被普遍腐蝕穿孔而報廢,造成因處理不及時而產生更大的損失。需要注意的是檢查出泄漏的列管后,堵焊后需要進行壓力測試,進行打壓試驗至使用壓力以上0.1MPa,穩壓40分鐘以上,24小時壓力減小低于0.01MPa方可投入使用,以防砂眼無法查出導致進一步泄漏,并做好試壓記錄。
3.5氯氣中冷器冷卻循環水富氧化導致的泄漏
我公司氯氣壓縮機中間冷卻器及油冷卻器循環水,采用獨立的循環水冷卻系統提供的循環水,與氯堿系統大循環水站獨立。
主要原因為大循環水站水質由于濃縮倍數的關系,通常濃縮倍數≤3進行換水,經過在線檢測PH大約在8-9,含鹽量大約在0.8-1.0g/l,沒有加藥處理。氯堿系統換熱設備的材質品種繁多,換熱器數量較多,出現泄漏進入各種雜質離子的可能性增加,對氯氣中冷器產生影響,造成腐蝕泄漏的可能性提高;大循環水站供水壓力大約在0.5MPa,而氯氣壓縮機中間冷卻器的氯氣壓力從一級到四級依次大約為0.05MPa、0.15MPa、0.35MPa、0.65MPa,大循環水站供水壓力由循環水泵供應,采用變頻與出口溫度調節,水壓會發生變化,氯氣中間冷卻器采用手動閥門控制且要求氣壓必須大于水壓,這給調節帶來不穩定性。
為了確保水質的穩定性和供水壓力的穩定性,我公司從第一套隔膜堿氯氣壓縮機開始就設計采用獨立的涼水塔系統,設計涼水塔冷水高位槽且設置回流至低位槽,水從12米高度的冷水高位槽內自然流到氯氣中間冷卻器及油冷卻器內,水壓穩定在0.12MPa。
原始采用河水作為補加水的方式,發現結垢較為嚴重,后改為純水作為補加水,結垢問題得到徹底解決,但經過了解考證,單純的純水是不適宜獨立作為補加水的。原因為碳鋼中含有一定的碳,在純水中,水與鐵、碳形成原電池,純水中的溶解氧、二氧化碳具有促進金屬腐蝕的作用,即使在氧、二氧化碳濃度很低的情況下,也能引起嚴重的腐蝕。純水對碳鋼的腐蝕面積小、深;工業水對碳鋼腐蝕的面積大、淺,容易使設備整體產生層狀腐蝕[4]。由于點蝕的過程具有自催化的特征,從而促進腐蝕快速發展,這種腐蝕產生的穿孔特征為尖銳狀針孔。在不完全密閉、不加處理劑的情況下,純水對碳鋼設備的腐蝕更不利于化工生產。要減少腐蝕,必須合理選擇使用環境(如溴化鋰冷水系統,完全密閉,不存在富氧化環境,純水對碳鋼設備腐蝕就可以忽略不計)。
如上所述,因敞開式涼水塔單純加純水對碳鋼的腐蝕作用,我們采用的純水為主,添加部分工業水,控制PH在7-8以上,電導率控制在<100us/cm,ORP控制在<300mv。經過實驗,避免了工業水容易堵塞的問題,也解決了單純純水容易產生針孔腐蝕穿孔的問題。
4、結論
綜上所述,氯氣中間冷卻器的使用安全,本質上也是保護主設備氯氣壓縮機的使用安全。氯氣壓縮機所涉及的輔助系統,如氯氣處理干燥系統的工藝參數的運行質量、循環水站水質的控制及在線監測、設備材質選擇及正確安裝等都關系到氯氣中間冷卻器能否長周期安全穩定運行。
上述僅代表筆者本人的一點薄見,不妥之處,敬請同行業者批評指正。
參考文獻
[1]王榮欣,肖娜.氯氣干燥裝置運行總結[J].氯堿工業,2014(10):25-26
[2]劉紅民,周賢國,柴曄.降低氯中含水量的措施[J].中國氯堿,2008(7):6-7
[3]楊國穩.氯氣處理工藝及關鍵點控制綜述[J].中國氯堿,2016(10):11-14
[4]王建超,薛志清.工業水與純水腐蝕碳鋼的實驗[J].氯堿工業,2015(3):44-45.
【壓縮機網】氯氣壓縮機中間冷卻器泄漏的原因有很多,涉及設備材質選擇、設備加工、設備安裝、工藝指標控制,特別是氯氣含水量的控制及酸霧的控制、氯氣中間冷卻器的冷卻介質即循環水的制備工藝等。本文將從氯氣壓縮機氯氣處理開始介紹,在整個氯氣處理直至氯氣壓縮后輸送過程中,各個過程安裝及控制對氯氣中冷器壽命可能造成影響的因素。氯氣的洗滌、冷卻、干燥、除霧、壓縮過程統稱為氯氣處理,也會對氯氣中冷器壽命造成影響。
1、氯氣處理工藝流程簡介
由離子膜電解槽出來的溫度約為85-90℃的高溫氯氣,在電解工序通過鈦列管式換熱器與二次鹽水工序的精制鹽水進行換熱,冷凝下來的氯水流至離子膜電解氯水罐,用氯水泵打入脫氯淡鹽水塔進行真空脫氯。冷卻后的氯氣溫度降溫至50-55℃后匯總并入氯氣主管線與氯酸鹽分解,和淡鹽水脫氯過來的氯氣一起被送至氯氣處理工序。
總體而言,在氯氣處理工序氯氣冷卻采用一級洗滌加二級鈦冷間接冷卻相結合[1],硫酸干燥采用四塔串聯干燥工藝,水霧和酸霧除霧器濾芯采用美國布林克除霧器濾芯,氯氣壓縮機采用西門子KKK公司生產的透平離心式氯氣壓縮機。該套氯氣處理裝置無論在電解初開車還是調峰生產變動負荷情況下,總體運行正常平穩,干燥氯氣含水質量分數一直穩定在1*10-5以內,硫酸單耗穩定在12-14kg/t。
詳細的處理過程為來自電解的氯氣通過玻璃鋼管道輸送至氯氣處理一級洗滌塔,塔內氯水由氯水泵加壓經氯水冷卻器冷卻后,從洗滌塔塔頂噴淋頭噴淋而下,與從下至上的高溫氯氣進行逆流接觸,氯氣降溫至30℃進入鈦列管式換熱器,被7-9℃冷凍水間接冷卻至12-16℃。在此過程中的所有氯水通過管道回流至氯氣洗滌塔,通過洗滌塔泵出口的液位調節閥與洗滌塔液位自控聯鎖將氯水打至電解淡鹽水脫氯工序回收利用。
從鈦冷卻器出來的氯氣進入水霧捕集器除去水霧后,電解槽出來的氯氣剩余含水量約降低為原來的1.6%[2],除霧后的氯氣進入一級填料塔填料底部,填料塔循環硫酸通過硫酸磁力泵從塔底輸送至硫酸板式換熱器,通過7~9℃的冷凍水與硫酸換熱后從塔頂硫酸分布器噴淋而下,在填料干燥塔中與氯氣逆流接觸,除去氯氣中的水分。一級干燥塔至四級干燥塔的硫酸濃度依次約為75~78%、85~90%、93~95%、98%,硫酸控制的溫度為14-15℃,氯氣溫度控制在14-15℃。其中在一級干燥塔的硫酸循環泵出口,設置一硫酸取樣口、現場密度計及廢酸控制調節閥,用于控制出酸。選擇上述各塔出酸濃度有一定的原因,一般情況下,濃硫酸溫度不應低于10℃,以防結晶,參見表1硫酸溶液的結晶溫度表。
干燥后的氯氣經過酸霧除霧器,除去硫酸霧和其它雜質后,進入氯氣壓縮機壓縮,經過四級壓縮及四級氯氣冷卻器冷卻,最終氯氣被壓縮至0.6-0.7MPaG,溫度約為30-35℃,送至液化工序的原氯分配臺。下圖1為安邦公司氯氣處理工序流程方框簡圖:
2、氯氣處理裝置運行情況
安邦公司氯氣處理裝置運行13年來,總體運行平穩,干燥氯氣中含水完全達到了設計要求。在線水分分析儀顯示一般保持在1*10-5以下,冬季水分可保持在0.5*10-5以下。由于電解調峰生產,調節較為頻繁,2010年開機以來,硫酸消耗基本維持在12-14kg/t左右水平,近5年來年平均硫酸單耗在12.7、13.6、12.9、13.2、13.2kg/t。
氯氣處理裝置運行中各項工藝指標保持穩定,2022年5月16日各項工藝指標執行情況如下:
氯氣洗滌塔氯氣進口溫度55.2℃
氯氣洗滌塔氯氣進口壓力-0.45KPa
氯氣洗滌塔氯氣出口溫度30.1℃
鈦冷卻器氯氣出口溫度13.45℃
一級干燥塔氯氣出口溫度14.2℃
一級干燥塔稀硫酸質量分數77.5%
二級干燥塔氯氣出氣溫度14.3℃
二級干燥塔稀硫酸質量分數92%
三級干燥塔氯氣出氣溫度14.1℃
三級干燥塔稀硫酸質量分數96%
四級干燥塔氯氣出氣溫度14.2℃
四級干燥塔稀硫酸質量分數98%
氯氣壓縮機進口氯氣壓力-12.8KPa
氯氣壓縮機出口氯氣溫度32℃
氯氣壓縮機出口氯氣壓力0.602MPa
氯氣在線水分分析儀(I、IV級)0.56*10-5、0.62*10-5
3、氯氣處理裝置可能產生的問題及技術改進
3.1干燥塔填料故障,出塔水分增加,影響氯氣中冷器壽命,可能造成腐蝕泄漏
氯氣填料干燥塔內填料是有壽命的,正常情況下經過近4年的運行,原PVC填料逐步老化,會發生脆化變形現象。導致比表面積嚴重降低,氯氣含水逐步上升,從原來穩定的5ppm左右,在約1個月時間內就可能上升至60ppm,且仍有繼續上升趨勢;干燥塔塔阻升高約2KPa,開始影響到氯壓機的安全穩定運行。
氯氣填料干燥塔水分開始逐步升高時,安邦公司在排除水分檢測儀誤差及故障、水霧捕集器故障原因后,初步懷疑PVC填料出現問題。
安邦公司氯氣處理1級到4級干燥塔用的是PVC花環,73*27.5型,填料堆積密度是硫酸密度的4.3%,填料質量相對于硫酸質量可不計。
從當時硫酸用量、硫酸控制溫度、氯氣水份來判斷,若水分檢測儀結果為真,則出現該情況的原因最大的可能性為塔內填料發生軟化降低,而且高度降低較多。硫酸用量增加及降低溫度已起不到決定性作用。在氯氣產量增加的情況下,氯氣流速流量增加,硫酸用量雖然增加,但是接觸面積不夠導致水分無法及時吸附。
經過論證,安邦公司決定徹底更換四臺塔內的PVC花環填料。對PVC花環和CPVC花環進行了溫度耐受實驗,PVC花環填料的耐受溫度在65℃,60℃時強度開始降低;而CPVC耐受溫度在85℃,80℃時強度未見明顯降低,且據資料顯示CPVC對腐蝕性介質比如氯氣和濃硫酸的耐受性上有較為明顯的優勢,PVC花環在長期使用過程中會發生癱軟脆化甚至發生斷裂,而CPVC花環填料相對PVC花環而言,CPVC盡管同樣會發生強度的降低但不易發生變脆垮塌的風險。因此在確認CPVC花環填料的運行穩定性后,決定對每只塔更換填料體積為31.8396m3,比表面積127m2/m3,接觸面積為4044m2。
安邦公司電解工序采用峰谷電調峰生產的方式,在電解A-D槽電流5kA,E-J槽電流6kA時,為低負荷;電解A-D槽電流11kA,E-J槽電流12.5kA時,為高負荷。PT0509為一級水洗塔前壓力,PT0550為四級干燥塔出口壓力,PT2450為酸霧捕集器出口壓力,PT2451為氯壓機進口壓力,氯氣處理阻力指水洗塔至酸霧捕集器出口之間的阻力,總阻力指水洗塔至氯壓機進口包含氯壓機進口過濾器的阻力。
更換填料后,在同樣高負荷情況下,電解氯氣輸送壓力PT218壓力從7.5kPa降至3.9kPa,降低3.6kPa;氯氣處理總阻力降低1.3kPa,電解至氯壓機進口管道總阻力降低4.9kPa。水分從60~90ppm降低至13ppm并仍然有下降趨勢。
更換填料后電解系統至氯壓機進口間的阻力降低效果明顯,降低的4.9kPa壓力可以提升電解槽A-D的電流約4kA,每小時多產3.3噸折百堿,每年多產2.67萬噸折百堿。同時干燥系統的水分降低明顯,保證了氯氣壓縮機的安全穩定運行,同時有效防止了氯氣中間冷卻器因為水分含量高導致的腐蝕穿孔泄漏。
3.2氯氣處理工藝指標控制值偏差導致水分升高,影響設備壽命
3.2.1.氯氣處理的目的
從電解槽陽極析出的聯產氯氣溫度很高,通常稱之為“高溫濕氯氣”。濕氯氣的化學性質要比干燥氯氣更為強烈,幾乎對鋼鐵以及絕大多數的金屬有較強的腐蝕作用。只有少量的貴、稀金屬或非金屬材料在一定條件下,才能抵御此類氯氣的腐蝕作用。因此給氯氣的輸送、使用、貯存等都帶來了極大的麻煩和困難。而干燥后的氯氣對鋼鐵等常用的金屬材料的腐蝕作用在通常的條件之下是比較小的。詳見氯中不同含水對鋼鐵的年腐蝕速率,見表4。
由上述腐蝕速率表可知,隨著氯氣中含水分的增加,每年的腐蝕速率也在增加。因此濕氯氣的脫水和干燥是生產和使用氯氣過程的需要。可見氯氣處理的目的就是要除去濕氯氣中的水分,使之成為含水分量甚微的干燥氯氣以適應、滿足氯氣輸送、生產、使用的需要。
3.2.2.氯氣處理氯中含水與氯氣溫度控制的關系
從氯氣處理的過程中,我們知道完整的氯氣處理工藝應包括:“冷卻除沫、干燥脫水、除霧凈化、壓縮輸送和事故氯氣處理”這五個部分。用通俗的話來講就是:“先冷卻、后干燥”工藝過程。
我們知道氣體的“含濕量”與溫度有著密切的關系。在不同的壓力和溫度下,氣體中的“含濕量”(又稱為“水蒸汽分壓”)是不同的。飽和濕氯氣中“含濕量”同樣與溫度有著密切的關系。一般來說,在壓力相同的情況下,溫度較高的氣體中含水量要大于溫度較低的氣體。詳見“氯氣中含濕量與溫度關系表5”:
由表5可知,在相同的壓力情況下,氣體溫度每下降10℃,濕氯氣中的“含濕量”幾乎降低近一半。若以電解槽陽極出口氯氣溫度為80℃的話,每千克濕氯氣中所含的水分為219克。如果使用溫度為30℃的工業上水將其冷卻,使其溫度降低至40℃;此時每千克濕氯氣含水分為19.8克,可以通過冷卻去除掉水分近200克,幾乎去除掉91.3%的含水分。如果再用5~10℃的冷凍氯化鈣鹽水進一步冷卻,讓其溫度降至12℃;則每千克濕氯氣可去除水分16.24克。由此可見,濕氯氣溫度從80℃下降至12℃,每千克濕氯氣可以去除掉水分215.44克,占98.4%。余下的1.6%水分進行干燥脫水,這樣做是比較合理的。
按照降低氣相的溫度能夠減少“含濕量”的觀點,即氣相的溫度越低,氣體中水蒸氣分壓也越低,所含水分也就越少。那么繼續降低氣相的溫度,以求得較低的氣體“含濕量”,這樣的做法卻是不可行、不可取的。原因是當氯氣的溫度降低到9.6℃時,將會形成Cl2·8H2O的結晶體,使冷凝下來的氯水結冰,將冷卻器及其管道堵塞,使氣體無法通過。因此濕氯氣的溫度不可無限制降低,應有適度,最佳的進干燥塔溫度是12~16℃。
以上是通過冷卻手段,使氯氣中的含水分量減少了98.4%,這也就是實施“先冷卻、后干燥”理論的效果。如果不采取冷卻而直接用硫酸進行脫水干燥會是什么樣子呢?我們用濃度為98%的硫酸干燥稀釋至75%硫酸計的話,進行干燥脫水過程中,1噸硫酸吸收濕氯氣中所含水分0.306噸。這樣每干燥1噸濕氯氣所消耗的98%硫酸為0.7噸。以年產20萬噸100%燒堿生產能力計的話,每天處理600噸濕氯氣需要消耗硫酸420噸。這樣的消耗實在驚人。更令人吃驚的是:這些硫酸吸收了氯氣中的水分所釋放出來的稀釋熱量簡直無法估量。以每千克濃硫酸吸收水分放出的溶解熱為3557.675千焦(850千卡)計算,每天釋放出的熱量為1.49×109千焦。這些熱量可將4462.5噸20℃水上升至100℃,這明顯是不合理的。
3.2.3.氯氣處理硫酸濃度控制對氯中含水的影響
在氯氣洗滌降溫除霧后,氯中含水的進一步降低需要通過濃硫酸干燥及除霧的方式進行脫除。
氯氣在硫酸中的溶解度很小,可以說幾乎不溶解于硫酸;而水分卻能夠以任意比例溶解于硫酸之中,從而組成不同濃度比例的硫酸溶液。因此在氯氣處理工藝過程中“干燥脫水”這一步驟就借助于硫酸作溶劑;但是濃硫酸與濕氯氣中的水分進行吸收傳質的所謂“干燥脫水”,并不是在任何條件下都能實現的;而是需要一定的吸收傳質條件,比如:溫度、溶劑濃度等等。
要使吸收傳質操作得以進行,需要解決三個問題:
a.選擇合適的溶劑,要使其有選擇性的溶解氣相混合物中被分離的組分。在氯氣處理工藝過程中,選擇硫酸作為溶劑,它能夠溶解氯氣中被分離的組分水分,而對氯氣卻幾乎不能溶解。
b.選擇合適的吸收傳質設備,以實現氣液二相(溶質與溶劑)之間的接觸,使被分離的組分能夠從氣相中轉移到硫酸溶液中去。在氯氣處理工藝過程中,選擇了填料塔(泡沫塔、泡罩塔)等設備等,使氣相中的溶質(水分)與液相的硫酸充分接觸,使氯氣中的水分能夠轉移到硫酸中去。
c.選擇的溶劑能夠循環使用。在氯氣處理工藝過程中,溶劑硫酸能夠在一定的濃度范圍之內循環使用(98%~75%),并不斷補充新溶劑,以確保溶劑有足夠的循環量,使濃度不斷地更新。
濕氯氣中的所含水分處理量決定于硫酸液面上方的水蒸汽分壓。而不同的濃度和溫度的硫酸溶液的液面上方的水蒸汽分壓力是不同的。把硫酸液面上的水蒸氣分壓力降低,就能提高硫酸吸收氣相中所含水分進行傳質的速率,也就能將“氣相”濕氯氣中所含水分量降到最低點。
那么,要降低硫酸液面上的水蒸氣分壓有兩種途徑:
a).在溫度一定的狀況下,溶劑硫酸的濃度越高,其液面上的水蒸氣分壓就越低(這是從參數濃度方面來考慮)。
b).在濃度一定的狀況下,溶劑硫酸的溫度降低,那么它的液面上水蒸汽分壓隨之下降,從而加大了傳質吸收的過程的推動力。理解溫度對硫酸吸水的影響請看示意圖2。
如圖所示(Ⅰ)表示:硫酸溶液在一個封閉的容器中,溶液中的水分不斷地從溶液中蒸發出來進入硫酸液面;幾乎同時又有液面上的冷凝水蒸汽不斷地進入硫酸溶液;因而,硫酸溶液的液面上水蒸氣分壓幾乎不變,達到平衡狀態。
如圖所示(Ⅱ)表示:硫酸溶液在一個封閉的容器中,并且處于溫度上升的加熱狀態,硫酸溶液中的水分大量的被蒸發出來進入硫酸溶液的液面;而液面上冷凝水蒸汽進入硫酸溶液幾乎很少;因而造成硫酸液面上的水蒸汽分壓增高,液面上的水蒸汽是很難進入硫酸溶液的。
如圖所示(Ⅲ)表示:硫酸溶液在一個封閉的容器之中,并且處于溫度下降的冷卻狀態,硫酸溶液中的水分由于溫度降低而蒸發至液面上的很少,相反液面上的水蒸汽由于溫度降低而大量的冷凝下來,進入溶液;因而造成硫酸液面上的水蒸氣分壓力降低,液面上的水蒸氣是很容易進入硫酸溶液的。
當然,對于氣相中含有雙組分(氯氣與水蒸汽)的混合物來說,其氣相擴散組分(水蒸汽)擴散進入硫酸的過程,“費克定律”(Fickler principle)同樣是適用的。即在單位時間之內,氣相氯氣中的擴散組分(水蒸汽)擴散通過單位面積的物質量是與擴散組分在擴散方向Z向上的濃度梯度成正比,因此降低硫酸濃度,可以降低硫酸表面水蒸氣分壓,更加有利于硫酸降低表面水蒸氣分壓從而在噴淋過程中增加傳質推動力,促進氯氣中的水分向冷硫酸中轉移,達到脫除氯中含水的目的,保證氯氣中間冷卻器的安全,防止其產生泄漏。
在此說明一點,氯中含水水分一般控制在50ppm以內,控制的越低對設備而言越好。氯氣壓縮機在運行時,會設置水分高報及停車指標,德國KKK壓縮機高報為240ppm,停車指標為480ppm。過高的水分不但對氯氣中間冷卻器造成腐蝕泄漏,同時也對氯氣壓縮機的轉子及管腔產生腐蝕。由于轉子轉速達到10000轉/min,水分的失控危害極其嚴重,可在短期內造成轉子的報廢,導致轉子壓縮能力急劇下降,甚至造成轉子不平衡導致導致事故的發生。曾有某廠家因氯中含水不達標導致氯氣壓縮機一周內轉子報廢的事故發生。
3.3氯氣壓縮機中間冷卻器列管結垢造成堵塞導致局部產生腐蝕穿孔
原廠家提供的氯氣中間冷卻器圖紙,采用八管程列管換熱器,管道為Φ19*2碳鋼管道。經過一年多的使用,發現該換熱器存在冷卻水折流管線過長,阻力大,導致水流速過緩,管道內部易杜塞、換熱效果差,出口氯氣溫度逐步由原來的30℃升高至51℃。
針對原氯氣中間冷卻器,冷卻水折流管線過長,阻力大,導致水流速過緩,管道內部易杜塞、換熱效果差的問題,安邦公司進行了專門的分析和研究,制定了改進方案。
將氯氣冷卻器重新設計,將原八管程改為六管程,內部列管改為Φ25*3管道,排列方式為正三角排列,換熱器循環水進出口管道由原來DN125改為DN150,因高位槽位置未變,進水壓力保持不變,出口依然保持無壓回水方式。
管道內水流方式為喘流,根據壓差阻力與管徑的關系,壓差阻力反比于管徑之比的5次方。改造后氯氣中間冷卻器的管程阻力降為改造前阻力的0.3倍,管內水流速增加,總傳熱系數大大增加。氯氣溫度由原來換熱后51℃降低至25-30℃。改造后換熱效果非常明顯。
3.4氯氣中間冷卻器水側暴露導致的電化腐蝕穿孔
氯氣冷卻器作為備件保存時應注意充氮氣保存,將所有氣相管口盲死確保密封,氣相口用盲板盲死,在盲板上安裝閥門及氮氣進口。有必要時加裝壓力表,觀察氯氣冷卻器氣相壓力泄漏情況。如果充入氮氣后氣相壓力隨著時間發生持續降低,應進行氣密性試驗。
氯氣冷卻器投入使用后,應注意氣相壓力高于冷卻水壓力,以防氯氣冷卻器水管泄漏時水進入氣相,導致氯氣壓縮機腐蝕造成更大事故。
氯氣壓縮機崗位巡檢人員在巡檢時,每班次需打開水側封頭排氣口將水中夾帶的空氣排盡,在每次開車加水時需打開排盡氯氣冷卻器內水中夾帶的空氣,而排水時同樣需要打開排氣口,以能夠迅速從排污口排去氯氣冷卻器內水,防止氯氣冷卻器內水因排水導致空腔形成負壓被吸住無法排盡。
在停車大修時,需要對氯氣冷卻器重點保護,除了氯氣壓縮機需要通入高氮進行充氣置換保護外,氯氣冷卻器水相也是重中之重。因水走的是管程,從氯氣冷卻器封頭的底部進入,從上部無壓溢出,碳鋼設備充水容易在空氣與水的接觸面上發生銹蝕,要防止這個問題,有兩種方法可以考慮。第一種是氯氣冷卻器管程保持充水滿液狀態后關閉進水閥門,為了保證氣相壓力大于水壓力,需要調整氯氣壓縮機進口的氮氣閥門,保證氯氣冷卻器內氣相壓力超過水壓力5kPa以上,以防止氯氣冷卻器泄漏水進入殼程。第二種方法是將氯氣冷卻器管程內水徹底排盡,排盡后從氯氣冷卻器E口充入氮氣,從F口將水吹出,直至排水口無水噴出為止。
在做開車準備時,氯氣冷卻器充水前必須保證氣相壓力在15kPa以上,以時刻保證氣相壓力大于水壓力。氯氣冷卻器充滿水后,提高氯氣壓縮機內氮氣壓力在25-40kPa之間,各項準備工作完畢后,開始啟動氯氣壓縮機。啟動后,迅速調節進入氯氣壓縮機的氮氣閥門,保證氮氣供應,防止氯氣壓縮機啟動后導致一級氯氣壓縮機內氣相壓力為負值。氯氣冷卻器曾發生過兩次因列管缺陷發生的泄漏,其中一次在氯氣壓縮機啟動后壓力逐步上升的過程中,發生列管突然破裂,DCS氯氣壓縮機冷卻水PH值發生迅速下降,現場氯氣報警儀出現氯氣報警,迅速被發現后,系統停車處理,檢測出具體的泄漏氯氣冷卻器,打開所有封頭用水管對所有列管進行水置換,直至水清澈無異味,同理對封頭及焊接面也必須徹底沖洗干凈,防止氯水腐蝕。在整個過程中氯氣壓縮機內始終充入大約200kPa的壓力,用肥皂水進行試驗,檢查泄漏的列管,如果列管泄漏,干燥的氮氣會將列管吹干,而不漏的列管保持潮濕狀態,此時用肥皂水試驗能夠較快地發現泄漏的列管。整個過程如果處理迅速,可及時防止氯氣冷卻器的腐蝕,否則極易導致氯氣冷卻器被普遍腐蝕穿孔而報廢,造成因處理不及時而產生更大的損失。需要注意的是檢查出泄漏的列管后,堵焊后需要進行壓力測試,進行打壓試驗至使用壓力以上0.1MPa,穩壓40分鐘以上,24小時壓力減小低于0.01MPa方可投入使用,以防砂眼無法查出導致進一步泄漏,并做好試壓記錄。
3.5氯氣中冷器冷卻循環水富氧化導致的泄漏
我公司氯氣壓縮機中間冷卻器及油冷卻器循環水,采用獨立的循環水冷卻系統提供的循環水,與氯堿系統大循環水站獨立。
主要原因為大循環水站水質由于濃縮倍數的關系,通常濃縮倍數≤3進行換水,經過在線檢測PH大約在8-9,含鹽量大約在0.8-1.0g/l,沒有加藥處理。氯堿系統換熱設備的材質品種繁多,換熱器數量較多,出現泄漏進入各種雜質離子的可能性增加,對氯氣中冷器產生影響,造成腐蝕泄漏的可能性提高;大循環水站供水壓力大約在0.5MPa,而氯氣壓縮機中間冷卻器的氯氣壓力從一級到四級依次大約為0.05MPa、0.15MPa、0.35MPa、0.65MPa,大循環水站供水壓力由循環水泵供應,采用變頻與出口溫度調節,水壓會發生變化,氯氣中間冷卻器采用手動閥門控制且要求氣壓必須大于水壓,這給調節帶來不穩定性。
為了確保水質的穩定性和供水壓力的穩定性,我公司從第一套隔膜堿氯氣壓縮機開始就設計采用獨立的涼水塔系統,設計涼水塔冷水高位槽且設置回流至低位槽,水從12米高度的冷水高位槽內自然流到氯氣中間冷卻器及油冷卻器內,水壓穩定在0.12MPa。
原始采用河水作為補加水的方式,發現結垢較為嚴重,后改為純水作為補加水,結垢問題得到徹底解決,但經過了解考證,單純的純水是不適宜獨立作為補加水的。原因為碳鋼中含有一定的碳,在純水中,水與鐵、碳形成原電池,純水中的溶解氧、二氧化碳具有促進金屬腐蝕的作用,即使在氧、二氧化碳濃度很低的情況下,也能引起嚴重的腐蝕。純水對碳鋼的腐蝕面積小、深;工業水對碳鋼腐蝕的面積大、淺,容易使設備整體產生層狀腐蝕[4]。由于點蝕的過程具有自催化的特征,從而促進腐蝕快速發展,這種腐蝕產生的穿孔特征為尖銳狀針孔。在不完全密閉、不加處理劑的情況下,純水對碳鋼設備的腐蝕更不利于化工生產。要減少腐蝕,必須合理選擇使用環境(如溴化鋰冷水系統,完全密閉,不存在富氧化環境,純水對碳鋼設備腐蝕就可以忽略不計)。
如上所述,因敞開式涼水塔單純加純水對碳鋼的腐蝕作用,我們采用的純水為主,添加部分工業水,控制PH在7-8以上,電導率控制在<100us/cm,ORP控制在<300mv。經過實驗,避免了工業水容易堵塞的問題,也解決了單純純水容易產生針孔腐蝕穿孔的問題。
4、結論
綜上所述,氯氣中間冷卻器的使用安全,本質上也是保護主設備氯氣壓縮機的使用安全。氯氣壓縮機所涉及的輔助系統,如氯氣處理干燥系統的工藝參數的運行質量、循環水站水質的控制及在線監測、設備材質選擇及正確安裝等都關系到氯氣中間冷卻器能否長周期安全穩定運行。
上述僅代表筆者本人的一點薄見,不妥之處,敬請同行業者批評指正。
參考文獻
[1]王榮欣,肖娜.氯氣干燥裝置運行總結[J].氯堿工業,2014(10):25-26
[2]劉紅民,周賢國,柴曄.降低氯中含水量的措施[J].中國氯堿,2008(7):6-7
[3]楊國穩.氯氣處理工藝及關鍵點控制綜述[J].中國氯堿,2016(10):11-14
[4]王建超,薛志清.工業水與純水腐蝕碳鋼的實驗[J].氯堿工業,2015(3):44-45.
網友評論
條評論
最新評論