【壓縮機網】本文就超高壓氧氣壓縮充灌系統從設計到使用過程中的安全性做一全面分析與評價,提出預防燃爆事故發生的措施。
物質燃燒具備三個必要條件:可燃物、助燃物和燃燒溫度(點火源)。氧氣是一種最常見的助燃物(氧化劑),本系統是制取儲運高純度氧氣,所以防止燃爆要從可燃物及燃燒溫度兩方面采取措施控制燃爆的發生。
一、壓縮機及充灌系統的安全性設計
氧氣是一種強氧化劑,易于與其它物質反應起火,所以,氧氣壓縮充灌過程中除要遵從一般的安全氣體壓縮充灌如空氣、氮氣等規律規則外,還一定要注重燃爆的防范。
從設計角度來看,筆者公司設計制造的超高壓氧氣壓縮機及充灌系統,從以下幾個方面確保了使用安全:
1.壓縮機結構的安全設計
采用全無油潤滑往復活塞結構壓縮機。
壓縮機結構圖:
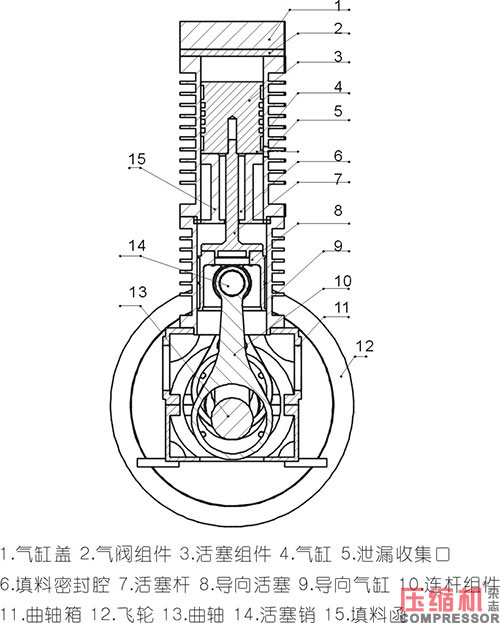
從上圖可知,壓縮機的運動機構,如曲軸連桿的旋轉運動、導向活塞及活塞的往復直線運動都是無需另加稀油潤滑。這臺壓縮機,旋轉運動采用的是密封脂潤滑軸承,往復運動采用的是自潤滑材料。壓縮機機體內無稀潤滑油,密封軸承采用抗氧化全氟潤滑脂。
因為高溫高壓氧氣與油接觸會發生巨烈反應,壓縮機完全無油,大幅度降低了燃爆事故的可能性,為壓縮機的安全使用奠定了基礎;
壓縮機采用四列立式結構,各級氣缸聚集在一起,利用一個外置風機進行吹風換熱,換熱充分,控制氧氣壓縮過程溫度處于較低水平。壓縮機外形如下圖所示:
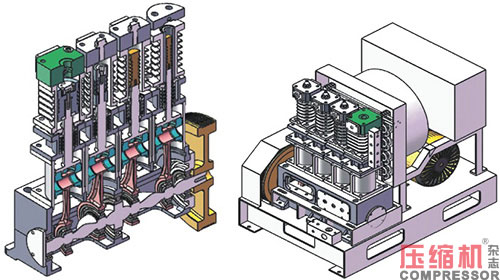
理論各級排氣溫度不大于130℃,實際控制在100℃以內。
為保證壓縮機性能的可靠性及安全性,壓縮機設計時采取低轉速的方式。理論計算轉速為200rpm。極低的轉速延長易損件使用壽命,確保了壓縮機運行安全。
壓縮機內被壓縮的氣體介質,其流速的快慢不僅影響壓縮機的效率,對于氧氣介質,過快的流速也可導致壓縮機發生燃爆的安全事故,因此壓縮機各管路內的氧氣流速嚴格按管內允許流速選取。根據壓縮機設計手冊,具體流速數值如下表:

據此,壓縮機高壓級30.0MPa狀態下,氣流設計流速為0.07m/s。
2.壓縮機安全用材
前文述及,氧氣能與許多物質發生化學反應,因此,壓縮機與高純氧氣接觸的零部件必須是化學惰性。所以壓縮機的氣缸、氣閥、缸蓋、管道等材料均選用含碳量低的不銹鋼材料;壓縮機的活塞,由于壓縮機的結構要求采用鋁合金及銅合金,這些材料導熱快,磨擦時不產生火花。壓縮機的活塞環、支承環,采用塑料王之稱的聚四氟乙烯,該材料抗強酸強堿不氧化的特性。壓縮機的靜態密封環采用化學穩定性極好的氟膠O型圈;壓縮機的螺紋密封采用四氟生料帶,密封效果好耐老化。
壓縮機各承壓零部件做1.5倍工作壓力的水壓試驗,壓縮機氣管路壁厚適中,能夠承受相應的氣體壓力。
高壓管道采用焊接方式的,做射線探傷檢查。
3.壓縮機安全防護設計
為保證壓縮機安全運行,各級設的安全閥,在級間壓力超過其設定值時,安全閥打開,泄放壓縮機壓縮腔及管道內壓力。
各級設溫度顯示,末級設溫度超標強制停機。
風機故障強制停機。
壓縮機電動機設置過載停機。
壓縮機設置進氣壓低保護,當進氣壓力低于設定值時壓縮機停機。
壓縮機設置排氣壓力保護,當排氣壓力高于30.0MPa時,壓縮機停機。
壓縮機進氣及各級排氣設過濾器,防止固態顆粒在氣流中移動磨擦而發生燃爆。
壓縮機旋轉帶輪以及換熱風機等設置防護網或防護罩,對人身進行防護。
超高壓氧氣充灌系統,設計成下圖所示的流程:
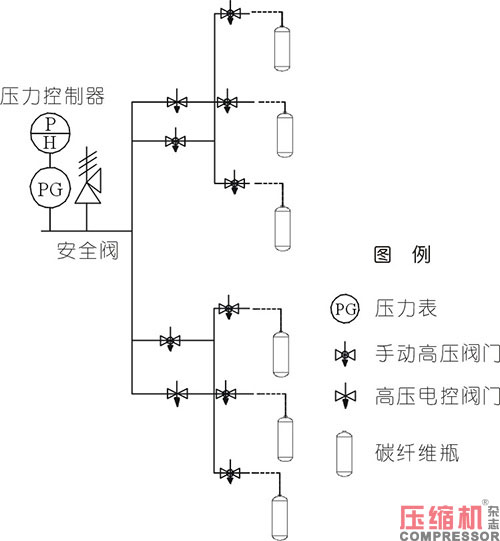
經壓縮機壓縮升壓的高純度高壓力氧氣,由連接管道送至充灌排,在充灌排上裝有壓力傳感器,當氣瓶壓力低于設定值時,高壓自動閥門打開,同時對三個氣瓶充裝。當壓力達到30MPa時,壓力傳感器動作,高壓自動閥門關閉,完成一個周期的充裝。
充灌壓力可于系統中現場設定,低壓1.0MPa,高壓30.0MPa;高壓電動閥門并聯手動閥門,高壓電動閥門出問題時,可改為手動操作;
每路充灌排上安裝壓力傳感器,到壓力開關機或轉換充灌;
充灌排上安裝有安全閥,超壓自動打開,確保使用安全;
為提高充裝效率,設為一用一備兩路每路3個共6個充注接口,兩路壓力控制自動切換;
為保證充裝高壓氧氣操作過程的安全性,要求三個充注口同時對三個氧氣瓶充注,達到控制充灌速度,確保碳纖維瓶充注溫度不大于50℃:
高壓氧氣充瓶速率的控制:采用三只20L碳纖維瓶同時充注的操作方式,壓縮機流量每小時6標態立方米,換算每分鐘為:0.1標態立方米,即100升。3只20L碳纖維瓶總共容積60升,充瓶速率約為0.17MPa/min,充灌限速0.2MPa/min。
規定高壓碳纖維氧氣瓶充灌過程中的溫升不得超過50℃。
二、壓縮機及充灌系統的工藝安全保障
1.脫脂
機器零件裝配前采用超聲波加脫脂劑的方法脫脂。具體方法是:將勾兌好的脫脂液在超聲波容劑槽內加熱后,放入要脫脂的零配件,開啟超聲波在加熱的狀況下清洗至少15分鐘,然后取出已脫脂的零部件,用高壓水槍在無油的環境中沖洗,然后用無油壓縮空氣吹除零件表面的水漬。
脫脂后的壓縮機零配件,在無油的環境下進行安裝,安裝過程中不得再帶入油脂。某些零件因潤滑考慮必須涂抹潤滑脂,如螺紋防咬死、O型圈涂脂安裝不被切破等,可以涂抹少量的抗氧化全氟潤滑脂。
安裝過程中若發現有零配件沾染油脂,必須重新脫脂后再安裝。
高壓充灌系統中空氣壓縮機必須采用無油空壓機,從空壓機到制氧機之間的連接管道及過濾器閥門等都要求進行脫脂處理,以利于系統運行安全。高壓充灌系統中從制氧機出口到氧氣瓶為止,所有的連接管道都要進行脫脂。
管道的脫脂方法為:
拆散管道,然后封閉一端,從另一端注入四氯化碳清洗液,直至灌滿,晃動管道數分鐘,倒出清洗液,用不含油的壓縮空氣吹干管內清洗液。
管路中的各類閥門的脫脂:閥門類的零配件采用四氯化碳浸洗的方式,將閥門上的線圈等通電元件拆下后,將閥門整體放入清洗液中浸洗攪拌,取出后用無油壓縮空氣吹干。
2.超高壓氧氣灌裝系統裝配工藝安全性
裝配場所:
要求無油無塵的環境進行裝配;
所用工器具必須脫脂。
裝配人員嚴禁配戴含植物纖維的手套進行裝配,裝配人員熟悉裝配要求。裝配過程中時刻注意零配件表面情況,若發現零配件表面有油污,立即中斷裝配重新進行脫脂。
裝配過程中各緊固件必須按規定鈕矩擰緊,管路做好密封,不得將密封膠等密封材料帶入管道內。
裝配完成的機器設備,再一次檢查各零配件正確位置及整機清潔度。
三、高壓氧氣充灌系統實驗及使用安全性
高壓氧氣充灌系統實驗檢驗按下圖流程進行:
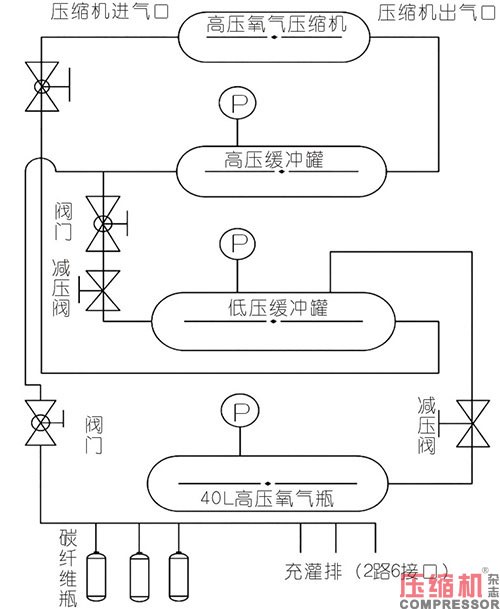
實驗場所必須無油及其它具危險性物質存在;
管線連接時必須確保無油,并密封無泄漏;
碳纖維氧氣瓶必須完好固定在支架上;
充裝系統電器連接線符合規范,有接地保護錯施;
充灌過程中或充灌結束后及時關閉制氧系統,及時卸下充滿的氧氣瓶;
滿瓶(30MPa)氧氣瓶若要放空,必須加放空減壓閥或控制低速小流量;
充裝過程中必須有人值守,及時處理異常情況。
實際使用中,壓力表、安全閥等配件要按期檢定,不合格禁用。
總結
結合已往高壓氧氣壓縮機設計制造經驗,遵從本文要求設計制造的超高壓制供氧系統,完全具備使用的安全性。
參考文獻
郁永章《容積式壓縮機技術手冊》
楊紹侃《活塞式壓縮機設計》
成大先 《機械設計手冊》

來源:本站原創
【壓縮機網】本文就超高壓氧氣壓縮充灌系統從設計到使用過程中的安全性做一全面分析與評價,提出預防燃爆事故發生的措施。
物質燃燒具備三個必要條件:可燃物、助燃物和燃燒溫度(點火源)。氧氣是一種最常見的助燃物(氧化劑),本系統是制取儲運高純度氧氣,所以防止燃爆要從可燃物及燃燒溫度兩方面采取措施控制燃爆的發生。
一、壓縮機及充灌系統的安全性設計
氧氣是一種強氧化劑,易于與其它物質反應起火,所以,氧氣壓縮充灌過程中除要遵從一般的安全氣體壓縮充灌如空氣、氮氣等規律規則外,還一定要注重燃爆的防范。
從設計角度來看,筆者公司設計制造的超高壓氧氣壓縮機及充灌系統,從以下幾個方面確保了使用安全:
1.壓縮機結構的安全設計
采用全無油潤滑往復活塞結構壓縮機。
壓縮機結構圖:
從上圖可知,壓縮機的運動機構,如曲軸連桿的旋轉運動、導向活塞及活塞的往復直線運動都是無需另加稀油潤滑。這臺壓縮機,旋轉運動采用的是密封脂潤滑軸承,往復運動采用的是自潤滑材料。壓縮機機體內無稀潤滑油,密封軸承采用抗氧化全氟潤滑脂。
因為高溫高壓氧氣與油接觸會發生巨烈反應,壓縮機完全無油,大幅度降低了燃爆事故的可能性,為壓縮機的安全使用奠定了基礎;
壓縮機采用四列立式結構,各級氣缸聚集在一起,利用一個外置風機進行吹風換熱,換熱充分,控制氧氣壓縮過程溫度處于較低水平。壓縮機外形如下圖所示:
理論各級排氣溫度不大于130℃,實際控制在100℃以內。
為保證壓縮機性能的可靠性及安全性,壓縮機設計時采取低轉速的方式。理論計算轉速為200rpm。極低的轉速延長易損件使用壽命,確保了壓縮機運行安全。
壓縮機內被壓縮的氣體介質,其流速的快慢不僅影響壓縮機的效率,對于氧氣介質,過快的流速也可導致壓縮機發生燃爆的安全事故,因此壓縮機各管路內的氧氣流速嚴格按管內允許流速選取。根據壓縮機設計手冊,具體流速數值如下表:
據此,壓縮機高壓級30.0MPa狀態下,氣流設計流速為0.07m/s。
2.壓縮機安全用材
前文述及,氧氣能與許多物質發生化學反應,因此,壓縮機與高純氧氣接觸的零部件必須是化學惰性。所以壓縮機的氣缸、氣閥、缸蓋、管道等材料均選用含碳量低的不銹鋼材料;壓縮機的活塞,由于壓縮機的結構要求采用鋁合金及銅合金,這些材料導熱快,磨擦時不產生火花。壓縮機的活塞環、支承環,采用塑料王之稱的聚四氟乙烯,該材料抗強酸強堿不氧化的特性。壓縮機的靜態密封環采用化學穩定性極好的氟膠O型圈;壓縮機的螺紋密封采用四氟生料帶,密封效果好耐老化。
壓縮機各承壓零部件做1.5倍工作壓力的水壓試驗,壓縮機氣管路壁厚適中,能夠承受相應的氣體壓力。
高壓管道采用焊接方式的,做射線探傷檢查。
3.壓縮機安全防護設計
為保證壓縮機安全運行,各級設的安全閥,在級間壓力超過其設定值時,安全閥打開,泄放壓縮機壓縮腔及管道內壓力。
各級設溫度顯示,末級設溫度超標強制停機。
風機故障強制停機。
壓縮機電動機設置過載停機。
壓縮機設置進氣壓低保護,當進氣壓力低于設定值時壓縮機停機。
壓縮機設置排氣壓力保護,當排氣壓力高于30.0MPa時,壓縮機停機。
壓縮機進氣及各級排氣設過濾器,防止固態顆粒在氣流中移動磨擦而發生燃爆。
壓縮機旋轉帶輪以及換熱風機等設置防護網或防護罩,對人身進行防護。
超高壓氧氣充灌系統,設計成下圖所示的流程:
經壓縮機壓縮升壓的高純度高壓力氧氣,由連接管道送至充灌排,在充灌排上裝有壓力傳感器,當氣瓶壓力低于設定值時,高壓自動閥門打開,同時對三個氣瓶充裝。當壓力達到30MPa時,壓力傳感器動作,高壓自動閥門關閉,完成一個周期的充裝。
充灌壓力可于系統中現場設定,低壓1.0MPa,高壓30.0MPa;高壓電動閥門并聯手動閥門,高壓電動閥門出問題時,可改為手動操作;
每路充灌排上安裝壓力傳感器,到壓力開關機或轉換充灌;
充灌排上安裝有安全閥,超壓自動打開,確保使用安全;
為提高充裝效率,設為一用一備兩路每路3個共6個充注接口,兩路壓力控制自動切換;
為保證充裝高壓氧氣操作過程的安全性,要求三個充注口同時對三個氧氣瓶充注,達到控制充灌速度,確保碳纖維瓶充注溫度不大于50℃:
高壓氧氣充瓶速率的控制:采用三只20L碳纖維瓶同時充注的操作方式,壓縮機流量每小時6標態立方米,換算每分鐘為:0.1標態立方米,即100升。3只20L碳纖維瓶總共容積60升,充瓶速率約為0.17MPa/min,充灌限速0.2MPa/min。
規定高壓碳纖維氧氣瓶充灌過程中的溫升不得超過50℃。
二、壓縮機及充灌系統的工藝安全保障
1.脫脂
機器零件裝配前采用超聲波加脫脂劑的方法脫脂。具體方法是:將勾兌好的脫脂液在超聲波容劑槽內加熱后,放入要脫脂的零配件,開啟超聲波在加熱的狀況下清洗至少15分鐘,然后取出已脫脂的零部件,用高壓水槍在無油的環境中沖洗,然后用無油壓縮空氣吹除零件表面的水漬。
脫脂后的壓縮機零配件,在無油的環境下進行安裝,安裝過程中不得再帶入油脂。某些零件因潤滑考慮必須涂抹潤滑脂,如螺紋防咬死、O型圈涂脂安裝不被切破等,可以涂抹少量的抗氧化全氟潤滑脂。
安裝過程中若發現有零配件沾染油脂,必須重新脫脂后再安裝。
高壓充灌系統中空氣壓縮機必須采用無油空壓機,從空壓機到制氧機之間的連接管道及過濾器閥門等都要求進行脫脂處理,以利于系統運行安全。高壓充灌系統中從制氧機出口到氧氣瓶為止,所有的連接管道都要進行脫脂。
管道的脫脂方法為:
拆散管道,然后封閉一端,從另一端注入四氯化碳清洗液,直至灌滿,晃動管道數分鐘,倒出清洗液,用不含油的壓縮空氣吹干管內清洗液。
管路中的各類閥門的脫脂:閥門類的零配件采用四氯化碳浸洗的方式,將閥門上的線圈等通電元件拆下后,將閥門整體放入清洗液中浸洗攪拌,取出后用無油壓縮空氣吹干。
2.超高壓氧氣灌裝系統裝配工藝安全性
裝配場所:
要求無油無塵的環境進行裝配;
所用工器具必須脫脂。
裝配人員嚴禁配戴含植物纖維的手套進行裝配,裝配人員熟悉裝配要求。裝配過程中時刻注意零配件表面情況,若發現零配件表面有油污,立即中斷裝配重新進行脫脂。
裝配過程中各緊固件必須按規定鈕矩擰緊,管路做好密封,不得將密封膠等密封材料帶入管道內。
裝配完成的機器設備,再一次檢查各零配件正確位置及整機清潔度。
三、高壓氧氣充灌系統實驗及使用安全性
高壓氧氣充灌系統實驗檢驗按下圖流程進行:
實驗場所必須無油及其它具危險性物質存在;
管線連接時必須確保無油,并密封無泄漏;
碳纖維氧氣瓶必須完好固定在支架上;
充裝系統電器連接線符合規范,有接地保護錯施;
充灌過程中或充灌結束后及時關閉制氧系統,及時卸下充滿的氧氣瓶;
滿瓶(30MPa)氧氣瓶若要放空,必須加放空減壓閥或控制低速小流量;
充裝過程中必須有人值守,及時處理異常情況。
實際使用中,壓力表、安全閥等配件要按期檢定,不合格禁用。
總結
結合已往高壓氧氣壓縮機設計制造經驗,遵從本文要求設計制造的超高壓制供氧系統,完全具備使用的安全性。
參考文獻
郁永章《容積式壓縮機技術手冊》
楊紹侃《活塞式壓縮機設計》
成大先 《機械設計手冊》
來源:本站原創
網友評論
條評論
最新評論