【壓縮機網】1、引言
往復式壓縮機氣缸的進、排氣是通過氣閥來完成的。氣閥是否能按設計參數進行進、排氣操作,其中的一個關鍵點是氣閥不能漏氣。這就要求氣閥墊圈的接觸壓力在合理的范圍。如果接觸壓力太小,墊圈就起不到密封的作用;如果接觸壓力太大,又容易導致墊圈變形超出范圍。另一方面,壓縮機運行過程中,墊圈接觸壓力是隨著氣閥進、排氣的循環過程而不斷變化的,這就增加了墊圈密封的難度??紤]到墊圈接觸壓力主要由壓閥螺栓預緊力和墊圈結構來決定,其中壓閥螺栓預緊力很容易調整而墊圈結構一旦確定就很難更改,因此,墊圈結構是氣閥密封設計的重點。
本文使用ANSYS有限元程序,對如圖1所示氣缸的兩種氣閥墊圈進行了應力分析。通過對比分析兩種氣閥墊圈,說明其結構優劣,以及優化和改進的方向,可為氣閥墊圈典型設計結構提供參考依據。圖2表示了優化前截面為近似平行四邊形的氣閥墊圈,圖3表示了優化后截面為長方形的氣閥墊圈。
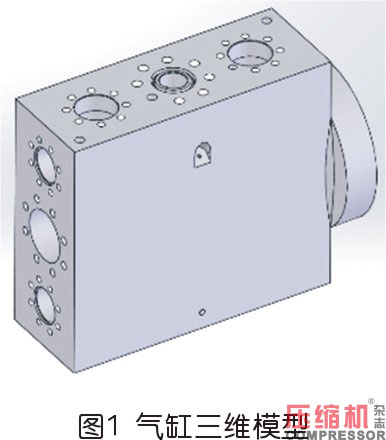
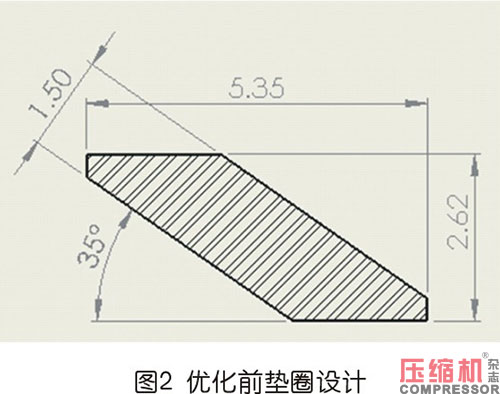
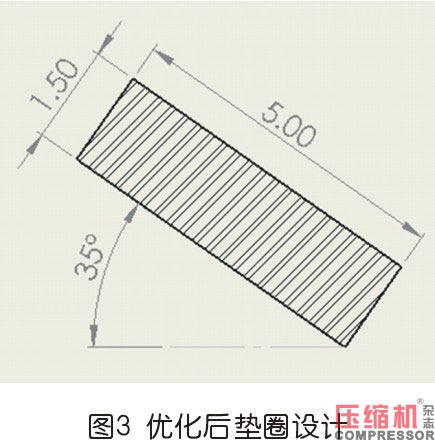
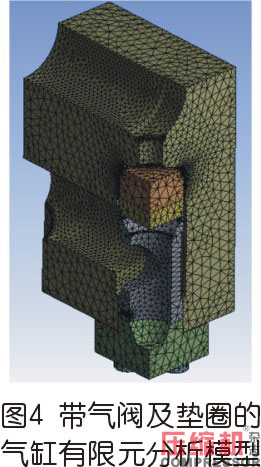
2、氣缸有限元分析模型
根據氣缸結構特點和載荷特性,取其1/8對稱結構,用ANSYS分析程序生成有限元模型如圖4所示。該有限元模型包含了缸體、氣閥及密封墊圈。各部件的材料特性如表1所示。
在有限元分析模型中,相對于周圍零件,氣閥墊圈尺寸較小,因此對氣閥墊圈以及和其相接觸的壓縮缸部件局部部位采用如圖5所示較細密的網格劃分,以捕捉到準確的應力變化。
根據氣缸分析模型結構的對稱性,在其三個對稱面上施加對稱約束邊界條件。氣閥密封墊圈和缸體以及氣閥的兩個接觸面采用摩擦接觸,取摩擦系數0.1。其它各零件之間的接觸面均假設為無摩擦可滑動接觸。
載荷方面,分別對壓縮缸進氣端和排氣端進行4個不同氣壓狀況載荷分析,具體如表2所示。
氣閥密封墊圈有限元分析采用四個荷載逐步加載。第一個荷載步是只加螺栓的預緊力,第二個荷載步是增加氣閥室的工作氣壓,第三個荷載步是增加壓縮缸進氣氣壓,第四個荷載步是增加壓縮缸排氣氣壓。
3、改進前氣閥墊圈有限元分析結果
圖6至圖9顯示了改進前排氣閥墊圈在四個載荷作用下的應力分布圖。從圖中可以看出,墊圈的應力分布很不均勻且隨著氣缸和排氣閥腔的壓力變化而變化。
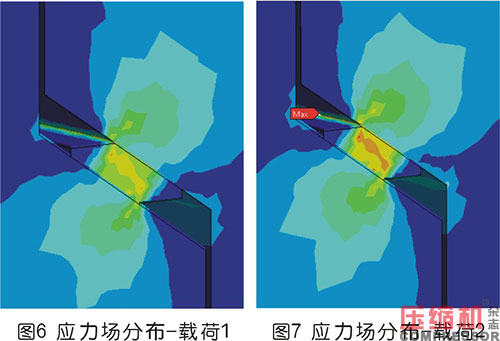
圖10和圖11分別是排氣閥墊圈和進氣閥墊圈在其邊緣處壓力匯總圖,以及根據ASME VIII Div. 1計算得出的最小墊圈座壓力和最小墊圈工作壓力。從圖中可以看出在載荷2時,即氣閥室工作壓力,氣缸內常壓時,氣閥墊圈表面壓力值最大。在載荷4,即氣閥室和氣缸均為工作壓力時,氣閥墊圈表面壓力值最小。在四種載荷作用下,也就是氣缸的不同工作過程中,氣閥墊圈壓力分布都極不均勻,且局部壓力低于ASME VIII Div. 1要求的最小墊圈工作壓力,說明此墊圈設計需要優化。
4、改進后氣閥墊圈有限元分析結果
圖12至圖15顯示了改進后排氣閥墊圈在四個載荷作用下的應力分布圖。從圖中可以看出,墊圈的應力分布相對較均勻,但也是隨著氣缸和排氣閥腔的壓力變化而變化。
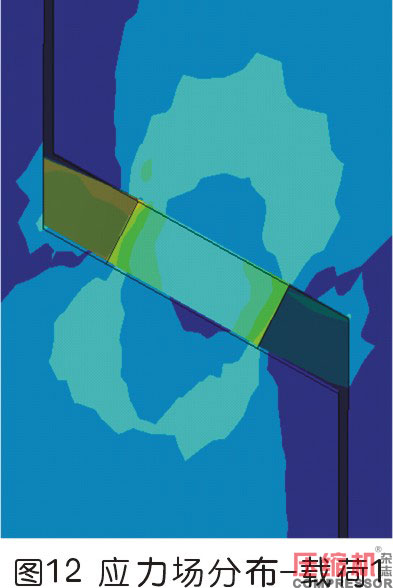
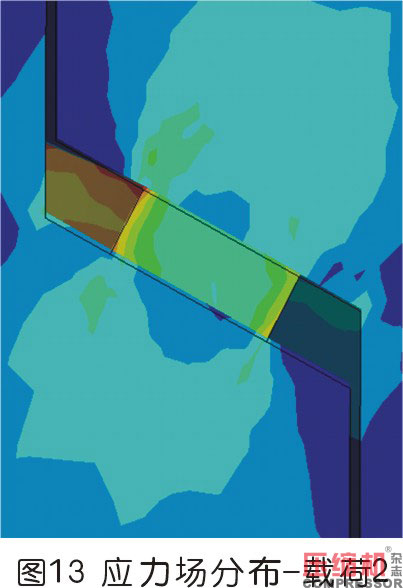
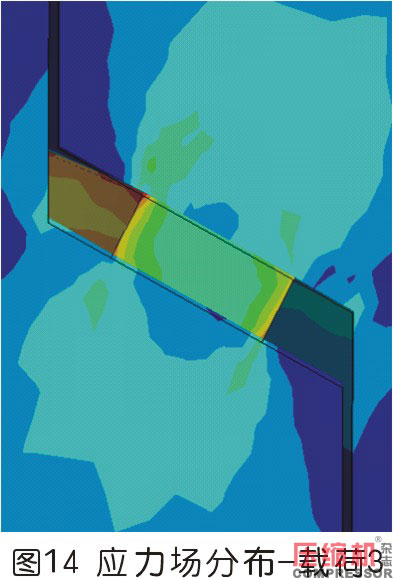
圖16和圖17分別是排氣閥墊圈和進氣閥墊圈在其邊緣處壓力匯總圖,以及根據ASME VIII Div. 1計算得出的最小墊圈座壓力和最小墊圈工作壓力。從圖中可以看出,在四種載荷作用下,也就是氣缸的不同工作過程中,氣閥墊圈壓力均高于ASME VIII Div. 1要求的最小墊圈工作壓力且其壓力分布不均勻性較改進前得到了極大的改善,說明此墊圈優化設計是有效的。
4、分析結果討論
氣閥密封墊圈接觸表面合適的壓力是保證氣密性的必要條件。工作時墊圈接觸面壓力要高于ASME VIII Div 1要求的最低座壓壓力和根據氣閥氣壓計算出的最低工作壓力。
改進前模型中墊圈兩接觸面的壓力分布極不均勻,在前沿邊處(鈍角處)的壓力顯著升高,遠高于墊圈材料的屈服強度,會有塑性變形出現。且局部壓力低于密封需求的最小墊圈工作壓力,不滿足氣閥墊圈設計要求。
改進后的墊圈形狀切除了橫截面銳角部分,橫截面從平行四邊形改變為長方形,減少了前沿邊處(鈍角處)的應力,并且增加了墊圈接觸面寬度,接觸面壓力比較均勻且滿足ASME VIII Div 1要求的最低座壓壓力和最低工作壓力,滿足氣閥墊圈設計要求。
5、結論
本文采用ANSYS有限元程序,對往復式壓縮機氣缸氣閥墊圈進行了應力分析和設計優化。分析結果表明,在氣閥工作過程中,墊圈接觸壓力不斷變化。通過對墊圈結構設計進行改進,其接觸壓力可以滿足氣閥密封要求且壓力分布較均勻,可為氣閥墊圈結構典型設計提供技術參考依據。
參考文獻
1. C. Lee, K. Chiang, W. Chen, Rong. Chen, Design and Analysis of Gasket Sealing of Cylinder Head under Engine Operation Conditions, Finite Elements in Analysis and Design, 2005, 41, 1160-1174
2. S.W. Chyuan, Finite element simulation of a twin-cam 16-valve cylinder structure, Finite Elements Analysis and Design, 2000, 35, 199–212.
3. M. Krishna, M. Shunmugam, N. Prasad, A study on the sealing performance of bolted flange joints with gaskets using finite element analysis, International Journal of Pressure Vessels and Piping, 2007, 84(6), 349-357
4. A. Kadam and S. Ingale, Experimental and Numerical Analysis of Effect of Washer Size and Preload on Strength of Double Lap Double Bolted GFRP-To-Steel Joint, International Journal of Science and Research, 2017, 6(6), 2397-2402
5. ANSYS User Manual, 2016. 6. ASME Boiler & Pressure Vessel Code VIII, Div. 1, New York: ASME, 2001.
來源:本站原創
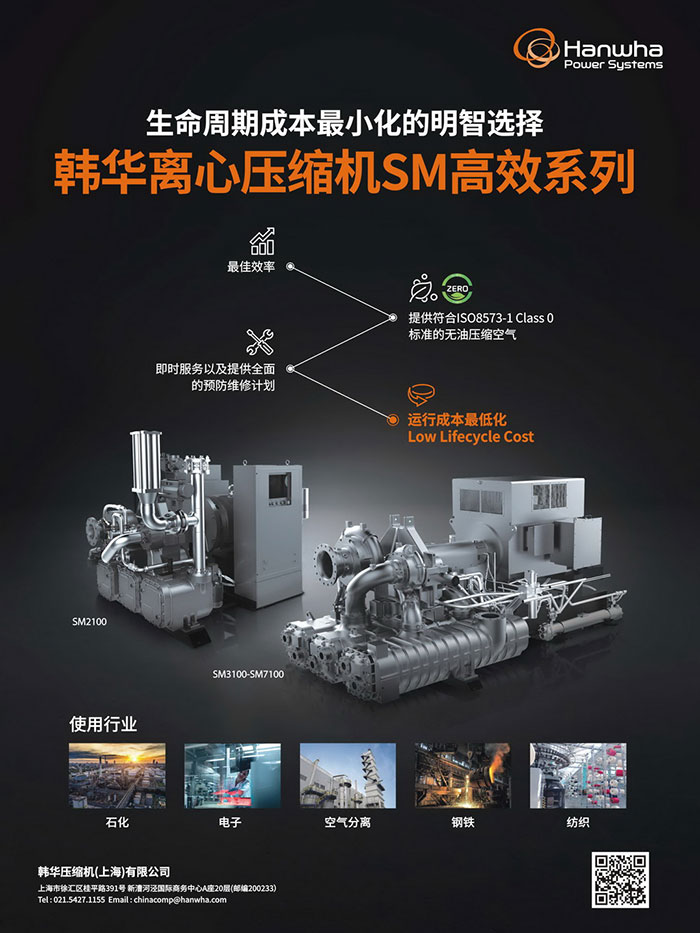
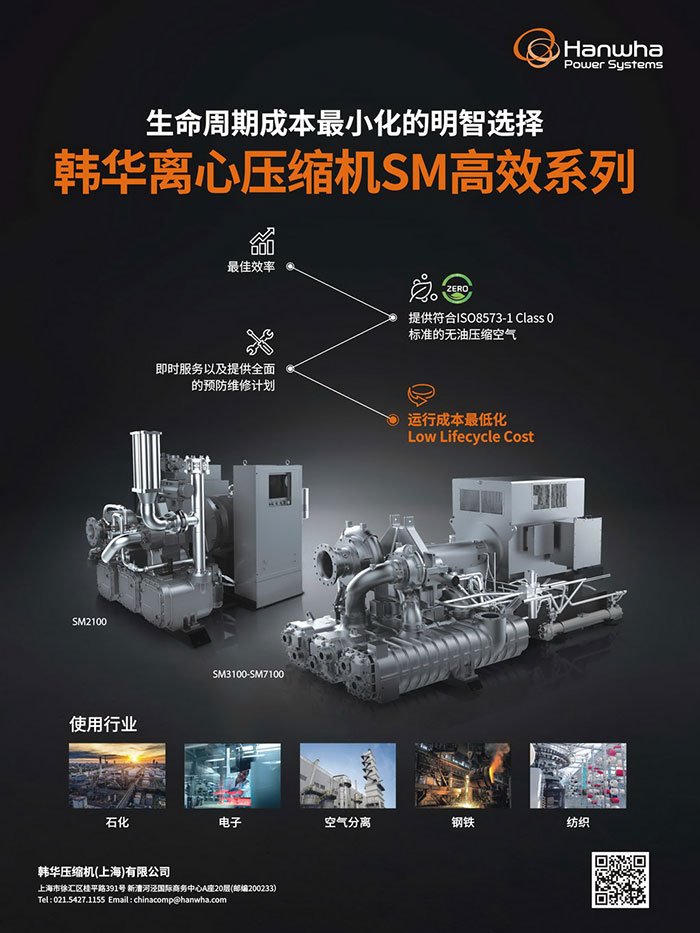
往復式壓縮機氣缸的進、排氣是通過氣閥來完成的。氣閥是否能按設計參數進行進、排氣操作,其中的一個關鍵點是氣閥不能漏氣。這就要求氣閥墊圈的接觸壓力在合理的范圍。如果接觸壓力太小,墊圈就起不到密封的作用;如果接觸壓力太大,又容易導致墊圈變形超出范圍。另一方面,壓縮機運行過程中,墊圈接觸壓力是隨著氣閥進、排氣的循環過程而不斷變化的,這就增加了墊圈密封的難度??紤]到墊圈接觸壓力主要由壓閥螺栓預緊力和墊圈結構來決定,其中壓閥螺栓預緊力很容易調整而墊圈結構一旦確定就很難更改,因此,墊圈結構是氣閥密封設計的重點。
本文使用ANSYS有限元程序,對如圖1所示氣缸的兩種氣閥墊圈進行了應力分析。通過對比分析兩種氣閥墊圈,說明其結構優劣,以及優化和改進的方向,可為氣閥墊圈典型設計結構提供參考依據。圖2表示了優化前截面為近似平行四邊形的氣閥墊圈,圖3表示了優化后截面為長方形的氣閥墊圈。
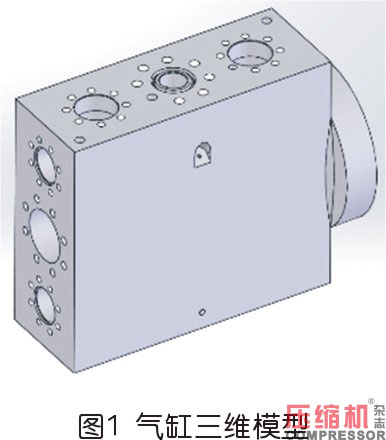
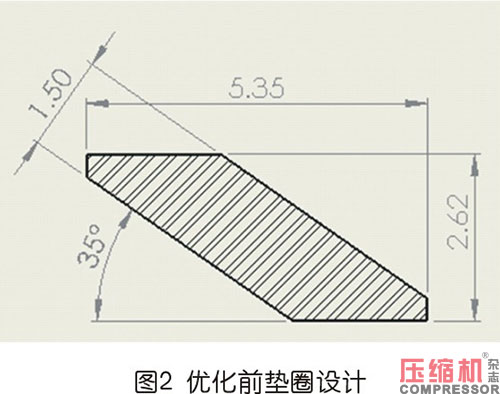
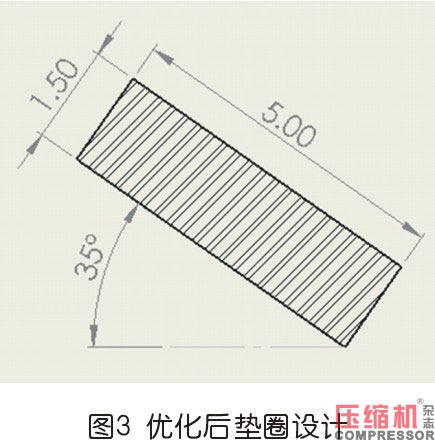
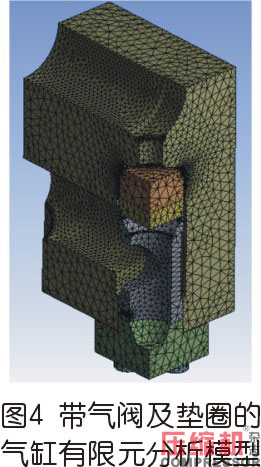
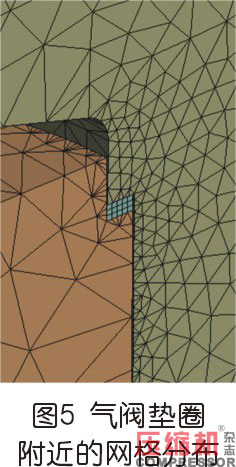
2、氣缸有限元分析模型
根據氣缸結構特點和載荷特性,取其1/8對稱結構,用ANSYS分析程序生成有限元模型如圖4所示。該有限元模型包含了缸體、氣閥及密封墊圈。各部件的材料特性如表1所示。
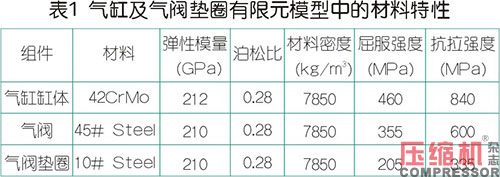
在有限元分析模型中,相對于周圍零件,氣閥墊圈尺寸較小,因此對氣閥墊圈以及和其相接觸的壓縮缸部件局部部位采用如圖5所示較細密的網格劃分,以捕捉到準確的應力變化。
根據氣缸分析模型結構的對稱性,在其三個對稱面上施加對稱約束邊界條件。氣閥密封墊圈和缸體以及氣閥的兩個接觸面采用摩擦接觸,取摩擦系數0.1。其它各零件之間的接觸面均假設為無摩擦可滑動接觸。
載荷方面,分別對壓縮缸進氣端和排氣端進行4個不同氣壓狀況載荷分析,具體如表2所示。
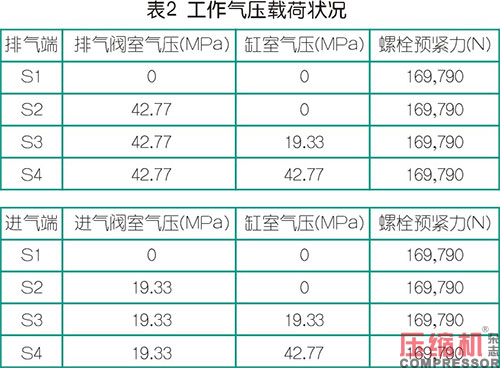
氣閥密封墊圈有限元分析采用四個荷載逐步加載。第一個荷載步是只加螺栓的預緊力,第二個荷載步是增加氣閥室的工作氣壓,第三個荷載步是增加壓縮缸進氣氣壓,第四個荷載步是增加壓縮缸排氣氣壓。
3、改進前氣閥墊圈有限元分析結果
圖6至圖9顯示了改進前排氣閥墊圈在四個載荷作用下的應力分布圖。從圖中可以看出,墊圈的應力分布很不均勻且隨著氣缸和排氣閥腔的壓力變化而變化。
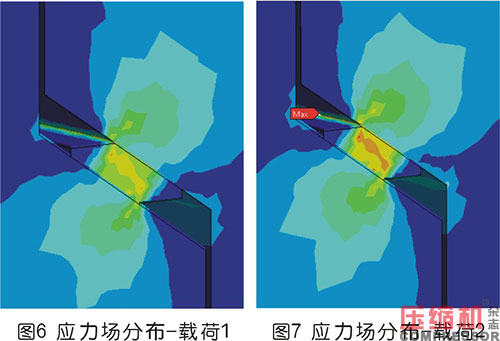
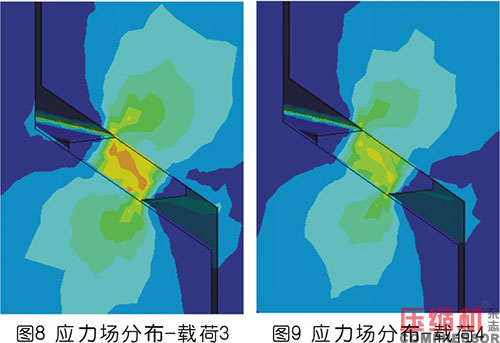
圖10和圖11分別是排氣閥墊圈和進氣閥墊圈在其邊緣處壓力匯總圖,以及根據ASME VIII Div. 1計算得出的最小墊圈座壓力和最小墊圈工作壓力。從圖中可以看出在載荷2時,即氣閥室工作壓力,氣缸內常壓時,氣閥墊圈表面壓力值最大。在載荷4,即氣閥室和氣缸均為工作壓力時,氣閥墊圈表面壓力值最小。在四種載荷作用下,也就是氣缸的不同工作過程中,氣閥墊圈壓力分布都極不均勻,且局部壓力低于ASME VIII Div. 1要求的最小墊圈工作壓力,說明此墊圈設計需要優化。
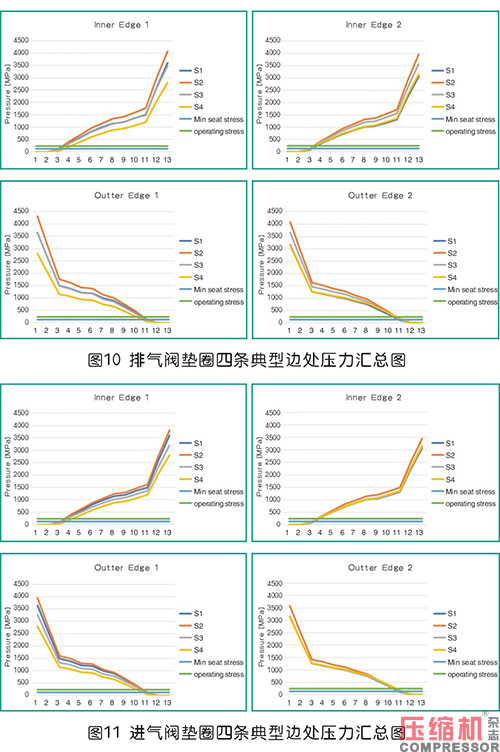
4、改進后氣閥墊圈有限元分析結果
圖12至圖15顯示了改進后排氣閥墊圈在四個載荷作用下的應力分布圖。從圖中可以看出,墊圈的應力分布相對較均勻,但也是隨著氣缸和排氣閥腔的壓力變化而變化。
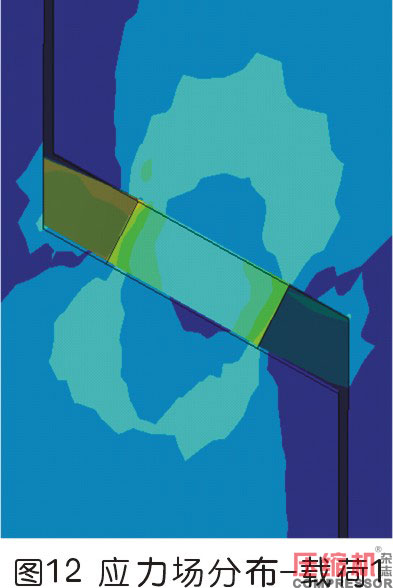
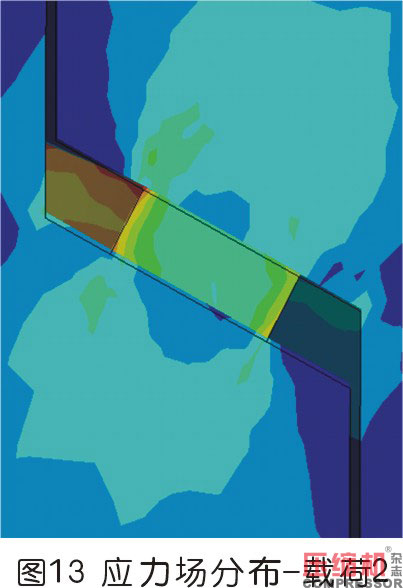
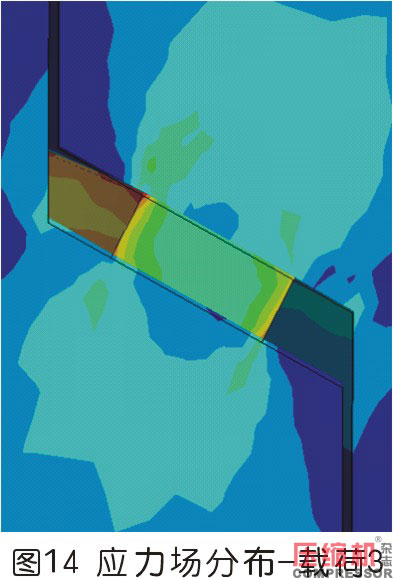
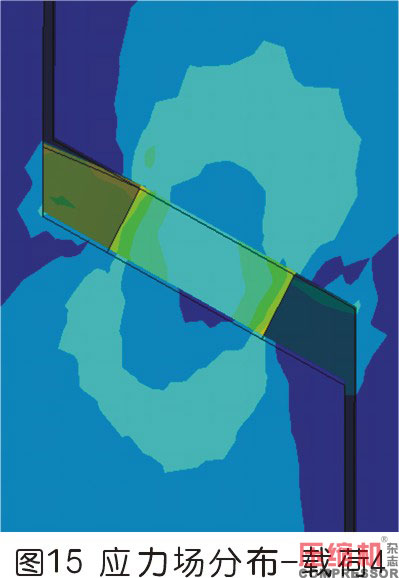
圖16和圖17分別是排氣閥墊圈和進氣閥墊圈在其邊緣處壓力匯總圖,以及根據ASME VIII Div. 1計算得出的最小墊圈座壓力和最小墊圈工作壓力。從圖中可以看出,在四種載荷作用下,也就是氣缸的不同工作過程中,氣閥墊圈壓力均高于ASME VIII Div. 1要求的最小墊圈工作壓力且其壓力分布不均勻性較改進前得到了極大的改善,說明此墊圈優化設計是有效的。
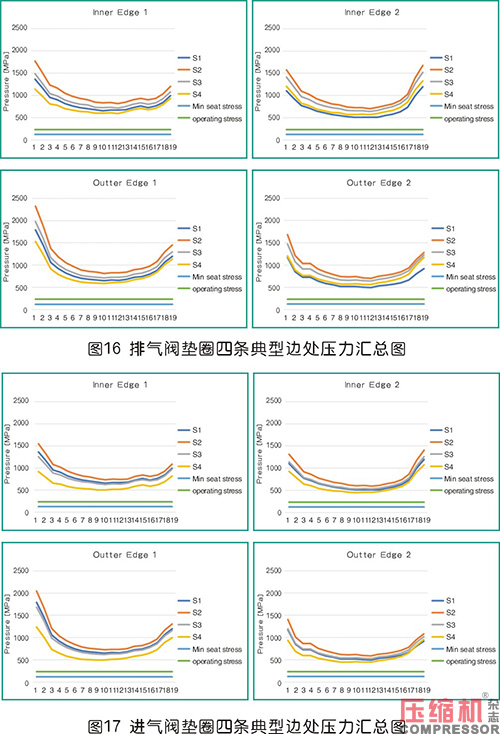
4、分析結果討論
氣閥密封墊圈接觸表面合適的壓力是保證氣密性的必要條件。工作時墊圈接觸面壓力要高于ASME VIII Div 1要求的最低座壓壓力和根據氣閥氣壓計算出的最低工作壓力。
改進前模型中墊圈兩接觸面的壓力分布極不均勻,在前沿邊處(鈍角處)的壓力顯著升高,遠高于墊圈材料的屈服強度,會有塑性變形出現。且局部壓力低于密封需求的最小墊圈工作壓力,不滿足氣閥墊圈設計要求。
改進后的墊圈形狀切除了橫截面銳角部分,橫截面從平行四邊形改變為長方形,減少了前沿邊處(鈍角處)的應力,并且增加了墊圈接觸面寬度,接觸面壓力比較均勻且滿足ASME VIII Div 1要求的最低座壓壓力和最低工作壓力,滿足氣閥墊圈設計要求。
5、結論
本文采用ANSYS有限元程序,對往復式壓縮機氣缸氣閥墊圈進行了應力分析和設計優化。分析結果表明,在氣閥工作過程中,墊圈接觸壓力不斷變化。通過對墊圈結構設計進行改進,其接觸壓力可以滿足氣閥密封要求且壓力分布較均勻,可為氣閥墊圈結構典型設計提供技術參考依據。
參考文獻
1. C. Lee, K. Chiang, W. Chen, Rong. Chen, Design and Analysis of Gasket Sealing of Cylinder Head under Engine Operation Conditions, Finite Elements in Analysis and Design, 2005, 41, 1160-1174
2. S.W. Chyuan, Finite element simulation of a twin-cam 16-valve cylinder structure, Finite Elements Analysis and Design, 2000, 35, 199–212.
3. M. Krishna, M. Shunmugam, N. Prasad, A study on the sealing performance of bolted flange joints with gaskets using finite element analysis, International Journal of Pressure Vessels and Piping, 2007, 84(6), 349-357
4. A. Kadam and S. Ingale, Experimental and Numerical Analysis of Effect of Washer Size and Preload on Strength of Double Lap Double Bolted GFRP-To-Steel Joint, International Journal of Science and Research, 2017, 6(6), 2397-2402
5. ANSYS User Manual, 2016. 6. ASME Boiler & Pressure Vessel Code VIII, Div. 1, New York: ASME, 2001.
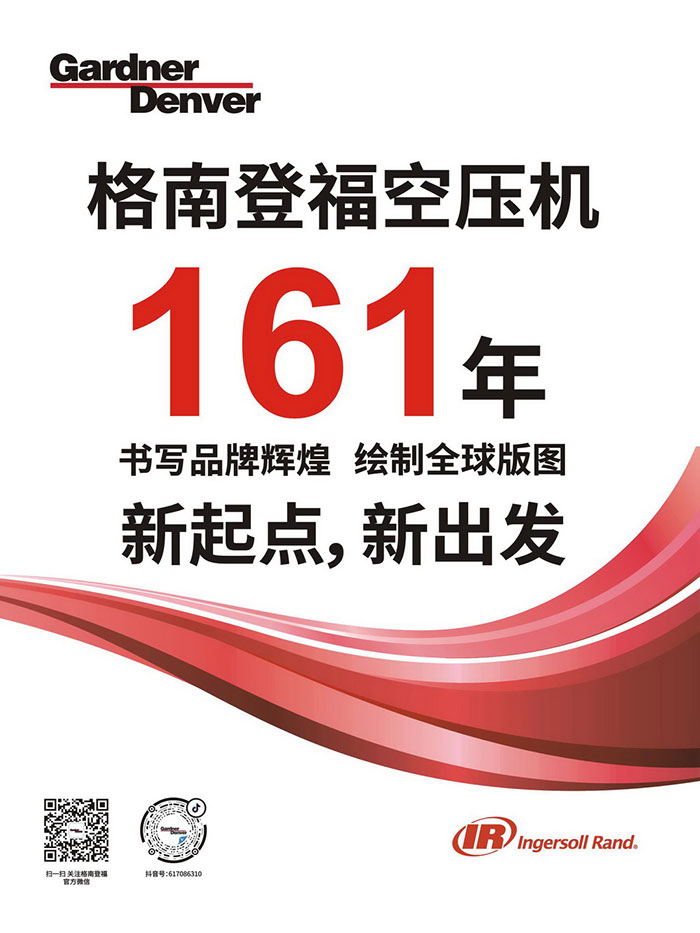
來源:本站原創
網友評論
條評論
最新評論