【壓縮機網】1、排氣管振動的原因
壓縮機強烈的管道振動會使管道附件特別是與管道相連的部件連接松動,輕則引起泄漏,重則由破裂引起爆炸;引起零件的疲勞破壞,降低整個裝置的疲勞壽命。為保證壓縮機的安全運行,有必要對管道振動的機理進行分析和研究。管道內流體流速過快產生湍流邊界層分離而形成渦流,會引起振動。管道系統的振動主要是由機械振動、管道內部介質脈動以及支吊架安裝不當引起。
使用測振儀對某型號移動式螺桿機進行測試,發現其在空載時運動比較平穩,振動輕微;當對移動機加載測試時,振動劇烈,由振動產生的噪聲也比較厲害,由此可以肯定該壓縮機的管道振動主要是由氣流脈動引起的。
2、對排氣管進行模態分析
圖1為排氣管的實體造型圖。此排氣管是從壓縮機主機出來到油氣分離器中間的一段,材質為普通碳鋼,彈性模量為210GPa,泊松比為0.28,密度為7800kg/m2。管外徑是89mm,管壁厚為4.5mm,管的彎角為90°。
2.1 排氣管內部流體的運動軌跡
針對排氣管的振動問題,用Solidworks 軟件對排氣管進行實體建模,然后導入內部模塊Flow simula—tion進行排氣管內部流場的模擬。對模型加上封蓋沿中心線剖分后,進行計算域和流體子域的限定,插人流體的邊界條件:入口的體積流量Q為20m3/min,化成軟件默認的單位m3/h后的數值為0.33,氣體的流動狀態假設為均勻流動,按理想氣體狀態進行處理;出口進行靜壓處理,從而得出排氣管內部流體的流動軌跡如圖2所示。
從上圖可以看出,在管道的拐彎處由于受到內部氣流的沖擊壓力較大,在直管部分氣流相對平穩,所以管道拐彎處的壓力脈動是引起管道頻率變化的主要因素。
2.2 排氣管的頻率分析
在原有的實體模型的基礎上,將模型導人Solid—Works的內部插件Simulation,進行頻率設定、編輯應用材料、添加固定夾具(由于排氣管的兩端都有構件相連,所以為兩端固定型),內壁均勻添加1.9MPa的壓力進行分析。在生成網格后運行得出管道的多階固有頻率和振型圖,從而依據仿真的手段對管道的固有特性加以了解。由于篇幅限制,選取管道的第3、4階振型列舉如圖3所示。
在得出排氣管的各階振型之后,可以看出排氣管相對的變化趨勢,但是要有更準確的仿真結果,需要管道各階固有頻率的實際數據,現僅列舉前六階如表l所示。
壓縮機的激振頻率可由下述公式計算。
其中,n為壓縮機轉速(r/min);m為激發頻率的階數。
此移動機的轉速為2000r/min,產生的激振頻率為200Hz,理論上激振頻率在0.8~1.2范圍內為共振區,即160Hz~240Hz為共振區。從表2中的數據可以得知,第二階頻率落在了共振區的范圍內,由此可以斷定共振也是引起壓縮機排氣管管道強烈振動的原因之一。
綜上所述,此移動式壓縮機排氣管振動是管道的固有頻率與激發頻率范圍重合(外因)以及氣流的脈動(內因)這兩項因素共同引起的。
3、控制管道振動的措施
該壓縮機的激振力主要來自管道拐彎處或異徑管處,因此盡量減少彎頭的數目可以減低振動。另外,彎管處的激振力大小與轉彎的角度有關閻,所以盡量加大管道彎角處的角度可以有效降低振動。所以管道由原來的90°彎角改為1200°。對改進后的模型做模態分析,得到改進后管道的各階固有頻率改變為如表2所示。
對改進前和改進后的管道分析進行對比,通過軟件模擬發現改進后的管道的固有頻率得到了有效的改善,各階頻率都避開了共振區而且又能減小流體的壓力波動,從而達到了降低振動的目的。
4、結束語
通過對該型號移動式螺桿壓縮機排氣管進行仿真分析,找出了引起管道振動的主要原因。在多種因素的綜合考慮下,采用了改變管道彎度的方案,實施后發現此方案實際有效,是減振的一種可靠的方法,為壓縮機類似問題的解決提供一定的參考。
【壓縮機網】1、排氣管振動的原因
壓縮機強烈的管道振動會使管道附件特別是與管道相連的部件連接松動,輕則引起泄漏,重則由破裂引起爆炸;引起零件的疲勞破壞,降低整個裝置的疲勞壽命。為保證壓縮機的安全運行,有必要對管道振動的機理進行分析和研究。管道內流體流速過快產生湍流邊界層分離而形成渦流,會引起振動。管道系統的振動主要是由機械振動、管道內部介質脈動以及支吊架安裝不當引起。
使用測振儀對某型號移動式螺桿機進行測試,發現其在空載時運動比較平穩,振動輕微;當對移動機加載測試時,振動劇烈,由振動產生的噪聲也比較厲害,由此可以肯定該壓縮機的管道振動主要是由氣流脈動引起的。
2、對排氣管進行模態分析
圖1為排氣管的實體造型圖。此排氣管是從壓縮機主機出來到油氣分離器中間的一段,材質為普通碳鋼,彈性模量為210GPa,泊松比為0.28,密度為7800kg/m2。管外徑是89mm,管壁厚為4.5mm,管的彎角為90°。
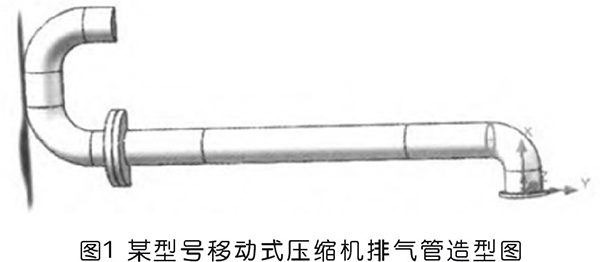
2.1 排氣管內部流體的運動軌跡
針對排氣管的振動問題,用Solidworks 軟件對排氣管進行實體建模,然后導入內部模塊Flow simula—tion進行排氣管內部流場的模擬。對模型加上封蓋沿中心線剖分后,進行計算域和流體子域的限定,插人流體的邊界條件:入口的體積流量Q為20m3/min,化成軟件默認的單位m3/h后的數值為0.33,氣體的流動狀態假設為均勻流動,按理想氣體狀態進行處理;出口進行靜壓處理,從而得出排氣管內部流體的流動軌跡如圖2所示。
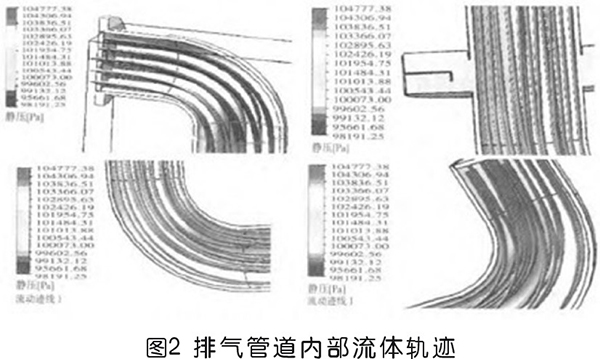
從上圖可以看出,在管道的拐彎處由于受到內部氣流的沖擊壓力較大,在直管部分氣流相對平穩,所以管道拐彎處的壓力脈動是引起管道頻率變化的主要因素。
2.2 排氣管的頻率分析
在原有的實體模型的基礎上,將模型導人Solid—Works的內部插件Simulation,進行頻率設定、編輯應用材料、添加固定夾具(由于排氣管的兩端都有構件相連,所以為兩端固定型),內壁均勻添加1.9MPa的壓力進行分析。在生成網格后運行得出管道的多階固有頻率和振型圖,從而依據仿真的手段對管道的固有特性加以了解。由于篇幅限制,選取管道的第3、4階振型列舉如圖3所示。
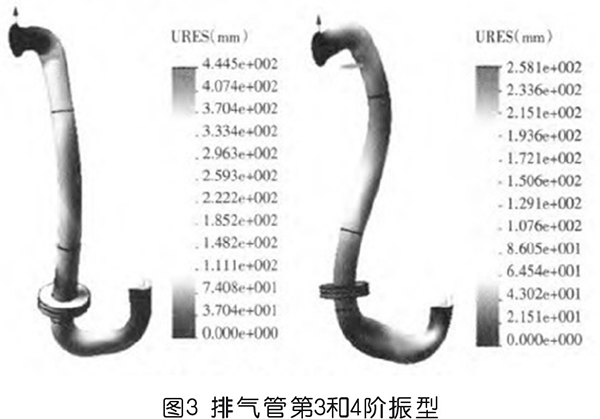
在得出排氣管的各階振型之后,可以看出排氣管相對的變化趨勢,但是要有更準確的仿真結果,需要管道各階固有頻率的實際數據,現僅列舉前六階如表l所示。
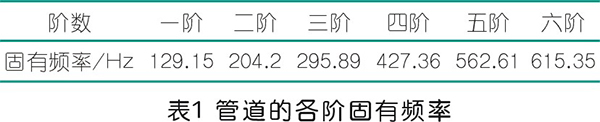
壓縮機的激振頻率可由下述公式計算。
其中,n為壓縮機轉速(r/min);m為激發頻率的階數。
此移動機的轉速為2000r/min,產生的激振頻率為200Hz,理論上激振頻率在0.8~1.2范圍內為共振區,即160Hz~240Hz為共振區。從表2中的數據可以得知,第二階頻率落在了共振區的范圍內,由此可以斷定共振也是引起壓縮機排氣管管道強烈振動的原因之一。
綜上所述,此移動式壓縮機排氣管振動是管道的固有頻率與激發頻率范圍重合(外因)以及氣流的脈動(內因)這兩項因素共同引起的。
3、控制管道振動的措施
該壓縮機的激振力主要來自管道拐彎處或異徑管處,因此盡量減少彎頭的數目可以減低振動。另外,彎管處的激振力大小與轉彎的角度有關閻,所以盡量加大管道彎角處的角度可以有效降低振動。所以管道由原來的90°彎角改為1200°。對改進后的模型做模態分析,得到改進后管道的各階固有頻率改變為如表2所示。
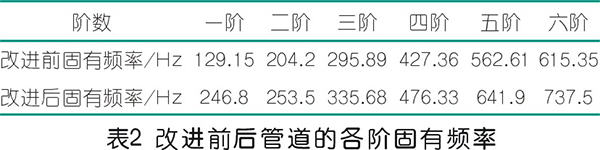
對改進前和改進后的管道分析進行對比,通過軟件模擬發現改進后的管道的固有頻率得到了有效的改善,各階頻率都避開了共振區而且又能減小流體的壓力波動,從而達到了降低振動的目的。
4、結束語
通過對該型號移動式螺桿壓縮機排氣管進行仿真分析,找出了引起管道振動的主要原因。在多種因素的綜合考慮下,采用了改變管道彎度的方案,實施后發現此方案實際有效,是減振的一種可靠的方法,為壓縮機類似問題的解決提供一定的參考。
網友評論
條評論
最新評論