一、循環氫壓縮機K-301A/B機組概況
【壓縮機網】1.1主要用途
在加氫精制裝置中,循環氫壓縮機主要用于克服生產裝置系統的阻力降,增加循環氫氣體的壓力,使得未充分參與反應的循環氫氣體物料,經循環氫壓縮機升壓后,重新進入反應系統。因此循環氫壓縮機K-301A/B,其作用是為石腦油加氫裝置反應系統輸送循環氫物料、給系統補氫增壓,把未充分參與反應的循環氫氣體物料,經循環氫壓縮機升壓后,重新送往反應系統中。
1.2主要結構簡述
石腦油加氫裝置循環氫壓縮機K-301A/B機組為固定水冷、一級、對稱平衡型無油潤滑往復活塞式壓縮機,由同步電動機、機身、氣缸曲柄軸、十字頭銷、十字體、活塞桿等零部件組成,由直接裝在主軸上的同步電動機驅動。
1.3主要技術性能
循環氫壓縮機K-301A/B組規格型號為DW-11/15-25,額度流量為11.0Nm3/min,額度吸氣壓力為1.5MPa,額度排氣壓力為2.5MPa,其作用為石腦油加氫裝置反應系統用的循環氫增壓循環,一備一用。該循環氫壓縮機機其詳細的技術性能如表1所示。
1.4 K-301A/B氣閥
氣閥是安裝在壓縮機氣缸上控制氣體進出的部件,分為進氣閥和排氣閥,是壓縮機中z*重要、z*易損壞的部件之一。因此壓縮機運行的經濟性和可靠性,很大程度上取決于氣閥的可靠完好,其壽命的長短,直接影響到壓縮機的運轉率。循環氫壓縮機K-301A/B氣閥為網狀閥,閥片采用了網狀結構,材質為3Cr13;閥座也是材質為3Cr13;氣閥彈簧材質為17—7PH。 一級進氣閥、一級排氣閥,對稱安裝布置。
二、氣閥故障及原因分析
2.1運行狀況及故障統計
汽油加氫改質裝置循環氫壓縮機K-301A/B為反應系統用的循環氫增壓循環,共設2臺,一開一備,設計參數見表2。
K401自2010年9月26日投運,初期試運行總時間404.76h的過程中,多次出現故障停車。具體情況為:開車運行13次,有8次因二段出口溫度高跳車(由現場的檢查和修理情況確定由氣閥引起),4次因氣閥問題停運,1次因刮油環漏油檢修。因氣閥引起的故障停車時間占整個停車時間的90%以上。
該機組自2017年8月25日投運以來,機組多次發生故障停車。其中因氣閥引起的故障停車時間占整個停車時間的80%以上計初步統計,2017年8月25日至2018年2月15日以來,機組因氣閥故障停車維修頻次達到8次,如表2所示。氣閥故障率高,頻繁發生故障,導致機組切換和維修頻次高,操作人員和檢維修人員勞動強度大,嚴重影響裝置的長周期、安全平穩運行。
從表2分析可以看出,在這個周期(6個月)的裝置生產過程中,循環氫壓縮機共發生故障8次,造成2臺機組頻繁切換運行。根據現場檢修情況和對氣閥拆檢情況分析,發現機組氣閥故障主要集中在以下幾個問題:
(1)氣閥內漏;
(2)氣閥部件閥片、彈簧腐蝕斷裂;
(3)機組帶液,氣閥閥座斷裂;
(4)機組催化劑粉塵多,在氣閥上積聚油泥、積碳;
(5)頂開吸氣閥氣量凋節機構卸荷閥設計不合理,容易卡死。
2.2 氣閥故障原因分析
從檢修的情況看,氣閥故障主要表現氣閥泄漏;氣閥閥片、彈簧大量斷裂;閥座上堆積催化劑粉塵、油泥、積碳較多,閥座液擊斷裂。同時機組帶液,粉塵大。從而導致機組在生產運行過程中出現排氣溫度高,排氣量降低,氣閥或氣缸異響等故障現象。因此,根據檢修的情況分析,結合機組實際的運行工況判斷,造成循環氫壓縮機K-301A/B氣閥故障原因主要有以下幾個方面:
(1)氣閥閥片、閥座密封面磨損,閥片、閥座上形成油泥、積碳等雜質,彈簧疲勞斷裂或受力不均勻,導致氣閥內漏,循環氫竄氣回流,導致機組排氣溫度高。
(2)裝置加工高硫油,循環氫中H2S含量高,循環氫高濃度的H2S加速氣閥彈簧、閥片腐蝕斷裂。對氣閥進行拆檢發現進氣閥彈簧斷裂、閥體內積累較多雜質、閥片斷裂等,見圖1所示。
在裝置生產過程中對循環氫定期取樣分析,循環氫H2S含量在10000-15000ppm;通過取壓縮機氣閥上的垢樣,按照SH/T0656方法進行了碳、氫、氧含量分析。從分析結果及樣品性狀看,樣品中除碳氫外,非金屬元素中硫氮含量較高,分別為16.10%和5.02%,金屬元素中鐵含量較高,為14.6%。因此裝置存在有腐蝕及結焦現象。由于H2S含量高,具有腐蝕作用,尤其在停機后存在于冷卻后的濕氣中,其腐蝕性會大大增強。彈簧在經歷長時間高頻率的工作后會不斷積累疲勞斷裂的可能性,如果再有腐蝕,會加速彈簧疲勞斷裂。彈簧斷裂后閥片彈性緩沖力減弱,閥片傾側撞擊閥座閥蓋進一步造成閥片斷裂引起氣閥異響,對應的卸荷閥壓叉腳在卸荷的時候因為受力不均勻,也增加了斷裂的可能性。所以高濃度H2S腐蝕加速了彈簧斷裂。
(3)介質循環氫氣中夾帶液體組分。生產上循環氫氣雖然經過循環氫分液罐進行分離,但仍帶有少量較輕的液體組分,同時生產上的操作波動將會使液體組分進一步增加。從而使壓縮機吸入的氫氣帶液,對氣缸及氣閥產生液擊。機組在生產運行過程中帶液運行,形成液擊,極易造成氣閥閥片、彈簧、閥座損壞或斷裂,導致氣閥故障,同時因液體難壓縮,機組帶液運行存在嚴重的安全隱患。如圖2,因液擊造成氣閥閥座斷裂。
(4)循環氫中攜帶的催化劑粉塵較多。如圖3,催化劑粉塵會積聚在氣閥閥片、閥座上形成油泥、積碳,堵塞氣閥的流通面積,影響閥片的啟閉,閥片彈簧受力不均,長期處在較高的交變應力工況下工作,容易造成閥片、彈簧斷裂。
(5)頂開吸氣閥氣量凋節機構設計不合理,容易卡死。卸荷閥頂開裝置結構設計不合理,故障卡死,致使氣閥閥片在卸荷時不能完整頂開或加荷時氣閥閥片不能正常打開,導致氣閥工況不穩。
三、解決措施
針對循環氫壓縮機K-301A/B在生產運行期間存在的問題,在裝置停工檢修期間,我們采取以下改進解決措施。
(1)針對現工況循環氫含H2S高腐蝕的問題,對原來的氣閥進行重新設計,采用耐H2S腐蝕的PEEK氣閥,對氣閥(含閥片、閥座、彈簧)進行材質升級。閥片材質升級選用PEEK;氣閥彈簧材質選用17-7PH進口鋼絲;為了能使整套氣閥抵抗H2S腐蝕,對閥蓋、閥座、彈簧、墊片等部件采取表面非晶態處理措施,噴涂耐高溫的防腐涂層,如表3所示。圖4為改造后的氣閥。
(2)對負荷控制器進行重新核算、設計、改造,使氣閥工況穩定。如圖4所示,原卸荷閥壓叉腳小,與閥片接觸面積小,受力集中,不均勻,當氣閥上有積聚的雜物時,容易卡死。所以對壓叉進行重新設計。所以,增大了壓叉的接觸面積,選用耐硫腐蝕的材質。
(3)對機組帶液和粉塵問題,在循環氫分液罐增加絲網除沫氣,在壓縮機吸入管路上增加一臺旋風分離器。對循環氫中攜帶的少量液體、催化劑粉塵進行進一步分離,減少循環氫中的液體夾帶和催化劑粉塵,改善氣閥工況。同時打開進口過濾器檢查,更換損壞的過濾器濾芯,并選用耐H2S腐蝕的不銹鋼316。要定期檢查機組進口管線Y型過濾器濾芯濾網是否腐蝕脫落,過濾器是否堵塞,進行清理。
(5)控制好檢修質量,要嚴格按照《SHS 01020-2004 活塞式壓縮機維護檢修規程》進行檢修和驗收。采購時要嚴格把控好氣閥及彈簧的質量。對更換的備件要認真檢查驗收,閥片不得有變形、裂紋、劃痕等缺陷;閥座密封面不得有腐蝕麻點、氣孔及劃痕,表面粗糙度為Ra0.8,閥座邊緣不得有裂紋、溝槽等缺陷;閥座與閥片接觸線應連續封閉;對氣閥組裝后,用煤油進行氣密性試驗,對超標一律更換或返修。
(6)加強機組的管理。日常要加強機組的管理工作,做好機組的日常維護保養和定期維護保養工作,成立公司級的大型機組的特護工作,崗位操作人員要嚴格按照設備安全操作規程操作。
四、改造效果
通過實施以上改進措施,自改造后機組投入生產運行以來,機組故障率明顯降低,氣閥故障問題基本上得到了有效控制,取得了較好的改造效果,避免了大型機組發生故障可能造成的操作波動,目前該機組平穩運行,未出現氣閥異響故障。
五、結論
氣閥故障是往復活塞式壓縮機常見的故障之一,其產生的原因具有工藝工況方面的原因,也有設備及機組管理方面的原因。因此,本文通過對某柴油加氫改質裝置循環氫壓縮機在生產運行過程中,頻繁出現的氣閥故障進行分析,找出了氣閥頻繁故障的原因,提出有效的改進措施,解決了機組氣閥頻繁故障問題,取得了明顯的改造效果,為國內同類設備處理類似問題提供了借鑒和參考。同時在管理上,應該建立健全大型機組的特護管理組織機構,明確職責,加強分工,加強機組的管理工作。加強機組的日常維護保養和定期維護保養工作;機組要定時定點進行巡檢點檢工作,及時發現機組在運行過程中的隱患,確保機組的安全運行。崗位操作人員要嚴格按照設備安全操作規程進行操作,嚴禁違規操作。只有這樣堅持科學的管理,才能降低設備故障率,才能降低設備維修和管理成本,確保設備的安全運行,提高企業的經濟效益。
參考文獻
【2】中國石化集團上海工程有限公司.《化工工藝設計手冊(第四版)》.中國石化出版社.2009
【3】中國石油和石化工程研究會.《煉油設備工程師手冊(第二版)》.中國石化出版社.2009
【4】SHS 01020-2004 《活塞式壓縮機維護檢修規程》
【5】《循環氫壓縮機氣閥故障分析》孝有正 巴鵬
作者簡介
石芝鋒 ,男,本科學士,中級工程師,過程裝備與控制工程專業。在石油化工及燃氣行業從事設備專業技術管理工作近8年,現在煉廠加氫裝置從事設備專業技術管理工作,任設備主管和設備工程師。
一、循環氫壓縮機K-301A/B機組概況
【壓縮機網】1.1主要用途
在加氫精制裝置中,循環氫壓縮機主要用于克服生產裝置系統的阻力降,增加循環氫氣體的壓力,使得未充分參與反應的循環氫氣體物料,經循環氫壓縮機升壓后,重新進入反應系統。因此循環氫壓縮機K-301A/B,其作用是為石腦油加氫裝置反應系統輸送循環氫物料、給系統補氫增壓,把未充分參與反應的循環氫氣體物料,經循環氫壓縮機升壓后,重新送往反應系統中。
1.2主要結構簡述
石腦油加氫裝置循環氫壓縮機K-301A/B機組為固定水冷、一級、對稱平衡型無油潤滑往復活塞式壓縮機,由同步電動機、機身、氣缸曲柄軸、十字頭銷、十字體、活塞桿等零部件組成,由直接裝在主軸上的同步電動機驅動。
1.3主要技術性能
循環氫壓縮機K-301A/B組規格型號為DW-11/15-25,額度流量為11.0Nm3/min,額度吸氣壓力為1.5MPa,額度排氣壓力為2.5MPa,其作用為石腦油加氫裝置反應系統用的循環氫增壓循環,一備一用。該循環氫壓縮機機其詳細的技術性能如表1所示。
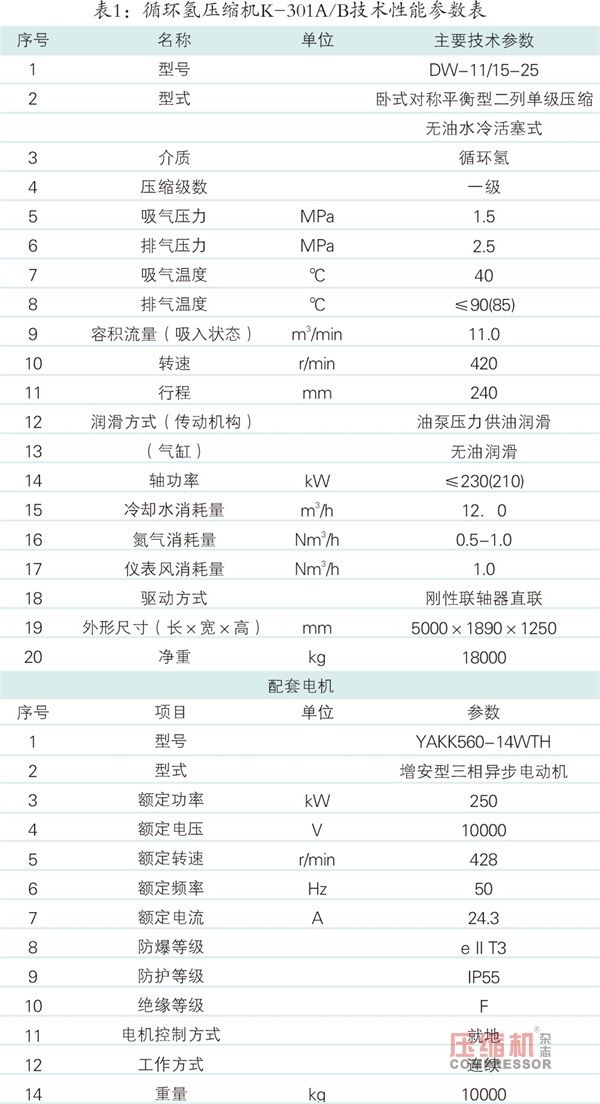
1.4 K-301A/B氣閥
氣閥是安裝在壓縮機氣缸上控制氣體進出的部件,分為進氣閥和排氣閥,是壓縮機中z*重要、z*易損壞的部件之一。因此壓縮機運行的經濟性和可靠性,很大程度上取決于氣閥的可靠完好,其壽命的長短,直接影響到壓縮機的運轉率。循環氫壓縮機K-301A/B氣閥為網狀閥,閥片采用了網狀結構,材質為3Cr13;閥座也是材質為3Cr13;氣閥彈簧材質為17—7PH。 一級進氣閥、一級排氣閥,對稱安裝布置。
二、氣閥故障及原因分析
2.1運行狀況及故障統計
汽油加氫改質裝置循環氫壓縮機K-301A/B為反應系統用的循環氫增壓循環,共設2臺,一開一備,設計參數見表2。
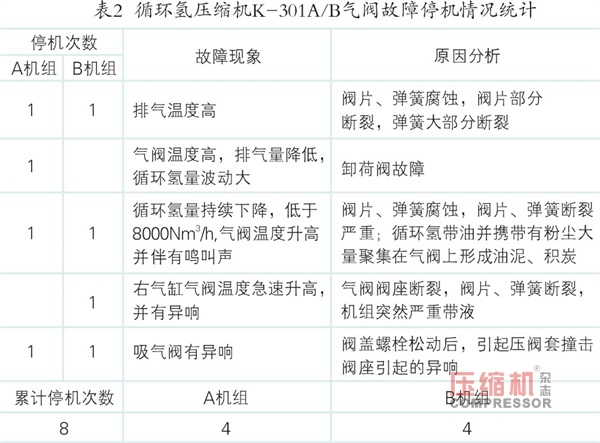
K401自2010年9月26日投運,初期試運行總時間404.76h的過程中,多次出現故障停車。具體情況為:開車運行13次,有8次因二段出口溫度高跳車(由現場的檢查和修理情況確定由氣閥引起),4次因氣閥問題停運,1次因刮油環漏油檢修。因氣閥引起的故障停車時間占整個停車時間的90%以上。
該機組自2017年8月25日投運以來,機組多次發生故障停車。其中因氣閥引起的故障停車時間占整個停車時間的80%以上計初步統計,2017年8月25日至2018年2月15日以來,機組因氣閥故障停車維修頻次達到8次,如表2所示。氣閥故障率高,頻繁發生故障,導致機組切換和維修頻次高,操作人員和檢維修人員勞動強度大,嚴重影響裝置的長周期、安全平穩運行。
從表2分析可以看出,在這個周期(6個月)的裝置生產過程中,循環氫壓縮機共發生故障8次,造成2臺機組頻繁切換運行。根據現場檢修情況和對氣閥拆檢情況分析,發現機組氣閥故障主要集中在以下幾個問題:
(1)氣閥內漏;
(2)氣閥部件閥片、彈簧腐蝕斷裂;
(3)機組帶液,氣閥閥座斷裂;
(4)機組催化劑粉塵多,在氣閥上積聚油泥、積碳;
(5)頂開吸氣閥氣量凋節機構卸荷閥設計不合理,容易卡死。
2.2 氣閥故障原因分析
從檢修的情況看,氣閥故障主要表現氣閥泄漏;氣閥閥片、彈簧大量斷裂;閥座上堆積催化劑粉塵、油泥、積碳較多,閥座液擊斷裂。同時機組帶液,粉塵大。從而導致機組在生產運行過程中出現排氣溫度高,排氣量降低,氣閥或氣缸異響等故障現象。因此,根據檢修的情況分析,結合機組實際的運行工況判斷,造成循環氫壓縮機K-301A/B氣閥故障原因主要有以下幾個方面:
(1)氣閥閥片、閥座密封面磨損,閥片、閥座上形成油泥、積碳等雜質,彈簧疲勞斷裂或受力不均勻,導致氣閥內漏,循環氫竄氣回流,導致機組排氣溫度高。
(2)裝置加工高硫油,循環氫中H2S含量高,循環氫高濃度的H2S加速氣閥彈簧、閥片腐蝕斷裂。對氣閥進行拆檢發現進氣閥彈簧斷裂、閥體內積累較多雜質、閥片斷裂等,見圖1所示。

在裝置生產過程中對循環氫定期取樣分析,循環氫H2S含量在10000-15000ppm;通過取壓縮機氣閥上的垢樣,按照SH/T0656方法進行了碳、氫、氧含量分析。從分析結果及樣品性狀看,樣品中除碳氫外,非金屬元素中硫氮含量較高,分別為16.10%和5.02%,金屬元素中鐵含量較高,為14.6%。因此裝置存在有腐蝕及結焦現象。由于H2S含量高,具有腐蝕作用,尤其在停機后存在于冷卻后的濕氣中,其腐蝕性會大大增強。彈簧在經歷長時間高頻率的工作后會不斷積累疲勞斷裂的可能性,如果再有腐蝕,會加速彈簧疲勞斷裂。彈簧斷裂后閥片彈性緩沖力減弱,閥片傾側撞擊閥座閥蓋進一步造成閥片斷裂引起氣閥異響,對應的卸荷閥壓叉腳在卸荷的時候因為受力不均勻,也增加了斷裂的可能性。所以高濃度H2S腐蝕加速了彈簧斷裂。
(3)介質循環氫氣中夾帶液體組分。生產上循環氫氣雖然經過循環氫分液罐進行分離,但仍帶有少量較輕的液體組分,同時生產上的操作波動將會使液體組分進一步增加。從而使壓縮機吸入的氫氣帶液,對氣缸及氣閥產生液擊。機組在生產運行過程中帶液運行,形成液擊,極易造成氣閥閥片、彈簧、閥座損壞或斷裂,導致氣閥故障,同時因液體難壓縮,機組帶液運行存在嚴重的安全隱患。如圖2,因液擊造成氣閥閥座斷裂。

(4)循環氫中攜帶的催化劑粉塵較多。如圖3,催化劑粉塵會積聚在氣閥閥片、閥座上形成油泥、積碳,堵塞氣閥的流通面積,影響閥片的啟閉,閥片彈簧受力不均,長期處在較高的交變應力工況下工作,容易造成閥片、彈簧斷裂。

(5)頂開吸氣閥氣量凋節機構設計不合理,容易卡死。卸荷閥頂開裝置結構設計不合理,故障卡死,致使氣閥閥片在卸荷時不能完整頂開或加荷時氣閥閥片不能正常打開,導致氣閥工況不穩。
三、解決措施
針對循環氫壓縮機K-301A/B在生產運行期間存在的問題,在裝置停工檢修期間,我們采取以下改進解決措施。
(1)針對現工況循環氫含H2S高腐蝕的問題,對原來的氣閥進行重新設計,采用耐H2S腐蝕的PEEK氣閥,對氣閥(含閥片、閥座、彈簧)進行材質升級。閥片材質升級選用PEEK;氣閥彈簧材質選用17-7PH進口鋼絲;為了能使整套氣閥抵抗H2S腐蝕,對閥蓋、閥座、彈簧、墊片等部件采取表面非晶態處理措施,噴涂耐高溫的防腐涂層,如表3所示。圖4為改造后的氣閥。

(2)對負荷控制器進行重新核算、設計、改造,使氣閥工況穩定。如圖4所示,原卸荷閥壓叉腳小,與閥片接觸面積小,受力集中,不均勻,當氣閥上有積聚的雜物時,容易卡死。所以對壓叉進行重新設計。所以,增大了壓叉的接觸面積,選用耐硫腐蝕的材質。

(3)對機組帶液和粉塵問題,在循環氫分液罐增加絲網除沫氣,在壓縮機吸入管路上增加一臺旋風分離器。對循環氫中攜帶的少量液體、催化劑粉塵進行進一步分離,減少循環氫中的液體夾帶和催化劑粉塵,改善氣閥工況。同時打開進口過濾器檢查,更換損壞的過濾器濾芯,并選用耐H2S腐蝕的不銹鋼316。要定期檢查機組進口管線Y型過濾器濾芯濾網是否腐蝕脫落,過濾器是否堵塞,進行清理。
(5)控制好檢修質量,要嚴格按照《SHS 01020-2004 活塞式壓縮機維護檢修規程》進行檢修和驗收。采購時要嚴格把控好氣閥及彈簧的質量。對更換的備件要認真檢查驗收,閥片不得有變形、裂紋、劃痕等缺陷;閥座密封面不得有腐蝕麻點、氣孔及劃痕,表面粗糙度為Ra0.8,閥座邊緣不得有裂紋、溝槽等缺陷;閥座與閥片接觸線應連續封閉;對氣閥組裝后,用煤油進行氣密性試驗,對超標一律更換或返修。
(6)加強機組的管理。日常要加強機組的管理工作,做好機組的日常維護保養和定期維護保養工作,成立公司級的大型機組的特護工作,崗位操作人員要嚴格按照設備安全操作規程操作。
四、改造效果
通過實施以上改進措施,自改造后機組投入生產運行以來,機組故障率明顯降低,氣閥故障問題基本上得到了有效控制,取得了較好的改造效果,避免了大型機組發生故障可能造成的操作波動,目前該機組平穩運行,未出現氣閥異響故障。
五、結論
氣閥故障是往復活塞式壓縮機常見的故障之一,其產生的原因具有工藝工況方面的原因,也有設備及機組管理方面的原因。因此,本文通過對某柴油加氫改質裝置循環氫壓縮機在生產運行過程中,頻繁出現的氣閥故障進行分析,找出了氣閥頻繁故障的原因,提出有效的改進措施,解決了機組氣閥頻繁故障問題,取得了明顯的改造效果,為國內同類設備處理類似問題提供了借鑒和參考。同時在管理上,應該建立健全大型機組的特護管理組織機構,明確職責,加強分工,加強機組的管理工作。加強機組的日常維護保養和定期維護保養工作;機組要定時定點進行巡檢點檢工作,及時發現機組在運行過程中的隱患,確保機組的安全運行。崗位操作人員要嚴格按照設備安全操作規程進行操作,嚴禁違規操作。只有這樣堅持科學的管理,才能降低設備故障率,才能降低設備維修和管理成本,確保設備的安全運行,提高企業的經濟效益。
參考文獻
【2】中國石化集團上海工程有限公司.《化工工藝設計手冊(第四版)》.中國石化出版社.2009
【3】中國石油和石化工程研究會.《煉油設備工程師手冊(第二版)》.中國石化出版社.2009
【4】SHS 01020-2004 《活塞式壓縮機維護檢修規程》
【5】《循環氫壓縮機氣閥故障分析》孝有正 巴鵬
作者簡介
石芝鋒 ,男,本科學士,中級工程師,過程裝備與控制工程專業。在石油化工及燃氣行業從事設備專業技術管理工作近8年,現在煉廠加氫裝置從事設備專業技術管理工作,任設備主管和設備工程師。
網友評論
條評論
最新評論