【壓縮機網(wǎng)】1、前言
盡管對往復(fù)壓縮機組的扭振分析,目前已有成熟的技術(shù),但實際工程應(yīng)用中,不乏看到往復(fù)式壓縮機組發(fā)生扭振事故。究其原因,各有不同。但通過對這些事故的深入分析,不難發(fā)現(xiàn)在壓縮機成撬設(shè)計過程中,如使用時、頻域相結(jié)合的扭振分析方法,可大大降低扭振事故發(fā)生的幾率。
目前,對壓縮機成撬設(shè)計過程中的扭振分析,大多是采用單一的時域響應(yīng)分析或頻域響應(yīng)分析方法。這對一般情況下壓縮機組的成撬設(shè)計是適用的,但對某些特殊情況下機組的設(shè)計略顯不足,留下了機組發(fā)生扭振事故的隱患。針對此實際情況,我們提出了采用時、頻域相結(jié)合的方法進行扭振分析的技術(shù)。其中頻域分析方法主要用來確定機組的臨界轉(zhuǎn)速即共振頻率,以及檢查機組在運行工況下的轉(zhuǎn)速是否有足夠的空間遠離前后的共振轉(zhuǎn)速。時域分析方法則通過直接使用廠家提供的壓縮機、驅(qū)動器及聯(lián)軸器上的阻尼等值,達到準(zhǔn)確計算機組的扭振動態(tài)響應(yīng)(即壓縮機、驅(qū)動器及聯(lián)軸器上瞬時角速度、角變形和動態(tài)扭矩等)的目的。時域分析方法特別適用于變頻機組等無法避開扭振共振轉(zhuǎn)速時的情況。本文以某臨海陸上終端處理廠增壓壓縮機組的扭振事故分析和機組整改為例,說明了應(yīng)用時、頻域相結(jié)合的扭振分析技術(shù)的過程和效果。
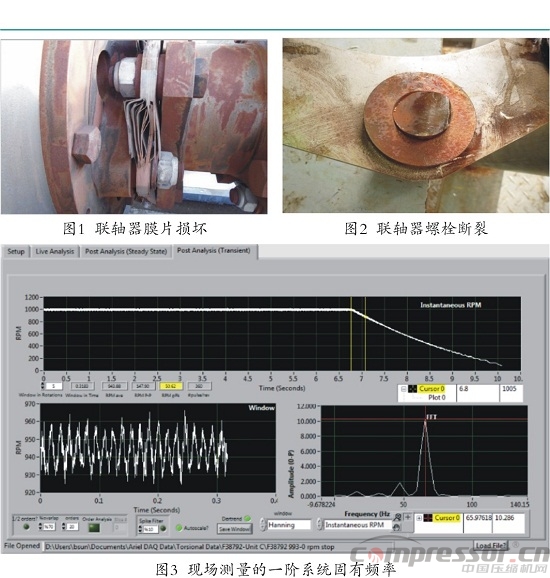
2、壓縮機組扭振事故概述
某臨海氣田陸上終端處理廠三臺增壓壓縮機組在運行大約2000小時后,發(fā)現(xiàn)聯(lián)軸器膜片損壞和螺栓斷裂,如圖1和圖2所示。
該機組壓縮機的主要技術(shù)參數(shù)如下:
型式:臥式單列二級雙作用
功率:1120kW
排量:29.360.7萬方/天(天然氣)
進氣壓力:1.5 2.0MPa
排氣壓力:4.5 5.6MPa
氣缸直徑:一級Φ375mm;二級Φ263.5mm
活塞行程:165.1mm
壓縮機轉(zhuǎn)速:993轉(zhuǎn)/分
該機組共有11個運行工況。
通過對機組進行現(xiàn)場扭振測量和分析,發(fā)現(xiàn)該機組系統(tǒng)的一階固有頻率與運行轉(zhuǎn)速的四倍頻重合,引起機組發(fā)生共振,如圖3所示。這是導(dǎo)致扭振事故發(fā)生的主要原因。
3、事故機組的扭振分析
s*先對機組建立扭振分析模型。該模型由電動機、聯(lián)軸器和壓縮機組成,分別由12個具有轉(zhuǎn)動慣量的轉(zhuǎn)盤(每個轉(zhuǎn)盤代表一個集中質(zhì)量塊)和11個具有彈性的扭轉(zhuǎn)彈簧所代表,如圖4所示。其中電動機由5個轉(zhuǎn)盤構(gòu)成,由“FRT”到“MN0”來標(biāo)示。聯(lián)軸器由2部分構(gòu)成,由“CP1”和“CP2”標(biāo)示。其中CP1部分還包括電動機軸前端部分的轉(zhuǎn)動慣量,CP2部分還包括飛輪的轉(zhuǎn)動慣量和壓縮機軸前端部分的轉(zhuǎn)動慣量。兩者之間由代表聯(lián)軸器扭轉(zhuǎn)剛度的等效彈簧連接。壓縮機部分由5個轉(zhuǎn)盤構(gòu)成,分別標(biāo)示為“MN1”到“AUX”。
使用頻域分析方法計算得到機組的前3階扭振固有頻率分別為65.8Hz,156.7Hz和215.4Hz。機組的前三階固有振型如圖5所示,相應(yīng)的Campbell圖如圖6所示。從圖6中可以看到系統(tǒng)的第一階固有頻率與機組運行轉(zhuǎn)速的4倍頻(4X)在運行轉(zhuǎn)速987rpm處發(fā)生相交,如圖中紅點所示。該共振轉(zhuǎn)速與機組的運行轉(zhuǎn)速993rpm非常接近,引起機組發(fā)生共振。這與圖3所示的實測結(jié)果完全吻合。
圖7和圖8顯示了使用頻域分析方法得到的機組諧振分析結(jié)果圖,圖7顯示了機組在共振轉(zhuǎn)速處的交變扭矩峰值。圖8顯示了該扭振共振響應(yīng)主要來自4倍頻諧振分量的貢獻。
考慮到通過頻域動態(tài)分析方法得到的交變扭矩值受使用的阻尼假設(shè)值影響較大,故對該機組使用時域強迫振動分析方法精確計算聯(lián)軸器上的動態(tài)扭矩。時域強迫振動分析方法是對電機軸施加驅(qū)動扭矩,和對壓縮機軸施加負載扭矩,并考慮阻尼及相位等參數(shù)影響,計算聯(lián)軸器、壓縮機和電機軸上的瞬時角速度、角變形和動態(tài)扭矩。是一種精確的力響應(yīng)分析方法。時域強迫振動分析能夠模擬機組自起動到穩(wěn)定運行狀態(tài)的全過程,當(dāng)電機驅(qū)動功率與壓縮機所需功率達到平衡時,系統(tǒng)進入穩(wěn)定運行狀態(tài)。圖9顯示了機組在z*不利運行工況(工況7,進壓1.75MPa,排壓5.0MPa)下,使用時域強迫振動分析方法計算得到的機組從開始到穩(wěn)定運行狀態(tài)下作用在聯(lián)軸器上的交變扭矩值。從圖中可以看出,作用在聯(lián)軸器上的z*小扭矩顯著超出了聯(lián)軸器的z*小扭矩允許值-26 kNm,從而引起聯(lián)軸器破壞。
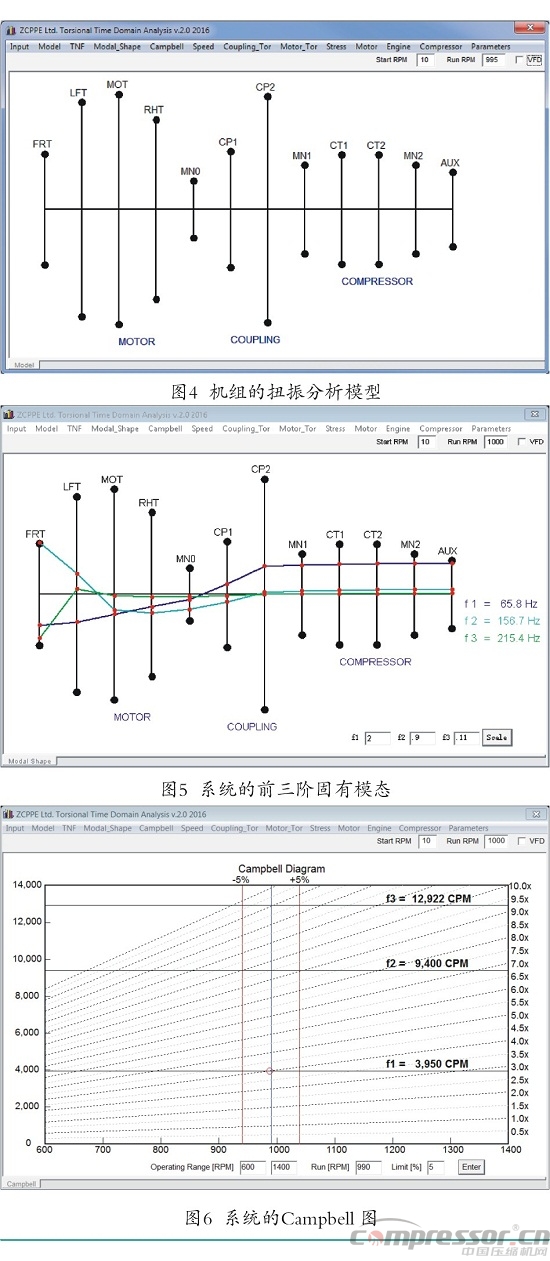
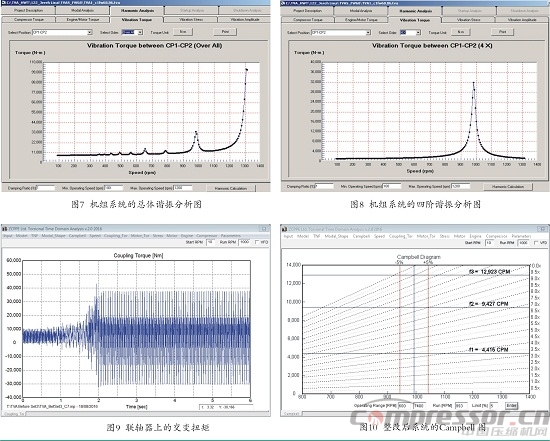
4、整改后機組的扭振分析
對事故機組的扭振分析和現(xiàn)場測試結(jié)果表明,需要調(diào)整該機組的扭振控制方案,以避免4倍頻上的共振。考慮到調(diào)整飛輪是一個簡單而有效的避開機組共振的方法,提出將飛輪轉(zhuǎn)動慣量由原68.86kg·m2減少到43kg·m2。
通過頻域分析方法,計算得到調(diào)整飛輪后機組的前3階扭轉(zhuǎn)固有頻率分別為73.6Hz,157.2Hz和215.4Hz。相應(yīng)的系統(tǒng)Campbell圖如圖10所示。此時,機組第一階系統(tǒng)扭振固有頻率是運行轉(zhuǎn)速993rpm的4.45倍。在運行轉(zhuǎn)速993rpm的正負5%范圍內(nèi)(即943rpm~1043rpm內(nèi)),沒有共振點。機組運行時不會產(chǎn)生共振。
圖11顯示了使用頻域動態(tài)分析方法計算得到的機組諧振分析結(jié)果圖。從圖中可以發(fā)現(xiàn)機組工況運行轉(zhuǎn)速993rpm離其前、后共振點都較遠,不易發(fā)生共振。圖12顯示了通過使用時域分析方法重新對z*不利運行工況7計算得到的聯(lián)軸器上的交變扭矩值。可以看到,與調(diào)整飛輪前相比,交變扭矩幅值下降了很多,其z*大和z*小值均在聯(lián)軸器的允許值范圍之內(nèi)。
現(xiàn)場測試結(jié)果表明(如圖13所示),機組調(diào)整飛輪后實測兩臺機組的平均第一階固有頻率為74Hz。與分析結(jié)果完全吻合。機組整改后運行情況良好,再沒有發(fā)現(xiàn)扭振故障。
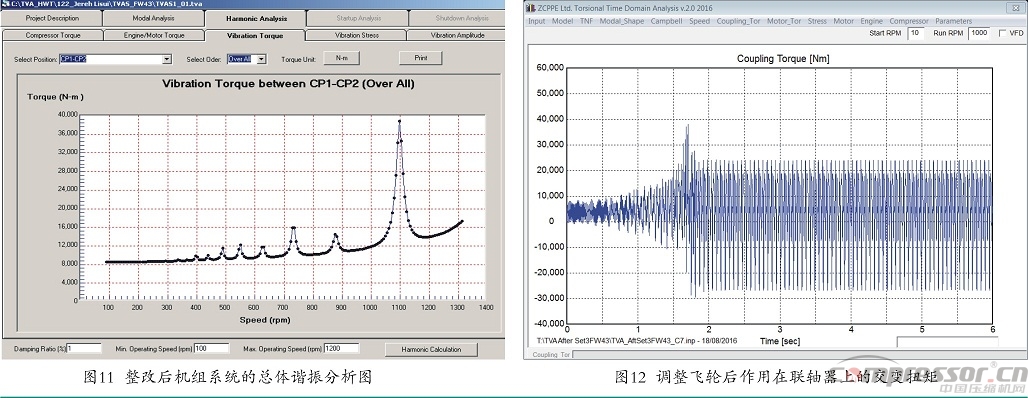
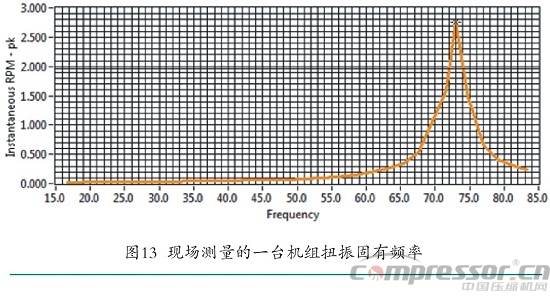
5、使用時、頻域分析方法討論z*佳扭振控制調(diào)整方案
(1)于機組飛輪轉(zhuǎn)動慣量的選擇
扭振分析整改建議推薦新的飛輪轉(zhuǎn)動慣量為43kg·m2。如果僅從避開共振點這個角度來考慮,也可選擇飛輪轉(zhuǎn)動慣量為92.18kg·m2或16kg·m2。如果考慮飛輪轉(zhuǎn)動慣量為92.18kg·m2,計算得到機組的第一階系統(tǒng)扭振固有頻率為61.7Hz,是運行轉(zhuǎn)速993rpm的3.7倍。圖14表示了連軸器在z*大功率工況下的交變扭矩。機組運行轉(zhuǎn)速993rpm離第一階扭振固有頻率和4倍頻(4X)共振點遠,不會發(fā)生共振。但是因為壓縮機在起動過程中要經(jīng)過4 倍頻共振點,時域分析表明機組在此共振點處的動態(tài)響應(yīng)較大,故不推薦此方案。
如果考慮飛輪轉(zhuǎn)動慣量為16kg·m2 ,此時計算得到的第一階系統(tǒng)扭振固有頻率為91.2Hz,是運行轉(zhuǎn)速993rpm的5.5倍。圖15為連軸器在z*大功率工況下的交變扭矩。機組運行轉(zhuǎn)速993rpm遠離共振點,不會發(fā)生共振。時域分析表明機組動態(tài)響應(yīng)也在允許范圍之內(nèi)。所以,使用轉(zhuǎn)動慣量為16kg·m2 的飛輪也是一個可行的方案。但考慮到16kg·m2 飛輪的幾何尺寸與原飛輪尺寸相差太大,可能導(dǎo)致機組在配置尺寸變更上的困難,因此也沒有采用。
(2)關(guān)于扭振分析模型參數(shù)變化的影響
在實際工程中,不能保證廠家提供的扭振分析參數(shù)與實際參數(shù)完全一致。此時使用頻域分析方法通過觀察工況運行點與前后共振點的距離,可有效避免由此誤差帶來的扭振問題。
對該機組,考慮到廠家提供的數(shù)據(jù)與現(xiàn)場測量結(jié)果反算得到的數(shù)據(jù)誤差,如假設(shè)聯(lián)軸器剛度下降21%,其它參數(shù)不變,使用頻域分析方法得到結(jié)果如圖16所示。此時第一階系統(tǒng)扭振固有頻率與4X共振點還差65rpm。如假設(shè)電機轉(zhuǎn)動慣量增加22%,其它參數(shù)不變,使用頻域分析方法得到結(jié)果如圖17所示。此時第一階系統(tǒng)扭振固有頻率與4X共振點還差60rpm。這就說明即使扭振分析參數(shù)有如此大誤差,推薦的扭振控制調(diào)整方案還有一定的轉(zhuǎn)速安全余量。
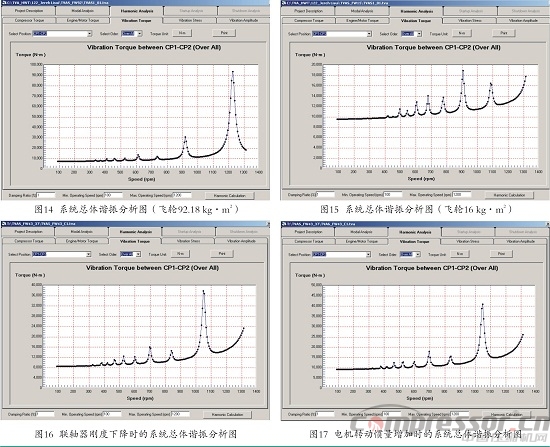
6、結(jié)論
從上面的分析可以看出:
(1)使用時、頻域相結(jié)合的扭振分析方法進行往復(fù)式壓縮機成撬時的扭振控制設(shè)計,可以充分發(fā)揮各自方法的長處,并對各自的不足進行互補,以z*大程度地避免機組扭振事故的發(fā)生。
(2) 采用時、頻域相結(jié)合的扭振分析方法整改后的機組運行正常,這為使用該方法有效整改現(xiàn)場機組的扭振事故提供了良好案例。
作者簡介
盧福志,博士,注冊工程師,加拿大中加壓縮機撬及管道工程公司
汪華良,碩士,注冊工程師,加拿大中加壓縮機撬及管道工程公司
徐宜桂,博士,注冊工程師,加拿大中加壓縮機撬及管道工程公司
http://www.zcppe.com E-mail: jason.xu@zcppe.com
參考文獻
1. P. Alves, M. Forcinito, J. Xu(徐宜桂), M. Ferguson, Analysis of Threaded Connection Reliability for Compression Application, J. Canadian Petroleum Tech., V49, No. 6, 2010, pp. 8-12
2.API Standard 618-5th ed., Washington: American Petroleum Institute, 2007.
3.API Standard 684-2nd ed., API Standard Paragraphs RotordynamicTutorial: Lateral Critical Speeds, Unbalance Response, Stability, Train Torsionals,And Rotor Balancing,2005/R2010
4.Nestorides, E.J., A Handbook on Torsional Vibration, Cambridge at the University Press, 1958
5.R.C. Juvinall and K.M Marshek, Fundamentals of Machine Component Design, 2nd ed, John Wiley and Sons.
【壓縮機網(wǎng)】1、前言
盡管對往復(fù)壓縮機組的扭振分析,目前已有成熟的技術(shù),但實際工程應(yīng)用中,不乏看到往復(fù)式壓縮機組發(fā)生扭振事故。究其原因,各有不同。但通過對這些事故的深入分析,不難發(fā)現(xiàn)在壓縮機成撬設(shè)計過程中,如使用時、頻域相結(jié)合的扭振分析方法,可大大降低扭振事故發(fā)生的幾率。
目前,對壓縮機成撬設(shè)計過程中的扭振分析,大多是采用單一的時域響應(yīng)分析或頻域響應(yīng)分析方法。這對一般情況下壓縮機組的成撬設(shè)計是適用的,但對某些特殊情況下機組的設(shè)計略顯不足,留下了機組發(fā)生扭振事故的隱患。針對此實際情況,我們提出了采用時、頻域相結(jié)合的方法進行扭振分析的技術(shù)。其中頻域分析方法主要用來確定機組的臨界轉(zhuǎn)速即共振頻率,以及檢查機組在運行工況下的轉(zhuǎn)速是否有足夠的空間遠離前后的共振轉(zhuǎn)速。時域分析方法則通過直接使用廠家提供的壓縮機、驅(qū)動器及聯(lián)軸器上的阻尼等值,達到準(zhǔn)確計算機組的扭振動態(tài)響應(yīng)(即壓縮機、驅(qū)動器及聯(lián)軸器上瞬時角速度、角變形和動態(tài)扭矩等)的目的。時域分析方法特別適用于變頻機組等無法避開扭振共振轉(zhuǎn)速時的情況。本文以某臨海陸上終端處理廠增壓壓縮機組的扭振事故分析和機組整改為例,說明了應(yīng)用時、頻域相結(jié)合的扭振分析技術(shù)的過程和效果。
2、壓縮機組扭振事故概述
某臨海氣田陸上終端處理廠三臺增壓壓縮機組在運行大約2000小時后,發(fā)現(xiàn)聯(lián)軸器膜片損壞和螺栓斷裂,如圖1和圖2所示。
該機組壓縮機的主要技術(shù)參數(shù)如下:
型式:臥式單列二級雙作用
功率:1120kW
排量:29.360.7萬方/天(天然氣)
進氣壓力:1.5 2.0MPa
排氣壓力:4.5 5.6MPa
氣缸直徑:一級Φ375mm;二級Φ263.5mm
活塞行程:165.1mm
壓縮機轉(zhuǎn)速:993轉(zhuǎn)/分
該機組共有11個運行工況。
通過對機組進行現(xiàn)場扭振測量和分析,發(fā)現(xiàn)該機組系統(tǒng)的一階固有頻率與運行轉(zhuǎn)速的四倍頻重合,引起機組發(fā)生共振,如圖3所示。這是導(dǎo)致扭振事故發(fā)生的主要原因。
3、事故機組的扭振分析
s*先對機組建立扭振分析模型。該模型由電動機、聯(lián)軸器和壓縮機組成,分別由12個具有轉(zhuǎn)動慣量的轉(zhuǎn)盤(每個轉(zhuǎn)盤代表一個集中質(zhì)量塊)和11個具有彈性的扭轉(zhuǎn)彈簧所代表,如圖4所示。其中電動機由5個轉(zhuǎn)盤構(gòu)成,由“FRT”到“MN0”來標(biāo)示。聯(lián)軸器由2部分構(gòu)成,由“CP1”和“CP2”標(biāo)示。其中CP1部分還包括電動機軸前端部分的轉(zhuǎn)動慣量,CP2部分還包括飛輪的轉(zhuǎn)動慣量和壓縮機軸前端部分的轉(zhuǎn)動慣量。兩者之間由代表聯(lián)軸器扭轉(zhuǎn)剛度的等效彈簧連接。壓縮機部分由5個轉(zhuǎn)盤構(gòu)成,分別標(biāo)示為“MN1”到“AUX”。
使用頻域分析方法計算得到機組的前3階扭振固有頻率分別為65.8Hz,156.7Hz和215.4Hz。機組的前三階固有振型如圖5所示,相應(yīng)的Campbell圖如圖6所示。從圖6中可以看到系統(tǒng)的第一階固有頻率與機組運行轉(zhuǎn)速的4倍頻(4X)在運行轉(zhuǎn)速987rpm處發(fā)生相交,如圖中紅點所示。該共振轉(zhuǎn)速與機組的運行轉(zhuǎn)速993rpm非常接近,引起機組發(fā)生共振。這與圖3所示的實測結(jié)果完全吻合。
圖7和圖8顯示了使用頻域分析方法得到的機組諧振分析結(jié)果圖,圖7顯示了機組在共振轉(zhuǎn)速處的交變扭矩峰值。圖8顯示了該扭振共振響應(yīng)主要來自4倍頻諧振分量的貢獻。
考慮到通過頻域動態(tài)分析方法得到的交變扭矩值受使用的阻尼假設(shè)值影響較大,故對該機組使用時域強迫振動分析方法精確計算聯(lián)軸器上的動態(tài)扭矩。時域強迫振動分析方法是對電機軸施加驅(qū)動扭矩,和對壓縮機軸施加負載扭矩,并考慮阻尼及相位等參數(shù)影響,計算聯(lián)軸器、壓縮機和電機軸上的瞬時角速度、角變形和動態(tài)扭矩。是一種精確的力響應(yīng)分析方法。時域強迫振動分析能夠模擬機組自起動到穩(wěn)定運行狀態(tài)的全過程,當(dāng)電機驅(qū)動功率與壓縮機所需功率達到平衡時,系統(tǒng)進入穩(wěn)定運行狀態(tài)。圖9顯示了機組在z*不利運行工況(工況7,進壓1.75MPa,排壓5.0MPa)下,使用時域強迫振動分析方法計算得到的機組從開始到穩(wěn)定運行狀態(tài)下作用在聯(lián)軸器上的交變扭矩值。從圖中可以看出,作用在聯(lián)軸器上的z*小扭矩顯著超出了聯(lián)軸器的z*小扭矩允許值-26 kNm,從而引起聯(lián)軸器破壞。
4、整改后機組的扭振分析
對事故機組的扭振分析和現(xiàn)場測試結(jié)果表明,需要調(diào)整該機組的扭振控制方案,以避免4倍頻上的共振。考慮到調(diào)整飛輪是一個簡單而有效的避開機組共振的方法,提出將飛輪轉(zhuǎn)動慣量由原68.86kg·m2減少到43kg·m2。
通過頻域分析方法,計算得到調(diào)整飛輪后機組的前3階扭轉(zhuǎn)固有頻率分別為73.6Hz,157.2Hz和215.4Hz。相應(yīng)的系統(tǒng)Campbell圖如圖10所示。此時,機組第一階系統(tǒng)扭振固有頻率是運行轉(zhuǎn)速993rpm的4.45倍。在運行轉(zhuǎn)速993rpm的正負5%范圍內(nèi)(即943rpm~1043rpm內(nèi)),沒有共振點。機組運行時不會產(chǎn)生共振。
圖11顯示了使用頻域動態(tài)分析方法計算得到的機組諧振分析結(jié)果圖。從圖中可以發(fā)現(xiàn)機組工況運行轉(zhuǎn)速993rpm離其前、后共振點都較遠,不易發(fā)生共振。圖12顯示了通過使用時域分析方法重新對z*不利運行工況7計算得到的聯(lián)軸器上的交變扭矩值。可以看到,與調(diào)整飛輪前相比,交變扭矩幅值下降了很多,其z*大和z*小值均在聯(lián)軸器的允許值范圍之內(nèi)。
現(xiàn)場測試結(jié)果表明(如圖13所示),機組調(diào)整飛輪后實測兩臺機組的平均第一階固有頻率為74Hz。與分析結(jié)果完全吻合。機組整改后運行情況良好,再沒有發(fā)現(xiàn)扭振故障。
5、使用時、頻域分析方法討論z*佳扭振控制調(diào)整方案
(1)于機組飛輪轉(zhuǎn)動慣量的選擇
扭振分析整改建議推薦新的飛輪轉(zhuǎn)動慣量為43kg·m2。如果僅從避開共振點這個角度來考慮,也可選擇飛輪轉(zhuǎn)動慣量為92.18kg·m2或16kg·m2。如果考慮飛輪轉(zhuǎn)動慣量為92.18kg·m2,計算得到機組的第一階系統(tǒng)扭振固有頻率為61.7Hz,是運行轉(zhuǎn)速993rpm的3.7倍。圖14表示了連軸器在z*大功率工況下的交變扭矩。機組運行轉(zhuǎn)速993rpm離第一階扭振固有頻率和4倍頻(4X)共振點遠,不會發(fā)生共振。但是因為壓縮機在起動過程中要經(jīng)過4 倍頻共振點,時域分析表明機組在此共振點處的動態(tài)響應(yīng)較大,故不推薦此方案。
如果考慮飛輪轉(zhuǎn)動慣量為16kg·m2 ,此時計算得到的第一階系統(tǒng)扭振固有頻率為91.2Hz,是運行轉(zhuǎn)速993rpm的5.5倍。圖15為連軸器在z*大功率工況下的交變扭矩。機組運行轉(zhuǎn)速993rpm遠離共振點,不會發(fā)生共振。時域分析表明機組動態(tài)響應(yīng)也在允許范圍之內(nèi)。所以,使用轉(zhuǎn)動慣量為16kg·m2 的飛輪也是一個可行的方案。但考慮到16kg·m2 飛輪的幾何尺寸與原飛輪尺寸相差太大,可能導(dǎo)致機組在配置尺寸變更上的困難,因此也沒有采用。
(2)關(guān)于扭振分析模型參數(shù)變化的影響
在實際工程中,不能保證廠家提供的扭振分析參數(shù)與實際參數(shù)完全一致。此時使用頻域分析方法通過觀察工況運行點與前后共振點的距離,可有效避免由此誤差帶來的扭振問題。
對該機組,考慮到廠家提供的數(shù)據(jù)與現(xiàn)場測量結(jié)果反算得到的數(shù)據(jù)誤差,如假設(shè)聯(lián)軸器剛度下降21%,其它參數(shù)不變,使用頻域分析方法得到結(jié)果如圖16所示。此時第一階系統(tǒng)扭振固有頻率與4X共振點還差65rpm。如假設(shè)電機轉(zhuǎn)動慣量增加22%,其它參數(shù)不變,使用頻域分析方法得到結(jié)果如圖17所示。此時第一階系統(tǒng)扭振固有頻率與4X共振點還差60rpm。這就說明即使扭振分析參數(shù)有如此大誤差,推薦的扭振控制調(diào)整方案還有一定的轉(zhuǎn)速安全余量。
6、結(jié)論
從上面的分析可以看出:
(1)使用時、頻域相結(jié)合的扭振分析方法進行往復(fù)式壓縮機成撬時的扭振控制設(shè)計,可以充分發(fā)揮各自方法的長處,并對各自的不足進行互補,以z*大程度地避免機組扭振事故的發(fā)生。
(2) 采用時、頻域相結(jié)合的扭振分析方法整改后的機組運行正常,這為使用該方法有效整改現(xiàn)場機組的扭振事故提供了良好案例。
作者簡介
盧福志,博士,注冊工程師,加拿大中加壓縮機撬及管道工程公司
汪華良,碩士,注冊工程師,加拿大中加壓縮機撬及管道工程公司
徐宜桂,博士,注冊工程師,加拿大中加壓縮機撬及管道工程公司
http://www.zcppe.com E-mail: jason.xu@zcppe.com
參考文獻
1. P. Alves, M. Forcinito, J. Xu(徐宜桂), M. Ferguson, Analysis of Threaded Connection Reliability for Compression Application, J. Canadian Petroleum Tech., V49, No. 6, 2010, pp. 8-12
2.API Standard 618-5th ed., Washington: American Petroleum Institute, 2007.
3.API Standard 684-2nd ed., API Standard Paragraphs RotordynamicTutorial: Lateral Critical Speeds, Unbalance Response, Stability, Train Torsionals,And Rotor Balancing,2005/R2010
4.Nestorides, E.J., A Handbook on Torsional Vibration, Cambridge at the University Press, 1958
5.R.C. Juvinall and K.M Marshek, Fundamentals of Machine Component Design, 2nd ed, John Wiley and Sons.
網(wǎng)友評論
條評論
最新評論