【壓縮機網】1 項目概況
1.1 項目研究目標與難點
打破國外技術壁壘,掌握一批具有自主知識產權、達到國際同等水平的壓縮機設計、制造技術,實現25MPa高壓儲氣庫壓縮機的國產化,實現“零”的突破,提升儲氣庫壓縮機設計研發能力,為我國儲氣庫工程建設提供質優價廉、安全可靠的國產壓縮機,為我國儲氣庫工程建設提供大型、關鍵的國產化裝備保障,為國民經濟發展作出貢獻。
項目研發面臨四大難題:
儲氣庫壓縮機寬工況設計;高壓氣缸設計及密封問題;高壓氣缸套磨損控制;長薄壁缸套制造問題。
1.2 項目合同規定的任務
1)高壓大缸徑氣缸開發
?。╝)結構形式研究;(b)安全性研究;(c)耐磨性研究;(d)冷卻方式研究;(e)切削加工性研究。
2)高壓填料、活塞環設計研究
?。╝)填料耐磨性研究;(b)填料長壽命研究;(c)填料密封性研究;(d)活塞環、支撐環結構形式研究;(e)支撐環壓應力研究。
3)高壓冷卻器設計研究
?。╝)結構形式研究;(b)減振性研究;(c)抗疲勞研究;(d)降噪研究。
4)高壓容器研究
?。╝)高壓動載荷設計研究;(b)疲勞強度研究;(c)末級高精度過濾器研究。
5)壓縮機組振動控制研究
?。╝)脈動及振動的成因研究;(b)壓縮機組扭振分析;(c)整機脈動分析研究。
1.3 項目考核指標
?。?)主要技術指標(見表1)
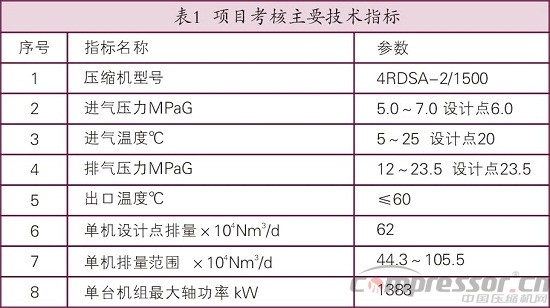
(2)主要經濟指標
通過成功進行天然氣儲氣庫壓縮機國產化研制,單機采購成本比同類型進口機組降低30%左右。
?。?)專有技術及論文
● 2項專有技術:高壓氣缸結構設計
氣缸缸套熱處理工藝
● 2項制造技術:高壓氣缸結構設計
氣缸缸套熱處理
● 發表論文1篇
2 項目實施情況
2.1 項目目標、任務總體完成情況
本項目完成合同規定的5項任務,研制出1臺儲氣庫壓縮機組,建立了1套技術規范,形成專利1項、專有技術2項、制造技術2項,發表論文2篇,培養技術骨干10人,全面完成各項考核任務。
?。?)全面完成合同要求的各項研究內容(見表2):
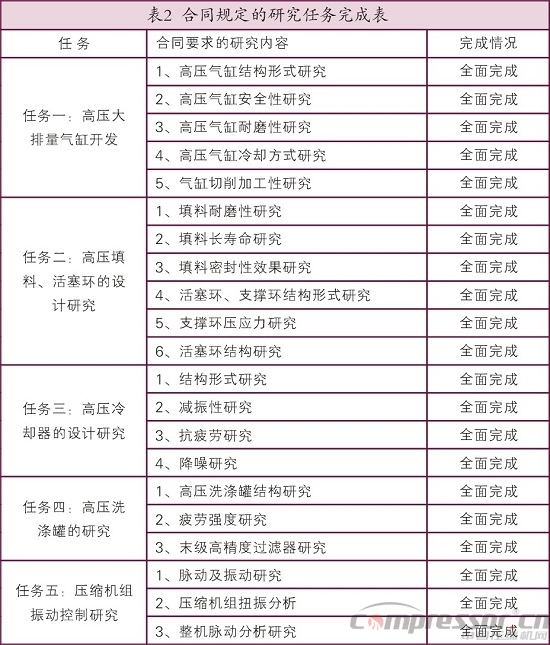
?。?)全面完成合同任務指標
1)預期成果完成情況
全面完成合同預期成果(見表3)。
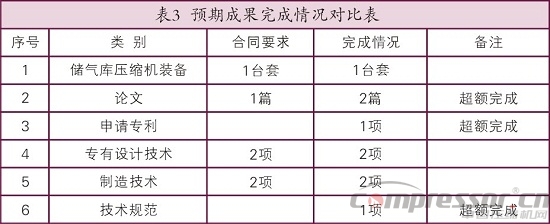
2)技術考核指標完成情況
項目的17項技術指標全部完成,達到考核要求(表4)
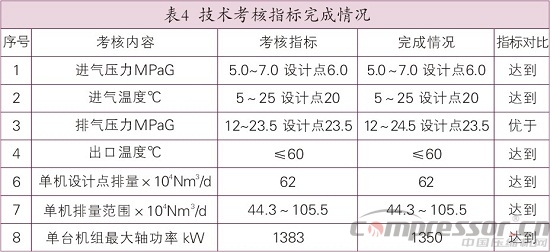
3)主要經濟指標
通過成功進行天然氣儲氣庫壓縮機國產化研制,單機采購成本比同類型進口機組降低50%左右(表5)。

4)完成廠內主要試驗(表6)
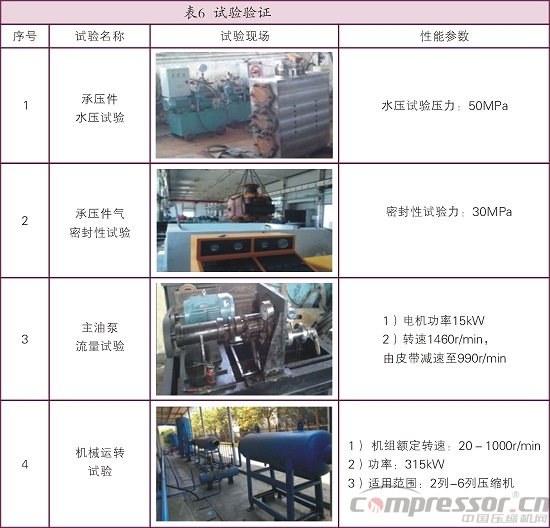
2.2 主要成果情況
通過本項目的開展與實施,形成4大核心成果(表7)。
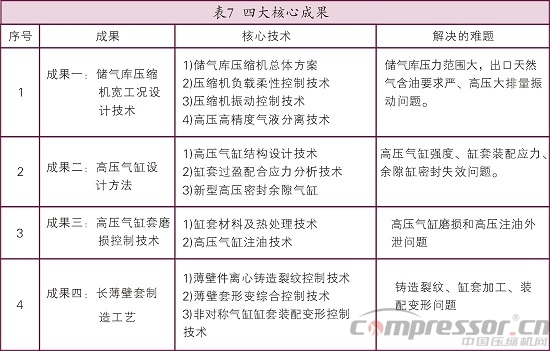
2.2.1 形成了儲氣庫壓縮機寬工況設計技術
通過熱力學專用軟件計算分析,研究壓縮機動力特性及振動控制分析,形成儲氣庫壓縮機主機配置及機組總體設計方案。
?。?)儲氣庫壓縮機總體方案
通過方案設計,提出二種主機配置方案進行對比分析,一種方案為四缸二級壓縮,一級氣缸兩個,二級氣缸兩個;另一種方案為二缸二級壓縮,一級氣缸一個,二級氣缸一個,二種方案的一級氣缸均配有可調余隙。
對兩種方案進行計算,通過分析可知:
1)四列機組比二列機組行程短,活塞線速度低;
2)四列機組比二列機組綜合桿載更小,提高了機組的安全性 ;
3)二列機組的氣體力較大,且反向角很小,為保證機組有一定的反向角,二級氣缸需要設置尾桿(貫穿活塞桿)。四列機組不存在反向角小的問題。
4)四列機組比二列機組的不平衡力矩要小,因此四列機組的振動要?。▓D1)。
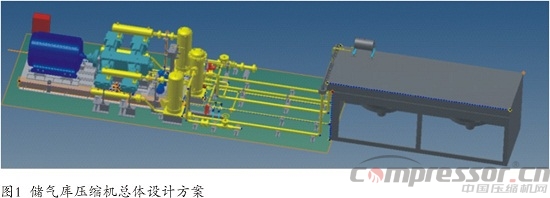
?。?)壓縮機負載柔性控制技術
1)壓縮機負載啟動柔性控制技術
研究壓縮過程負荷特性,采用遞階控制結構,創建壓縮機負載柔性控制方法,協調控制先導閥組與進氣閥門,適應高壓進氣變化,降低機組啟動負載。
2)壓縮機加/卸負載柔性控制技術
研究機組加\卸負載特性,采用模糊控制技術,創建負荷柔性調節方法,實現加載平穩漸進、卸載回流控制。避免加載對電網干擾、卸載高壓對罐體容器和安全閥沖擊。根據實時檢測排氣壓力變化值調整加載閥門關閉速度,使機組負載在一個合理的變化規律內緩慢增加,減小對電機軸承損害和對電網的干擾;根據實時檢測進、排壓力變化值調整閥門開啟速度,減小高壓氣回流對進氣洗滌罐內濾網的沖擊力,同時可保證卸載時機組進氣管線內壓力不超過安全閥工作設定值。
(3)壓縮機振動控制技術
采用API618規定的第三種方法進行氣流脈動分析,優化管線、支撐布置和緩沖罐結構,減小氣流脈動力,降低管線振動。
a) 壓縮機和管路系統的固有頻率分析
b) 壓縮機力學模型的受力機械響應分析
c) 管路系統受力機械響應(圖2)
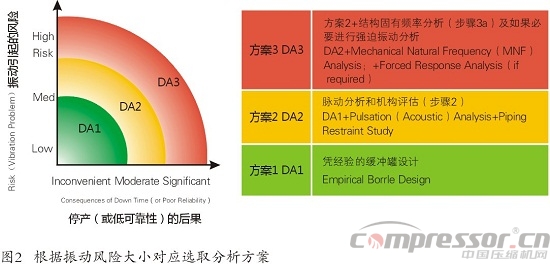
1)壓縮機振動控制技術軸系共振控制
針對壓縮機軸系進行了動力學分析。在往復式壓縮機軸系中施加活塞、連桿、十字頭以及驅動電機轉子等慣性質量的基本方法,建立考慮各種慣性質量的軸系動力學分析模型,選取了集總參數法,對軸系進行了簡化,將模型繼續簡化成有限個自由度的模型。在構成集總參數模型時,對軸系的總節點數N由一定的要求(圖3)
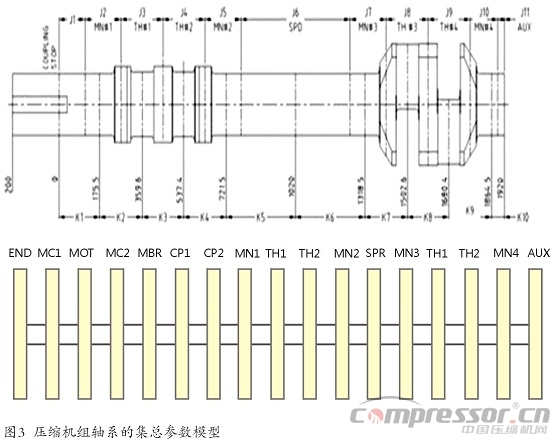
對軸系進行了簡化:分布質量離散化,集總到許多節點上,簡化成有限個自由度的分析模型(END~MBR為壓縮機軸,CP1~CP2為聯軸器,MN1~AUX為電機軸)。
?。ü街衂i為轉子第i個截面的受力和變形狀態的狀態矢量,Xi為截面的徑向位移,ai繞角,Mi為彎矩,Qi為剪力,l為軸段長度;E為材料的彈性模量;I為軸段的截面矩;V則為考慮截面上剪切影響的系數: 其中G為材料的切變模量;Ar為截面積,Kt為截面系數。)
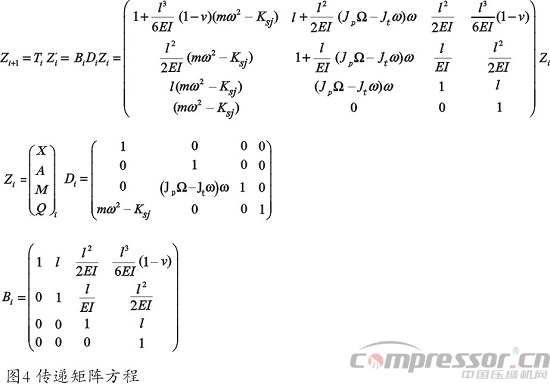
研究壓縮機動力特性,采用轉子動力學分析,建立了集總參數模型后,采用傳遞矩陣法(如圖4),建立這些構件兩端狀態矢量之間的傳遞關系,利用連續條件,得到整個軸系兩端截面的狀態矢量之間的關系式,再根據軸系的邊界條件就可導出頻率方程式,求解頻率方程式,得到軸系的各階固有頻率和振型,形成扭轉振動分析方法,掌握了扭振控制技術,避免軸系共振計算軸系臨界轉速和瞬態響應(圖5)。
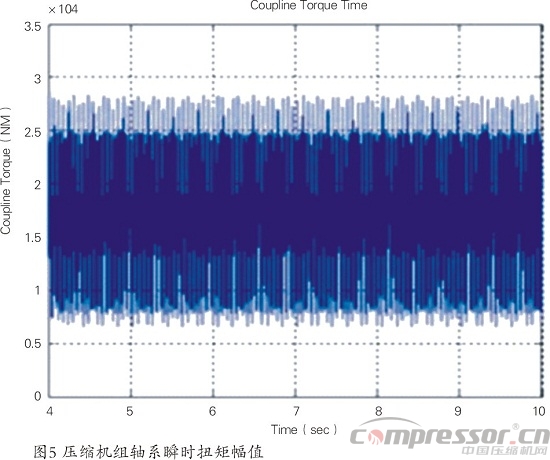
因整個軸系中,z*薄弱、z*有可能發生破壞的部件為聯軸器,分析得到軸系的響應幅值小于聯軸器許用扭矩值,確認軸系安全。
2)壓縮機振動控制技術-氣流脈動力控制
根據壓縮機氣流脈動聲學特性及聲阻抗網絡分析模型技術,建立壓縮機管系和元件結構的三維分析模型,提供管系和元件的振動分析數學模型??紤]環境因素(管系與外界的熱交換、環境噪聲等)的情況下,建立更加完善的數學模型和特征型方程組,分析儲氣庫工況要求,算了模型固有頻率及響應,形成脈動分析方法,掌握脈動控制技術,優化工藝氣管路設計(圖6,7,8)。
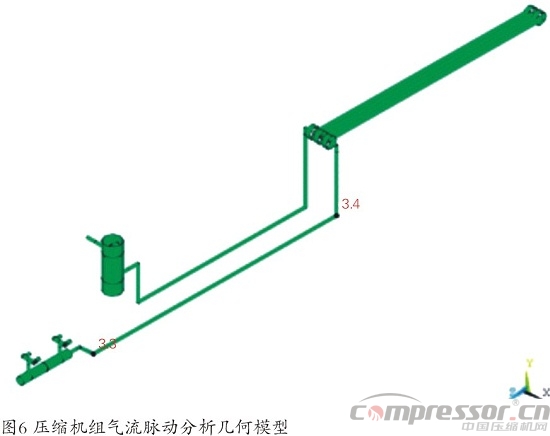
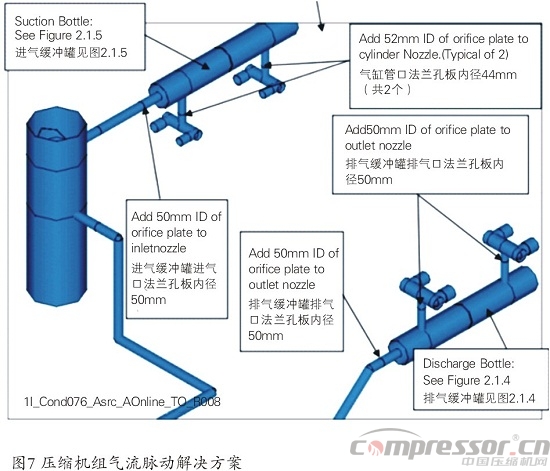
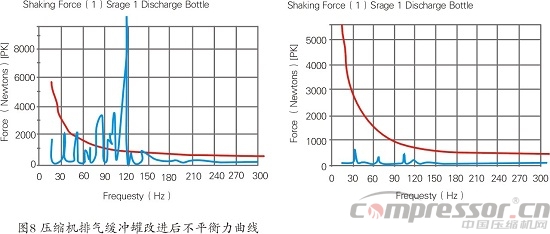
圖8左為排氣緩沖罐改進前不平衡力曲線圖,圖8右為排氣緩沖罐改進后的不平衡力曲線,紅色曲線為API618標準規定值。通過氣流脈動分析后,發現有些頻率段脈動不平衡力很大,通過改進設計后,降不平衡力降低到標準值以下。
3)壓縮機振動控制技術-機械振動控制
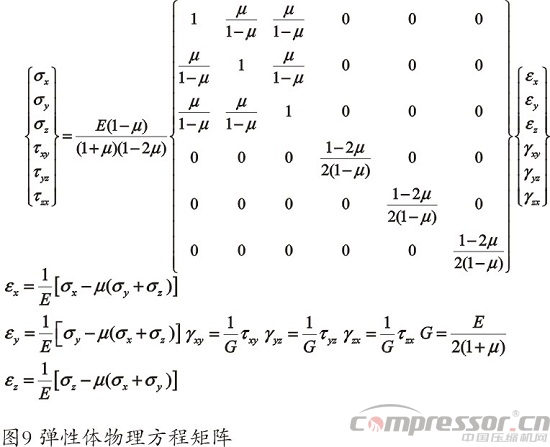
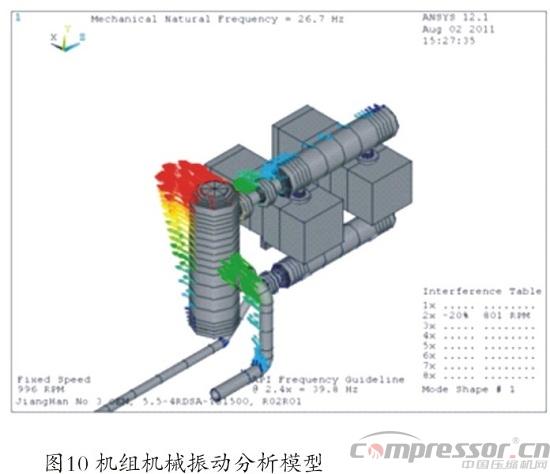
采用有限元分析理論,建立了彈性體物理方程矩陣(如圖9)和機組有限元模型(如圖10),找到其固有頻率及頻響特性,提出解決方案(如圖11),掌握機械振動分析方法,優化機組結構設計。
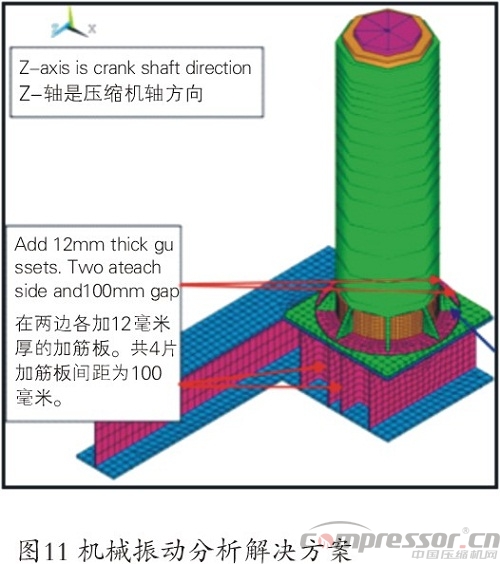
其中 為正應力, 為剪應力, 為彈性體沿X軸正方向的位移, 為Y軸正方向的位移, 為Z軸正方向的位移,G為剪切模量。
通過機械振動分析后,需要提高洗滌罐支撐座固有頻率,避免與機組發生共振。
?。?)高壓高精度氣液分離技術
1)論證了不同分離結構的過濾效果,形成高壓大排量高精度過濾分離方案,控制天然氣出口含液量低于1ppm。
2)分析液體的聚結特性,優選了“層壓法”處理過濾濾芯, 該濾芯不但可以滿足技術要求,并且極大延長了濾芯使用壽命,濾芯的z*大更換周期在18個月。采用“層壓法”聚結濾芯可將工藝氣流中的液體污染物去除至0.01ppmw以下,同時對天然氣中少量固體顆粒物的去除率為99.98%(0.3um以上)。該聚結濾芯在生產工藝中采用了疏油處理技術,可以將聚結液體在只占整個濾芯25-30%的底部排除,從而避免液沫夾帶現象,防止聚結液體潤濕介質,加速液體在介質纖維上的排出。
3)末級高壓分離器,因工作壓力變化范圍較大,氣流脈動影響較大,承受各種靜、動載荷或交變載荷,還有附加的機械或溫度載荷,情況很復雜。因此在設計時,選擇厚壁管補強,運用等面積補強法對末級分離器進口接管開孔進行補強設計,進行疲勞分析,評定結構承受疲勞載荷的能力,保證承受交變載荷的容器不致在其壽命期限內發生疲勞破壞。z*終設計出開式分段高壓高精度過濾器結構和專用液壓工具,解決了高壓大壁厚大通徑制造難題(圖12,13)。
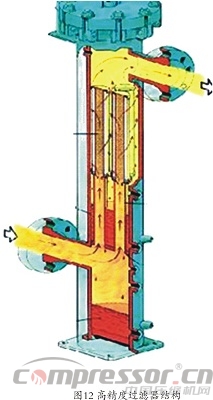
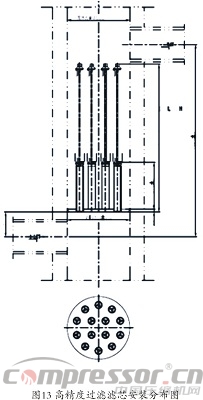
<本文未完待續,更多精彩見下期>
來源:中石化石油機械股份有限公司壓縮機分公司
【壓縮機網】1 項目概況
1.1 項目研究目標與難點
打破國外技術壁壘,掌握一批具有自主知識產權、達到國際同等水平的壓縮機設計、制造技術,實現25MPa高壓儲氣庫壓縮機的國產化,實現“零”的突破,提升儲氣庫壓縮機設計研發能力,為我國儲氣庫工程建設提供質優價廉、安全可靠的國產壓縮機,為我國儲氣庫工程建設提供大型、關鍵的國產化裝備保障,為國民經濟發展作出貢獻。
項目研發面臨四大難題:
儲氣庫壓縮機寬工況設計;高壓氣缸設計及密封問題;高壓氣缸套磨損控制;長薄壁缸套制造問題。
1.2 項目合同規定的任務
1)高壓大缸徑氣缸開發
?。╝)結構形式研究;(b)安全性研究;(c)耐磨性研究;(d)冷卻方式研究;(e)切削加工性研究。
2)高壓填料、活塞環設計研究
?。╝)填料耐磨性研究;(b)填料長壽命研究;(c)填料密封性研究;(d)活塞環、支撐環結構形式研究;(e)支撐環壓應力研究。
3)高壓冷卻器設計研究
?。╝)結構形式研究;(b)減振性研究;(c)抗疲勞研究;(d)降噪研究。
4)高壓容器研究
?。╝)高壓動載荷設計研究;(b)疲勞強度研究;(c)末級高精度過濾器研究。
5)壓縮機組振動控制研究
?。╝)脈動及振動的成因研究;(b)壓縮機組扭振分析;(c)整機脈動分析研究。
1.3 項目考核指標
?。?)主要技術指標(見表1)
(2)主要經濟指標
通過成功進行天然氣儲氣庫壓縮機國產化研制,單機采購成本比同類型進口機組降低30%左右。
?。?)專有技術及論文
● 2項專有技術:高壓氣缸結構設計
氣缸缸套熱處理工藝
● 2項制造技術:高壓氣缸結構設計
氣缸缸套熱處理
● 發表論文1篇
2 項目實施情況
2.1 項目目標、任務總體完成情況
本項目完成合同規定的5項任務,研制出1臺儲氣庫壓縮機組,建立了1套技術規范,形成專利1項、專有技術2項、制造技術2項,發表論文2篇,培養技術骨干10人,全面完成各項考核任務。
?。?)全面完成合同要求的各項研究內容(見表2):
?。?)全面完成合同任務指標
1)預期成果完成情況
全面完成合同預期成果(見表3)。
2)技術考核指標完成情況
項目的17項技術指標全部完成,達到考核要求(表4)
3)主要經濟指標
通過成功進行天然氣儲氣庫壓縮機國產化研制,單機采購成本比同類型進口機組降低50%左右(表5)。
4)完成廠內主要試驗(表6)
2.2 主要成果情況
通過本項目的開展與實施,形成4大核心成果(表7)。
2.2.1 形成了儲氣庫壓縮機寬工況設計技術
通過熱力學專用軟件計算分析,研究壓縮機動力特性及振動控制分析,形成儲氣庫壓縮機主機配置及機組總體設計方案。
?。?)儲氣庫壓縮機總體方案
通過方案設計,提出二種主機配置方案進行對比分析,一種方案為四缸二級壓縮,一級氣缸兩個,二級氣缸兩個;另一種方案為二缸二級壓縮,一級氣缸一個,二級氣缸一個,二種方案的一級氣缸均配有可調余隙。
對兩種方案進行計算,通過分析可知:
1)四列機組比二列機組行程短,活塞線速度低;
2)四列機組比二列機組綜合桿載更小,提高了機組的安全性 ;
3)二列機組的氣體力較大,且反向角很小,為保證機組有一定的反向角,二級氣缸需要設置尾桿(貫穿活塞桿)。四列機組不存在反向角小的問題。
4)四列機組比二列機組的不平衡力矩要小,因此四列機組的振動要?。▓D1)。
?。?)壓縮機負載柔性控制技術
1)壓縮機負載啟動柔性控制技術
研究壓縮過程負荷特性,采用遞階控制結構,創建壓縮機負載柔性控制方法,協調控制先導閥組與進氣閥門,適應高壓進氣變化,降低機組啟動負載。
2)壓縮機加/卸負載柔性控制技術
研究機組加\卸負載特性,采用模糊控制技術,創建負荷柔性調節方法,實現加載平穩漸進、卸載回流控制。避免加載對電網干擾、卸載高壓對罐體容器和安全閥沖擊。根據實時檢測排氣壓力變化值調整加載閥門關閉速度,使機組負載在一個合理的變化規律內緩慢增加,減小對電機軸承損害和對電網的干擾;根據實時檢測進、排壓力變化值調整閥門開啟速度,減小高壓氣回流對進氣洗滌罐內濾網的沖擊力,同時可保證卸載時機組進氣管線內壓力不超過安全閥工作設定值。
(3)壓縮機振動控制技術
采用API618規定的第三種方法進行氣流脈動分析,優化管線、支撐布置和緩沖罐結構,減小氣流脈動力,降低管線振動。
a) 壓縮機和管路系統的固有頻率分析
b) 壓縮機力學模型的受力機械響應分析
c) 管路系統受力機械響應(圖2)
1)壓縮機振動控制技術軸系共振控制
針對壓縮機軸系進行了動力學分析。在往復式壓縮機軸系中施加活塞、連桿、十字頭以及驅動電機轉子等慣性質量的基本方法,建立考慮各種慣性質量的軸系動力學分析模型,選取了集總參數法,對軸系進行了簡化,將模型繼續簡化成有限個自由度的模型。在構成集總參數模型時,對軸系的總節點數N由一定的要求(圖3)
對軸系進行了簡化:分布質量離散化,集總到許多節點上,簡化成有限個自由度的分析模型(END~MBR為壓縮機軸,CP1~CP2為聯軸器,MN1~AUX為電機軸)。
?。ü街衂i為轉子第i個截面的受力和變形狀態的狀態矢量,Xi為截面的徑向位移,ai繞角,Mi為彎矩,Qi為剪力,l為軸段長度;E為材料的彈性模量;I為軸段的截面矩;V則為考慮截面上剪切影響的系數: 其中G為材料的切變模量;Ar為截面積,Kt為截面系數。)
研究壓縮機動力特性,采用轉子動力學分析,建立了集總參數模型后,采用傳遞矩陣法(如圖4),建立這些構件兩端狀態矢量之間的傳遞關系,利用連續條件,得到整個軸系兩端截面的狀態矢量之間的關系式,再根據軸系的邊界條件就可導出頻率方程式,求解頻率方程式,得到軸系的各階固有頻率和振型,形成扭轉振動分析方法,掌握了扭振控制技術,避免軸系共振計算軸系臨界轉速和瞬態響應(圖5)。
因整個軸系中,z*薄弱、z*有可能發生破壞的部件為聯軸器,分析得到軸系的響應幅值小于聯軸器許用扭矩值,確認軸系安全。
2)壓縮機振動控制技術-氣流脈動力控制
根據壓縮機氣流脈動聲學特性及聲阻抗網絡分析模型技術,建立壓縮機管系和元件結構的三維分析模型,提供管系和元件的振動分析數學模型??紤]環境因素(管系與外界的熱交換、環境噪聲等)的情況下,建立更加完善的數學模型和特征型方程組,分析儲氣庫工況要求,算了模型固有頻率及響應,形成脈動分析方法,掌握脈動控制技術,優化工藝氣管路設計(圖6,7,8)。
圖8左為排氣緩沖罐改進前不平衡力曲線圖,圖8右為排氣緩沖罐改進后的不平衡力曲線,紅色曲線為API618標準規定值。通過氣流脈動分析后,發現有些頻率段脈動不平衡力很大,通過改進設計后,降不平衡力降低到標準值以下。
3)壓縮機振動控制技術-機械振動控制
采用有限元分析理論,建立了彈性體物理方程矩陣(如圖9)和機組有限元模型(如圖10),找到其固有頻率及頻響特性,提出解決方案(如圖11),掌握機械振動分析方法,優化機組結構設計。
其中 為正應力, 為剪應力, 為彈性體沿X軸正方向的位移, 為Y軸正方向的位移, 為Z軸正方向的位移,G為剪切模量。
通過機械振動分析后,需要提高洗滌罐支撐座固有頻率,避免與機組發生共振。
?。?)高壓高精度氣液分離技術
1)論證了不同分離結構的過濾效果,形成高壓大排量高精度過濾分離方案,控制天然氣出口含液量低于1ppm。
2)分析液體的聚結特性,優選了“層壓法”處理過濾濾芯, 該濾芯不但可以滿足技術要求,并且極大延長了濾芯使用壽命,濾芯的z*大更換周期在18個月。采用“層壓法”聚結濾芯可將工藝氣流中的液體污染物去除至0.01ppmw以下,同時對天然氣中少量固體顆粒物的去除率為99.98%(0.3um以上)。該聚結濾芯在生產工藝中采用了疏油處理技術,可以將聚結液體在只占整個濾芯25-30%的底部排除,從而避免液沫夾帶現象,防止聚結液體潤濕介質,加速液體在介質纖維上的排出。
3)末級高壓分離器,因工作壓力變化范圍較大,氣流脈動影響較大,承受各種靜、動載荷或交變載荷,還有附加的機械或溫度載荷,情況很復雜。因此在設計時,選擇厚壁管補強,運用等面積補強法對末級分離器進口接管開孔進行補強設計,進行疲勞分析,評定結構承受疲勞載荷的能力,保證承受交變載荷的容器不致在其壽命期限內發生疲勞破壞。z*終設計出開式分段高壓高精度過濾器結構和專用液壓工具,解決了高壓大壁厚大通徑制造難題(圖12,13)。
<本文未完待續,更多精彩見下期>
來源:中石化石油機械股份有限公司壓縮機分公司
網友評論
條評論
最新評論