【壓縮機網】轉子部件脫落可以說是壓縮機等旋轉設備中最為兇險的一類故障,尤其是對于一些超高轉速的壓縮機,葉輪外緣的線速度會接近聲速,在這種情況下,脫落的部件會帶有強大的動能,甚至足以擊穿機殼。對于轉速不那么高的機組,轉子部件脫落也會使轉子振幅產生突然變化,影響機組的正常運行,嚴重的可能會觸發聯鎖停車甚至引發事故,而且脫落部件可能會在慣性力的作用下飛出,發生二次事故。
轉子部件脫落常見部位
理論上轉子上的部件都有脫落的可能,實際現場比較常見的掉落部位包括壓縮機葉輪、汽輪機和煙機的葉片、拉筋、圍帶、輪齒、聯軸器部件等。
轉子部件脫落原因
導致轉子部件脫落的原因很多,比如安裝檢修后管道吹掃的不徹底,管道、機殼內部的焊渣、雜物在運行時被高壓氣體吹出來撞擊葉輪葉片造成破壞;再比如裝配時的一些部件預緊力不足,在長期振動下產生松動脫落;或者由于設計強度不足、局部材料缺陷等原因導致的失效斷裂等等。
是強度不足還是材料缺陷,亦或者是外力損傷,我們可以借助斷口分析工具來確定。斷口分析是金屬構件進行失效分析的重要手段,是研究金屬斷裂面的科學。金屬破斷后會形成斷口。斷口總是發生在金屬組織中最薄弱的地方,通過斷口的形態分析去研究一些斷裂的基本問題:如斷裂起因、斷裂性質、斷裂方式、斷裂機制、斷裂韌性、斷裂過程的應力狀態以及裂紋擴展速率等。
如果要求深入地研究材料的冶金因素和環境因素對斷裂過程的影響,通常還要進行斷口表面的微區成分分析、主體分析、結晶學分析和斷口的應力與應變分析等。
對斷口進行宏觀觀察的儀器主要是放大鏡(約10倍)和體視顯微鏡(從5~50倍)等。在很多情況下,利用宏觀觀察就可以判定斷裂的性質、起始位置和裂紋擴展路徑。但如果要對斷裂起點附近進行細致研究,分析斷裂原因和斷裂機制,還必須進行微觀觀察。
斷口的微觀觀察經歷了光學顯微鏡(觀察斷口的實用倍數是在50~500倍間)、透射電子顯微鏡(觀察斷口的實用倍數是在1000~40000倍間)和掃描電子顯微鏡(觀察斷口的實用倍數是在20~10000倍間)三個階段。
轉子部件脫落特征
既然轉子部件脫落特征危害如此之大,我們怎么才能做到快速準確的診斷呢?
由于轉子部件脫落本質是轉子平衡狀態的改變,所以它具備不平衡故障的一些基本特征,同時也有一些自身特點,具體如下:
1.振動的工頻值會在瞬間突然變化
2. 時域波形可見幅值突然變化或有沖擊信號(不常見)
有時葉片脫落時刻的信號剛好被采集存儲下來,則可以在時域波形上看到幅值的變化以及沖擊信號,但由于脫落瞬間很短暫,以及監測系統通常并不是連續采集和存儲的,所以不易見到。
3. 工頻振動的相位也可能會發生突變
請注意,這里面第一條說的是“突然變化”并不是突然升高;第二條工頻振動的相位也“可能”會發生突變。
4.突變后振值相位多趨于穩定
如果你所管理的設備在發生斷振動突變后振值和相位比較穩定,又沒有其他的復雜頻率成分,你要暗自慶幸一下,這說明設備目前只是發生了單次的部件脫落,并沒有引發連鎖反應。我們知道,流程工業的壓縮機、汽輪機為了效率和性能多會采用多級設計形式,氣體在設備中逐級通過。如果部件脫落發生在末級,脫落部分可能會隨著氣流進入管道,最終卡在濾網或者管道中的某個部位;如果脫落部位發生在前面幾級,情況就比較糟糕了,脫落的部分有可能隨著氣流進入到下一級,此時脫落部件與下一級葉片的相對速度是非常大的,發生碰撞會打傷更多的葉片,這些碎片再進入下一級,后果不堪設想,甚至會引發重大安全事故。
5.變化后的振動特征頻率多以工頻為主
轉子部件脫落故障本質與轉子不平衡機理相同,所以時域波形像正弦曲線,頻率成分以工頻為主,這里就不再贅述了。
6.軸心軌跡一般是渦動范圍比較大的橢圓或者接近正圓
由于轉子部件脫落多數情況會破壞原始的平衡狀態,使設備產生較大的不平衡量,所以軸心軌跡渦動范圍一般會比較大,如果沒有其他復合故障,軌跡形態多以橢圓為主。
7. 少部分原發性的部件脫落故障在脫落之前可能會有小幅的工頻和相位波動
如果設備不是受到異物撞擊產生的部件脫落,我們有可能有機會在部件完全從轉子上脫離之前發現一些征兆。因為一般來說,脫落也是有過程的,失效斷裂也是從裂紋逐漸變大發展形成的。
案例:某化工廠合成氣壓縮機斷葉片故障
某廠新裝合成氣機組由汽輪機驅動,工作機為離心壓縮機,共有7級葉輪分為2段,其中聯端為循環段,2級葉輪;非聯端為合成段,5級葉輪。壓縮機振動報警值為63.5μm,聯鎖停機值為88.9μm,聯鎖停機為“二取二”。機組總貌圖如右圖所示:
機組相關參數如下:
2017年7月8日晚21:53分,該合成氣機組壓縮機四個通道同時出現了振值大幅上漲的現象,從穩定運行時的25μm左右突跳至80μm左右,變化時間約為3秒鐘。同一時刻,汽輪機側的振值無明顯變化。查看相關工藝量參數,通過查看相關數據,確認該時間段內工藝方面未做大幅調整,機組干氣密封各監測數據也無異常;查看壓縮機四個通道的GAP電壓趨勢,可排除儀表方面的原因。
壓縮機4個通道振值出現突變前后主要是1X幅值的大幅改變,特別是壓縮機非聯端(合成段)通道1X幅值從12μm變化至70μm左右。而其它頻率分量幅值變化不大;查看1X相位趨勢,振值突變前后1X相位最大也有約30°左右的改變;波形圖內呈現正弦波,且重復性較好,初相位點較為穩定,波峰與波谷值相近;頻譜圖內以1X為主,2X,3X及低頻分量幅值較低;軸心軌跡呈現橢圓形,各點圓滑過渡,重復性較好,渦動方向為同步正進動。
機組于7月21日停機,在停機降速過程中,壓縮機四個通道振值隨轉速變化關系十分明顯,完全符合轉子部件脫落后不平衡故障的振動特征。在對機組進行拆解后,發現在合成段第5級葉輪的輪盤處有大約70*40*5mm左右的脫落,同時在此葉輪上還發現長度約70mm長的裂紋。
這起斷葉片故障很蹊蹺,如果是管道內異物撞擊,損傷的大概率應該是首級葉輪,而發生斷裂的卻是第5級葉輪,斷口也沒有發現明顯的材料缺陷,更像是疲勞損傷。為什么會在這個位置產生疲勞?
SIEMES ENERGY SECTOR的工程師 Sven Konig 和 NicoPetry 發表的一篇論文給了筆者啟發,文中提到兩起案例的葉輪的失效形式和這起很像。
論文中的第一個案例是一臺運行了6年的壓縮機第五級葉輪葉片斷裂。
論文中的第二個案例是三臺相同的天然氣壓縮機在改造后運行幾個月就出現了葉片斷裂,形式和第一個案例非常相似。
文中作者通過有限元計算,認為這種失效形式是特定頻率激發葉輪的某階固有頻率共振有關,共振時高頻交變應力導致葉輪局部產生疲勞斷裂,斷裂形狀和振型一致。
回到本文案例,由于現場工藝流程原因,機組長期在非設計工況運轉,經常達不到工作轉速6936,筆者推測在這種非設計運行工況下,激發了葉輪的某階固有頻率,最終導致了葉片的疲勞斷裂。
比較遺憾的是沒能拿到準確的葉輪原始設計數據,無法建立準確的模型,進行模態分析,所以推測最終沒有得到驗證,僅供參考。希望能給大家在分析故障原因時多提供一條思路。
轉子部件脫落常見部位
理論上轉子上的部件都有脫落的可能,實際現場比較常見的掉落部位包括壓縮機葉輪、汽輪機和煙機的葉片、拉筋、圍帶、輪齒、聯軸器部件等。
轉子部件脫落原因
導致轉子部件脫落的原因很多,比如安裝檢修后管道吹掃的不徹底,管道、機殼內部的焊渣、雜物在運行時被高壓氣體吹出來撞擊葉輪葉片造成破壞;再比如裝配時的一些部件預緊力不足,在長期振動下產生松動脫落;或者由于設計強度不足、局部材料缺陷等原因導致的失效斷裂等等。
是強度不足還是材料缺陷,亦或者是外力損傷,我們可以借助斷口分析工具來確定。斷口分析是金屬構件進行失效分析的重要手段,是研究金屬斷裂面的科學。金屬破斷后會形成斷口。斷口總是發生在金屬組織中最薄弱的地方,通過斷口的形態分析去研究一些斷裂的基本問題:如斷裂起因、斷裂性質、斷裂方式、斷裂機制、斷裂韌性、斷裂過程的應力狀態以及裂紋擴展速率等。
如果要求深入地研究材料的冶金因素和環境因素對斷裂過程的影響,通常還要進行斷口表面的微區成分分析、主體分析、結晶學分析和斷口的應力與應變分析等。
對斷口進行宏觀觀察的儀器主要是放大鏡(約10倍)和體視顯微鏡(從5~50倍)等。在很多情況下,利用宏觀觀察就可以判定斷裂的性質、起始位置和裂紋擴展路徑。但如果要對斷裂起點附近進行細致研究,分析斷裂原因和斷裂機制,還必須進行微觀觀察。
斷口的微觀觀察經歷了光學顯微鏡(觀察斷口的實用倍數是在50~500倍間)、透射電子顯微鏡(觀察斷口的實用倍數是在1000~40000倍間)和掃描電子顯微鏡(觀察斷口的實用倍數是在20~10000倍間)三個階段。
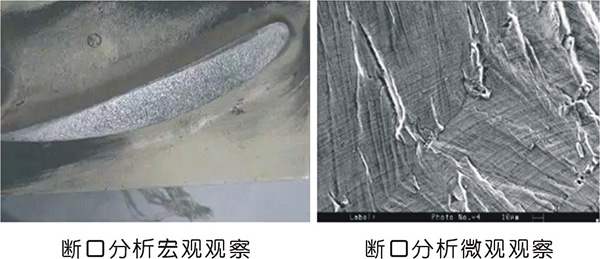
轉子部件脫落特征
既然轉子部件脫落特征危害如此之大,我們怎么才能做到快速準確的診斷呢?
由于轉子部件脫落本質是轉子平衡狀態的改變,所以它具備不平衡故障的一些基本特征,同時也有一些自身特點,具體如下:
1.振動的工頻值會在瞬間突然變化
2. 時域波形可見幅值突然變化或有沖擊信號(不常見)
有時葉片脫落時刻的信號剛好被采集存儲下來,則可以在時域波形上看到幅值的變化以及沖擊信號,但由于脫落瞬間很短暫,以及監測系統通常并不是連續采集和存儲的,所以不易見到。
3. 工頻振動的相位也可能會發生突變
請注意,這里面第一條說的是“突然變化”并不是突然升高;第二條工頻振動的相位也“可能”會發生突變。
4.突變后振值相位多趨于穩定
如果你所管理的設備在發生斷振動突變后振值和相位比較穩定,又沒有其他的復雜頻率成分,你要暗自慶幸一下,這說明設備目前只是發生了單次的部件脫落,并沒有引發連鎖反應。我們知道,流程工業的壓縮機、汽輪機為了效率和性能多會采用多級設計形式,氣體在設備中逐級通過。如果部件脫落發生在末級,脫落部分可能會隨著氣流進入管道,最終卡在濾網或者管道中的某個部位;如果脫落部位發生在前面幾級,情況就比較糟糕了,脫落的部分有可能隨著氣流進入到下一級,此時脫落部件與下一級葉片的相對速度是非常大的,發生碰撞會打傷更多的葉片,這些碎片再進入下一級,后果不堪設想,甚至會引發重大安全事故。
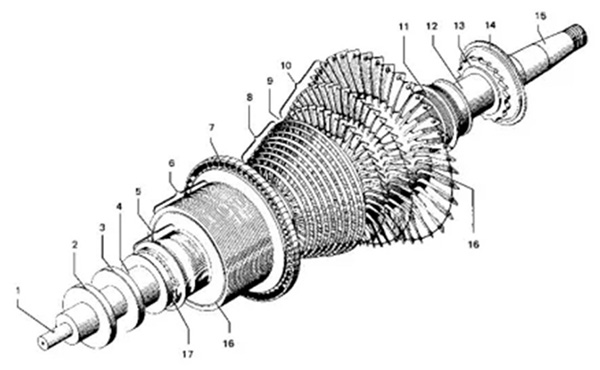
5.變化后的振動特征頻率多以工頻為主
轉子部件脫落故障本質與轉子不平衡機理相同,所以時域波形像正弦曲線,頻率成分以工頻為主,這里就不再贅述了。
6.軸心軌跡一般是渦動范圍比較大的橢圓或者接近正圓
由于轉子部件脫落多數情況會破壞原始的平衡狀態,使設備產生較大的不平衡量,所以軸心軌跡渦動范圍一般會比較大,如果沒有其他復合故障,軌跡形態多以橢圓為主。
7. 少部分原發性的部件脫落故障在脫落之前可能會有小幅的工頻和相位波動
如果設備不是受到異物撞擊產生的部件脫落,我們有可能有機會在部件完全從轉子上脫離之前發現一些征兆。因為一般來說,脫落也是有過程的,失效斷裂也是從裂紋逐漸變大發展形成的。
案例:某化工廠合成氣壓縮機斷葉片故障
某廠新裝合成氣機組由汽輪機驅動,工作機為離心壓縮機,共有7級葉輪分為2段,其中聯端為循環段,2級葉輪;非聯端為合成段,5級葉輪。壓縮機振動報警值為63.5μm,聯鎖停機值為88.9μm,聯鎖停機為“二取二”。機組總貌圖如右圖所示:
機組相關參數如下:
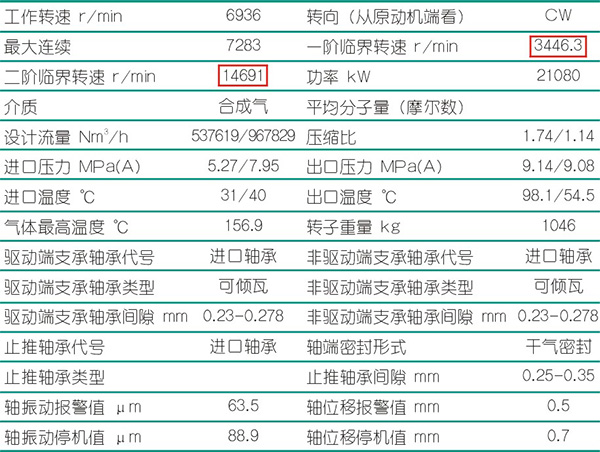
2017年7月8日晚21:53分,該合成氣機組壓縮機四個通道同時出現了振值大幅上漲的現象,從穩定運行時的25μm左右突跳至80μm左右,變化時間約為3秒鐘。同一時刻,汽輪機側的振值無明顯變化。查看相關工藝量參數,通過查看相關數據,確認該時間段內工藝方面未做大幅調整,機組干氣密封各監測數據也無異常;查看壓縮機四個通道的GAP電壓趨勢,可排除儀表方面的原因。
壓縮機4個通道振值出現突變前后主要是1X幅值的大幅改變,特別是壓縮機非聯端(合成段)通道1X幅值從12μm變化至70μm左右。而其它頻率分量幅值變化不大;查看1X相位趨勢,振值突變前后1X相位最大也有約30°左右的改變;波形圖內呈現正弦波,且重復性較好,初相位點較為穩定,波峰與波谷值相近;頻譜圖內以1X為主,2X,3X及低頻分量幅值較低;軸心軌跡呈現橢圓形,各點圓滑過渡,重復性較好,渦動方向為同步正進動。
機組于7月21日停機,在停機降速過程中,壓縮機四個通道振值隨轉速變化關系十分明顯,完全符合轉子部件脫落后不平衡故障的振動特征。在對機組進行拆解后,發現在合成段第5級葉輪的輪盤處有大約70*40*5mm左右的脫落,同時在此葉輪上還發現長度約70mm長的裂紋。
這起斷葉片故障很蹊蹺,如果是管道內異物撞擊,損傷的大概率應該是首級葉輪,而發生斷裂的卻是第5級葉輪,斷口也沒有發現明顯的材料缺陷,更像是疲勞損傷。為什么會在這個位置產生疲勞?
SIEMES ENERGY SECTOR的工程師 Sven Konig 和 NicoPetry 發表的一篇論文給了筆者啟發,文中提到兩起案例的葉輪的失效形式和這起很像。
論文中的第一個案例是一臺運行了6年的壓縮機第五級葉輪葉片斷裂。
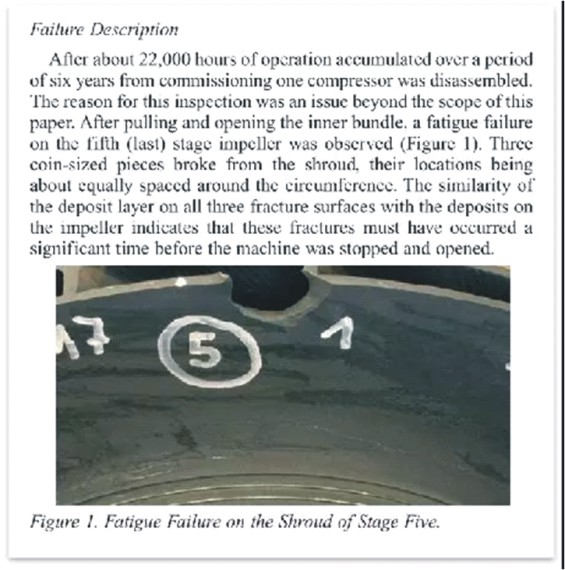
論文中的第二個案例是三臺相同的天然氣壓縮機在改造后運行幾個月就出現了葉片斷裂,形式和第一個案例非常相似。
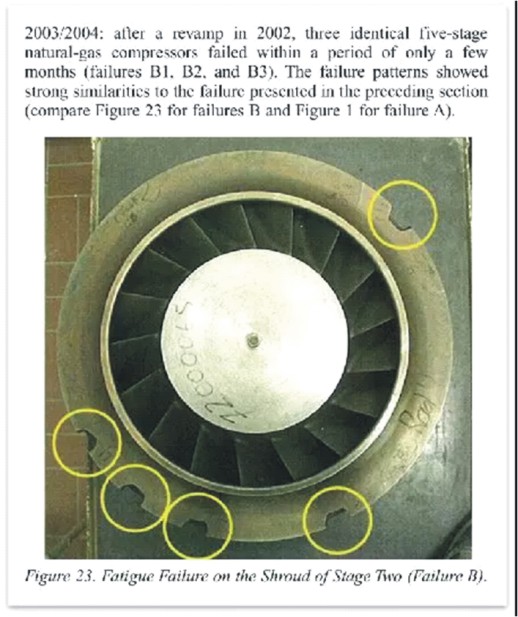
文中作者通過有限元計算,認為這種失效形式是特定頻率激發葉輪的某階固有頻率共振有關,共振時高頻交變應力導致葉輪局部產生疲勞斷裂,斷裂形狀和振型一致。

回到本文案例,由于現場工藝流程原因,機組長期在非設計工況運轉,經常達不到工作轉速6936,筆者推測在這種非設計運行工況下,激發了葉輪的某階固有頻率,最終導致了葉片的疲勞斷裂。
比較遺憾的是沒能拿到準確的葉輪原始設計數據,無法建立準確的模型,進行模態分析,所以推測最終沒有得到驗證,僅供參考。希望能給大家在分析故障原因時多提供一條思路。
網友評論
條評論
最新評論