【壓縮機網】乙烯項目EO/EG裝置建成,交付生產運行
2020年6月15日,乙烯項目20/50萬噸/年EO/EG裝置舉行中間交接儀式,標志著該裝置完成了建設,正式進入生產試運投產階段。
EO/EG裝置引進國外領先技術,2018年12月開始土建基礎施工,2020年6月15日實現工程中間交接,施工周期18個月,相比國內同類裝置建設工期處于領先水平。
EO/EG裝置是乙烯項目的核心裝置之一,消耗40%~50%的自產乙烯,在生產開工流程中不可或缺,EO/EG裝置能否順利建成中交,直接影響整個乙烯項目的開工進度。
01總體:時間緊、任務重
受工藝包引進等因素制約,項目開工建設比乙烯項目其它裝置晚6個月以上,且裝置工藝流程復雜,平面布置緊湊,施工作業面狹小,動靜設備大型化且數量眾多,最大的兩臺EO反應器重達1560噸,工藝管線直徑粗、管壁厚、焊接量大,最粗管徑2200mm,最大壁厚45mm,焊接當量33萬寸,施工難度非常高,施工工期壓力巨大,始終處于乙烯項目建設的關鍵路徑。
面對前所未有的困難與挑戰,項目建設團隊沒有退怯,相信辦法總比困難多,逢山開路、遇水搭橋。主要困難是關鍵設備制造進度普遍滯后,設備制造廠生產負荷飽滿,生產計劃一再推延,交貨最晚的塔器制造工期滯后約6個月。其次,關鍵吊裝機具資源緊缺,單臺EO反應器重1560噸。第三,2020年初新冠疫情爆發,延緩了節后施工人員復工計劃,嚴重影響施工進度;第四,EO/EG裝置采用E+P+C 模式,對業主建設團隊的項目管控能力提出了很高的挑戰。
針對設備到貨滯后問題,中化集團、中化能源領導親自催交EO/EG裝置反應器、關鍵塔器制造進度,乙烯項目部總經理唐匯云每月專項催交EO/EG裝置設備制造進度。另一方面,項目施工團隊根據設備到貨計劃不斷動態優化吊裝方案,千方百計縮小吊裝預留范圍,將設備到貨滯后造成的不利影響降至最低。
02團隊之工程管理
針對關鍵吊裝資源緊缺問題,積極協調吊裝公司,迅速調整吊裝方案,采用3200噸液化提升裝置進行吊裝,確保了EO反應器按期吊裝。
2020年初新冠疫情爆發之后,項目建設團隊不等不靠,主動作為。2月中旬,新冠疫情出現轉機之后,地方政府針對復工復產的相關政策發生變化,項目建設團隊迅速與中油一建溝通協調包機返程復工事宜,在短短兩天時間內,辦理完成了所有人員健康檢測及出行手續,2月24日第一批171名施工人員包機從鄭州返回施工現場,后續施工人員也陸續通過包機、包車等方式返回,解決了現場施工力量問題。
EO/EG裝置采用“E+P+C”的項目管理模式,對業主項目建設團隊是巨大考驗,乙烯項目部成立EO/EG裝置中交攻堅小組,集合設計、采購、設備技術、計劃控制、工程造價、施工管理、生產準備等各方面力量,加強專業協調與融合,提高溝通效率,有力地推動了項目進度。
項目建設期間,化學品項目分部主動安排晚上19點召開日協調會,會議經常持續到21點,分部多名員工常住廠區宿舍。
復工后現場加大施工力度,夜晚施工場景熱鬧非凡、燈火通明。
03團隊之生產運行
EO/EG裝置建設進展順利的背后,也離不開操作團隊的辛勤付出。生產運行團隊提前介入,與項目分部、施工承包商一并研究優化試車方案、試壓方案、沖洗和吹掃方案,通過見縫插針、交叉推進縮短工期。
在疫情還未完全消除的情況下,為了減輕建設團隊的壓力,裝置運行人員開始分批、分組進入裝置進行塔內件裝填、管線沖洗等工作,保證了現場建設的進度。
2020年5月11日,EO/EG裝置在外操間開展了三查四定工作的啟動會議,這意味著裝置向著開工吹起了沖鋒的號角。操作人員紛紛去現場查問題、找漏項,再經班長、工程師以總共同討論后,共計提出問題800余項,為開工減少隱患。
五一過后,裝置建設進行最后的沖刺,他們各司其職,互相協助,團結一致,攜手完成了裝置儀表點對點調校、循環水沖洗、管線水壓試驗以及全場3.7Mpag蒸汽吹掃等各類開工準備任務。
付出終將有回報,在參建各方的共同努力下,乙烯項目EO/EG裝置突破重重困難,實現工程中交。項目建設過程中未發生重大安全事故,工程質量可控,焊接拍片一次合格率98%以上,在受新冠疫情影響2個月的情況下,建設周期僅18個月。目前,項目團隊在為830投產繼續努力奮斗者。
來源:煤油一體化
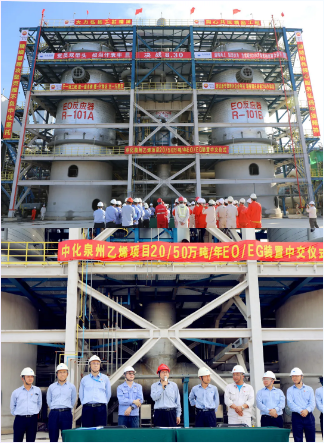
2020年6月15日,乙烯項目20/50萬噸/年EO/EG裝置舉行中間交接儀式,標志著該裝置完成了建設,正式進入生產試運投產階段。
EO/EG裝置引進國外領先技術,2018年12月開始土建基礎施工,2020年6月15日實現工程中間交接,施工周期18個月,相比國內同類裝置建設工期處于領先水平。
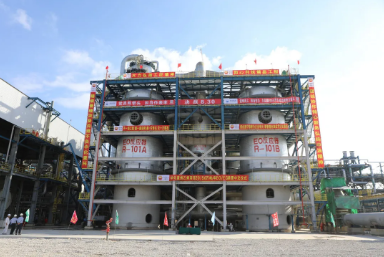
EO/EG裝置是乙烯項目的核心裝置之一,消耗40%~50%的自產乙烯,在生產開工流程中不可或缺,EO/EG裝置能否順利建成中交,直接影響整個乙烯項目的開工進度。
01總體:時間緊、任務重
受工藝包引進等因素制約,項目開工建設比乙烯項目其它裝置晚6個月以上,且裝置工藝流程復雜,平面布置緊湊,施工作業面狹小,動靜設備大型化且數量眾多,最大的兩臺EO反應器重達1560噸,工藝管線直徑粗、管壁厚、焊接量大,最粗管徑2200mm,最大壁厚45mm,焊接當量33萬寸,施工難度非常高,施工工期壓力巨大,始終處于乙烯項目建設的關鍵路徑。
面對前所未有的困難與挑戰,項目建設團隊沒有退怯,相信辦法總比困難多,逢山開路、遇水搭橋。主要困難是關鍵設備制造進度普遍滯后,設備制造廠生產負荷飽滿,生產計劃一再推延,交貨最晚的塔器制造工期滯后約6個月。其次,關鍵吊裝機具資源緊缺,單臺EO反應器重1560噸。第三,2020年初新冠疫情爆發,延緩了節后施工人員復工計劃,嚴重影響施工進度;第四,EO/EG裝置采用E+P+C 模式,對業主建設團隊的項目管控能力提出了很高的挑戰。
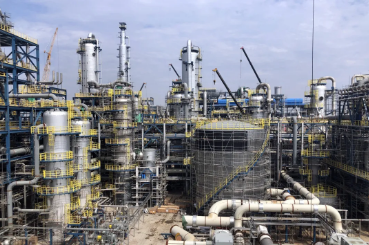
針對設備到貨滯后問題,中化集團、中化能源領導親自催交EO/EG裝置反應器、關鍵塔器制造進度,乙烯項目部總經理唐匯云每月專項催交EO/EG裝置設備制造進度。另一方面,項目施工團隊根據設備到貨計劃不斷動態優化吊裝方案,千方百計縮小吊裝預留范圍,將設備到貨滯后造成的不利影響降至最低。
02團隊之工程管理
針對關鍵吊裝資源緊缺問題,積極協調吊裝公司,迅速調整吊裝方案,采用3200噸液化提升裝置進行吊裝,確保了EO反應器按期吊裝。
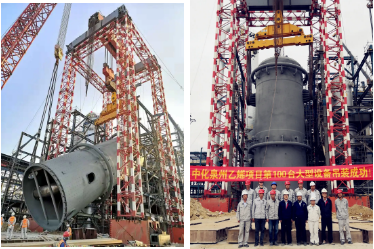
2020年初新冠疫情爆發之后,項目建設團隊不等不靠,主動作為。2月中旬,新冠疫情出現轉機之后,地方政府針對復工復產的相關政策發生變化,項目建設團隊迅速與中油一建溝通協調包機返程復工事宜,在短短兩天時間內,辦理完成了所有人員健康檢測及出行手續,2月24日第一批171名施工人員包機從鄭州返回施工現場,后續施工人員也陸續通過包機、包車等方式返回,解決了現場施工力量問題。
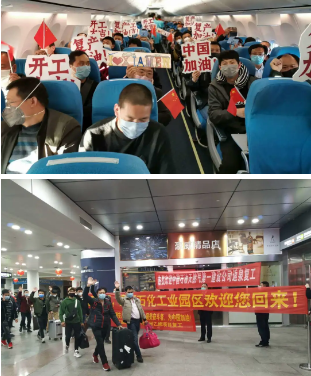
EO/EG裝置采用“E+P+C”的項目管理模式,對業主項目建設團隊是巨大考驗,乙烯項目部成立EO/EG裝置中交攻堅小組,集合設計、采購、設備技術、計劃控制、工程造價、施工管理、生產準備等各方面力量,加強專業協調與融合,提高溝通效率,有力地推動了項目進度。
項目建設期間,化學品項目分部主動安排晚上19點召開日協調會,會議經常持續到21點,分部多名員工常住廠區宿舍。
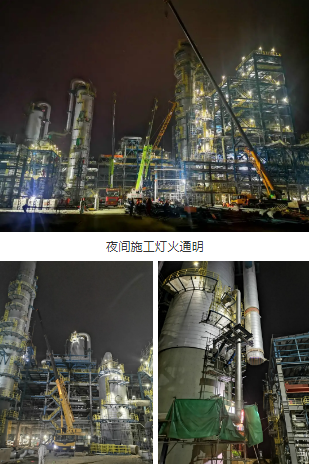
復工后現場加大施工力度,夜晚施工場景熱鬧非凡、燈火通明。
03團隊之生產運行
EO/EG裝置建設進展順利的背后,也離不開操作團隊的辛勤付出。生產運行團隊提前介入,與項目分部、施工承包商一并研究優化試車方案、試壓方案、沖洗和吹掃方案,通過見縫插針、交叉推進縮短工期。
在疫情還未完全消除的情況下,為了減輕建設團隊的壓力,裝置運行人員開始分批、分組進入裝置進行塔內件裝填、管線沖洗等工作,保證了現場建設的進度。
2020年5月11日,EO/EG裝置在外操間開展了三查四定工作的啟動會議,這意味著裝置向著開工吹起了沖鋒的號角。操作人員紛紛去現場查問題、找漏項,再經班長、工程師以總共同討論后,共計提出問題800余項,為開工減少隱患。
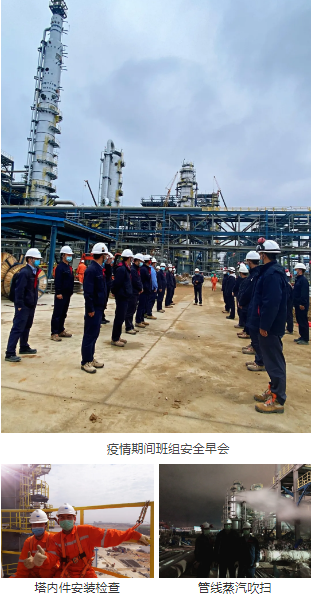
五一過后,裝置建設進行最后的沖刺,他們各司其職,互相協助,團結一致,攜手完成了裝置儀表點對點調校、循環水沖洗、管線水壓試驗以及全場3.7Mpag蒸汽吹掃等各類開工準備任務。
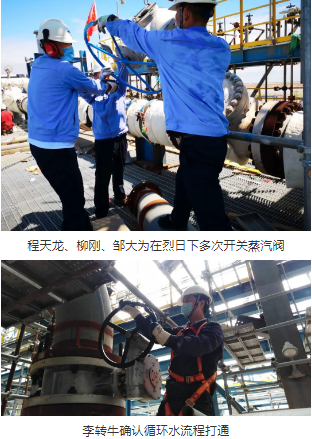
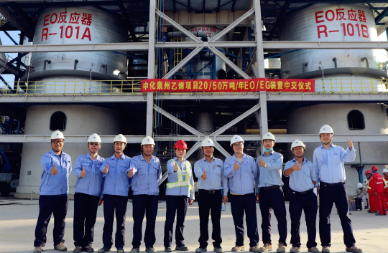
付出終將有回報,在參建各方的共同努力下,乙烯項目EO/EG裝置突破重重困難,實現工程中交。項目建設過程中未發生重大安全事故,工程質量可控,焊接拍片一次合格率98%以上,在受新冠疫情影響2個月的情況下,建設周期僅18個月。目前,項目團隊在為830投產繼續努力奮斗者。
來源:煤油一體化
網友評論
條評論
最新評論